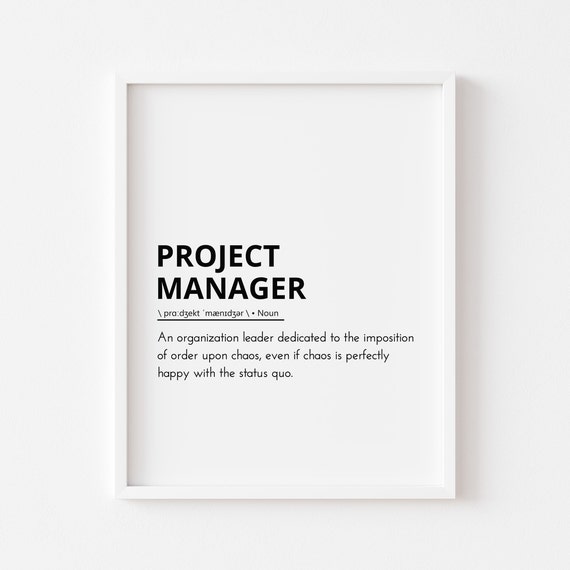
While HR systems are a vital part of any business, implementing a single solution is not always the best way to go. You should consider many factors when selecting a system. These factors include cost and embedded workflows. For some great tips on making the right decision, read on.
Process design
Creating an effective process design for HR systems requires careful consideration of the business requirements of the company. HR managers need to consider the company culture and employee types when creating an HR system. Managers should be open to ideas and flexible in implementing changes. Although the ideal HR system is not the most efficient for a business, managers must be flexible to find the right one for them.
Embedded workflows
The use of workflows in HR systems enables HR departments to automate tasks. HR teams can focus on more challenging tasks by automating their processes and simplify their HR data. These systems also allow for the storage of employee information, including personal and company information. This data can aid HR departments in employee development. You can, for example, create an organisational structure according to job duties and reporting arrangements. They can also create an organogram which helps to determine who reports.
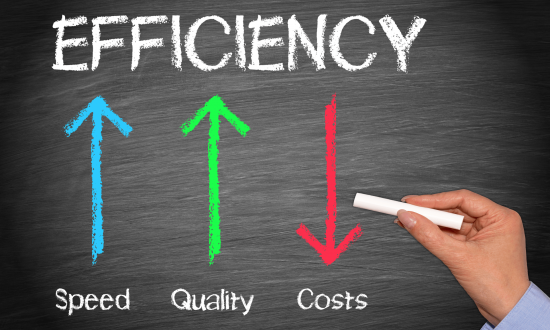
Automated processes
With the help of automation in HR systems, companies can now track data from different HR functions and analyse them to discover trends and patterns. This data can be used in order to identify trends and make improvements to employee experiences. A HR automation program can aid companies in process transparency, making it easier to make changes to benefits or processes.
Costs
Investing in HR Software can help you save money. It eliminates the need of multiple manual entry steps and eliminates mistakes. It can improve employee productivity as well as retention. It can be difficult to choose the right system. Before you invest, consider your budget as well as the number of users that you will require.
Modularity
Modularity in HR system design is the ability to create HR systems that are flexible and adaptable to your organization's needs. A typical unified HR system would need a large server to maintain. But a modular system allows you to buy only what you need as your business grows.
Recruiting
HRMS can improve the process of recruiting, but they are not all created equal. Although some are more sophisticated than others. The key to finding the right system for you is to make sure it meets your company's needs. You should also consider a HRMS that has robust candidate management capabilities if your company experiences high turnover. Also, consider whether the system you're considering can handle multi-state or international payroll scenarios. A system must also have an analysis function. This is useful in planning a workforce.
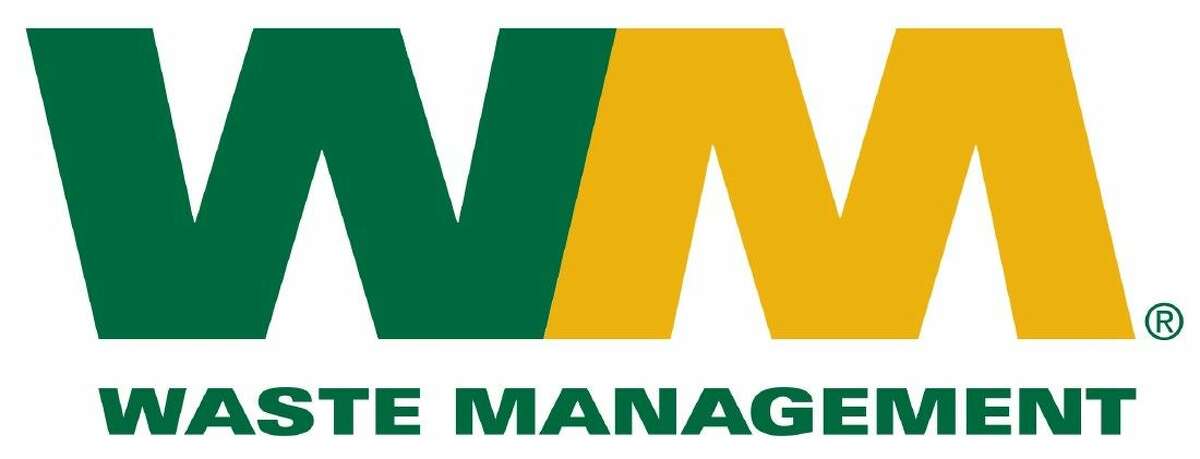
Onboarding
With HR systems software, HR professionals can create engaging onboarding experiences to new hires. These software solutions allow organizations to automate administrative tasks like hiring and training new employees. These systems are available separately or in combination with a comprehensive HR software package. These systems allow for 24/7 access to employee records and information.
FAQ
What are the three basic management styles?
The three major management styles are authoritarian (left-faire), participative and laissez -faire. Each style has its own strengths and weaknesses. Which style do your prefer? Why?
Autoritarian - The leader sets direction and expects everyone else to follow it. This style works best in large organizations that are stable and well-organized.
Laissez-faire is a leader who allows everyone to make their own decisions. This style works best when the organization is small and dynamic.
Participative: The leader listens to everyone's ideas and suggestions. This style is best for small organizations where everyone feels valued.
How can we create a successful company culture?
A positive company culture creates a sense of belonging and respect in its people.
It is based on three principles:
-
Everyone has something valuable to contribute
-
People are treated fairly
-
Individuals and groups can have mutual respect
These values reflect in how people behave. They will treat others with respect and kindness.
They will listen to other people's opinions respectfully.
They can also be a source of inspiration for others.
Additionally, the company culture encourages open communication as well as collaboration.
People are free to speak out without fear of reprisal.
They know that they will not be judged if they make mistakes, as long as the matter is dealt with honestly.
Finally, the company culture promotes honesty and integrity.
Everyone is aware that truth must be told.
Everyone understands there are rules that they must follow.
No one is entitled to any special treatment or favors.
What is a fundamental management tool for decision-making?
A decision matrix is an easy but powerful tool to aid managers in making informed decisions. They can think about all options and make informed decisions.
A decision matrix represents alternatives in rows and columns. This makes it easy to see how each alternative affects other choices.
This example shows four options, each represented by the boxes on either side of the matrix. Each box represents an option. The status quo (the current condition) is shown in the top row, and what would happen if there was no change?
The effect of Option 1 can be seen in the middle column. In this example, it would lead to an increase in sales of between $2 million and $3 million.
The effects of options 2 and 3 are shown in the next columns. These are positive changes - they increase sales by $1 million and $500 thousand respectively. These positive changes have their downsides. For instance, Option 2 increases cost by $100 thousand while Option 3 reduces profits by $200 thousand.
The final column shows results of choosing Option 4. This involves decreasing sales by $1 million.
The best part of using a decision-matrix is that it doesn't require you to know which numbers belong where. Simply look at the cells to instantly determine if one choice is better than the other.
This is because the matrix has already taken care of the hard work for you. Simply compare the numbers within the cells.
Here is an example how you might use the decision matrix in your company.
Advertising is a decision that you make. By doing so, you can increase your revenue by $5 000 per month. You will still have to pay $10000 per month in additional expenses.
The net result of advertising investment can be calculated by looking at the cell below that reads "Advertising." It is 15 thousand. Advertising is a worthwhile investment because it has a higher return than the costs.
How to effectively manage employees
Effectively managing employees means making sure they are productive and happy.
It also means having clear expectations of their behavior and keeping track of their performance.
Managers must be clear about their goals and those of their teams in order to succeed.
They should communicate clearly to staff members. They also need to make sure that they discipline and reward the best performers.
They must also keep track of the activities of their team. These include:
-
What was achieved?
-
What was the work involved?
-
Who did it all?
-
It was done!
-
Why?
This information can be used for monitoring performance and evaluating results.
Which kind of people use Six Sigma
People who have worked with statistics and operations research will usually be familiar with the concepts behind six sigma. However, anyone involved in any aspect of business can benefit from using it.
Because it requires a high degree of commitment, only leaders with strong leadership skills can implement it successfully.
What is the difference between Six Sigma Six Sigma and TQM?
The key difference between the two quality management tools is that while six-sigma focuses its efforts on eliminating defects, total quality management (TQM), focuses more on improving processes and reducing cost.
Six Sigma is a methodology for continuous improvement. This method emphasizes eliminating defects using statistical methods such p-charts, control charts, and Pareto analysis.
This method has the goal to reduce variation of product output. This is achieved by identifying and addressing the root causes of problems.
Total Quality Management involves monitoring and measuring every aspect of the organization. It also includes the training of employees to improve performance.
It is commonly used as a strategy for increasing productivity.
Statistics
- The BLS says that financial services jobs like banking are expected to grow 4% by 2030, about as fast as the national average. (wgu.edu)
- As of 2020, personal bankers or tellers make an average of $32,620 per year, according to the BLS. (wgu.edu)
- UpCounsel accepts only the top 5 percent of lawyers on its site. (upcounsel.com)
- Your choice in Step 5 may very likely be the same or similar to the alternative you placed at the top of your list at the end of Step 4. (umassd.edu)
- The profession is expected to grow 7% by 2028, a bit faster than the national average. (wgu.edu)
External Links
How To
How does Lean Manufacturing work?
Lean Manufacturing techniques are used to reduce waste while increasing efficiency by using structured methods. They were created in Japan by Toyota Motor Corporation during the 1980s. The aim was to produce better quality products at lower costs. Lean manufacturing seeks to eliminate unnecessary steps and activities in the production process. It has five components: continuous improvement and pull systems; just-in time; continuous change; and kaizen (continuous innovation). It is a system that produces only the product the customer requests without additional work. Continuous improvement is constantly improving upon existing processes. Just-in-time is when components and other materials are delivered at their destination in a timely manner. Kaizen refers to continuous improvement. It is achieved through small changes that are made continuously. The 5S acronym stands for sort in order, shine standardize and maintain. These five elements can be combined to achieve the best possible results.
Lean Production System
The lean production system is based on six key concepts:
-
Flow is about moving material and information as near as customers can.
-
Value stream mapping is the ability to divide a process into smaller tasks, and then create a flowchart that shows the entire process.
-
Five S’s - Sorted, In Order. Shine. Standardize. And Sustain.
-
Kanban – visual signals like colored tape, stickers or other visual cues are used to keep track inventory.
-
Theory of Constraints - Identify bottlenecks in the process, and eliminate them using lean tools such kanban boards.
-
Just-intime - Order components and materials at your location right on the spot.
-
Continuous improvement is making incremental improvements to your process, rather than trying to overhaul it all at once.