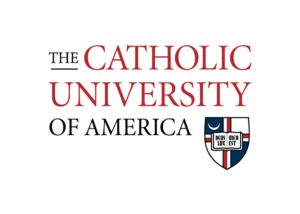
A priority matrix can be helpful in prioritizing tasks and organizing your to-dos according their urgency and importance. First, create a list of priorities. You can organize and map each item by writing it down in detail. If necessary, create separate lists for work and personal items. This will help you see how your to dos relate.
To organize your tasks according to importance and urgency, create a priority matrix
A priority matrix can help you manage your time and ensure you do the most important things first. It is possible to model your priorities numerically by using a simple 1-to-10 scale. Once you have identified your priorities, you can divide your workload into different quadrants by importance and urgency. You can delegate the more urgent items to others so you can plan your daily activities.
A priority matrix is an effective organizational tool, saving you time and money. It can be used to organize all types of work and can even be customized to suit your team or business. This system is used by many organizations to organize tasks according to their importance and urgency. It's also useful in project management and prioritization. This will allow you to identify which tasks are essential for your goals.
Todoist
Priorities are an important part of managing your time. Todoist makes it easy to prioritize tasks. It lets you organize tasks by priority levels and labels. You can assign each task a particular label or a priority level. Todoist also allows you to search for labels and sort tasks by priority level.
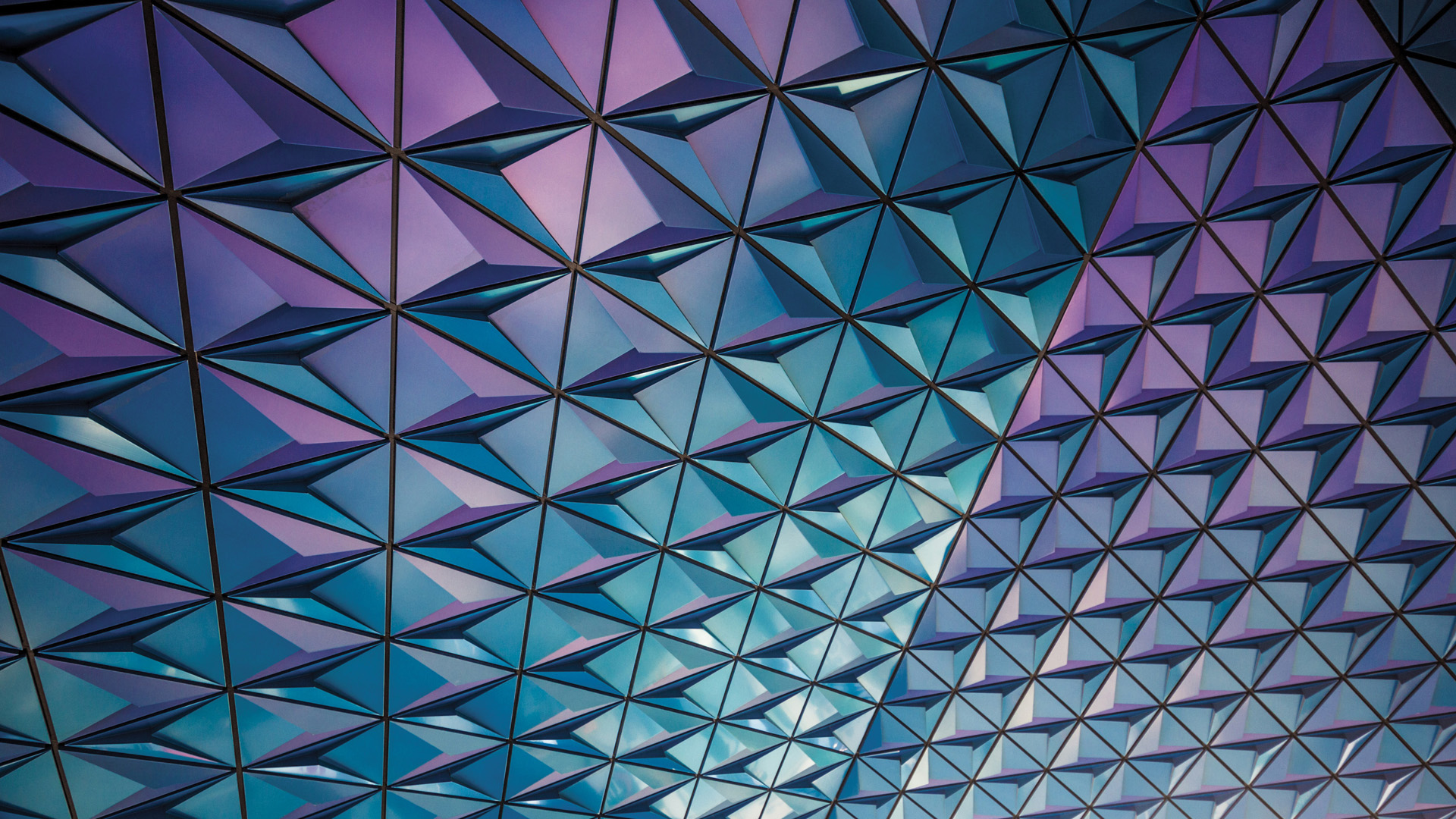
Todoist is highly customizable and works great for teams and product management. Using this system for managing your workload will help you get more done. It helps you plan your day and organizes tasks. Software uses the Getting Things Done technique to help you stay on top your tasks. It allows you to assign tasks to others and move them around to different inboxes.
Eisenhower matrix
The Eisenhower priorities matrix can help you prioritize and manage your time by identifying the most important. While some tasks may require immediate attention, others are less urgent but still require thoughtful planning. These tasks can be moved to the less urgent and important quadrants for consideration later. The Eisenhower matrix is an excellent tool for simplifying your to-do-list.
The Eisenhower priorities grid can be used to help prioritize tasks and reach long-term objectives. It can help you identify which tasks must be completed now and which ones should be deferred until later. The goal is to prioritize the most crucial tasks first.
PERT matrix
Project managers use the PERT matrix as one tool to plan and execute projects. It's a network made up of boxes that are numbered and represent different events during the project. These boxes are either circular or rectangular and are connected by labeled lines. Each box represents different tasks and activities that must be completed. Each box contains an indicator arrow that identifies a task sequence. The numbers on the boxes indicate how long each task should take. The team is responsible to follow the sequence in order to complete all activities.
This chart assists project managers in planning and meeting deadlines. The PERT matrix helps to keep projects on schedule by defining task dependencies. They can also visualize the project timeline.
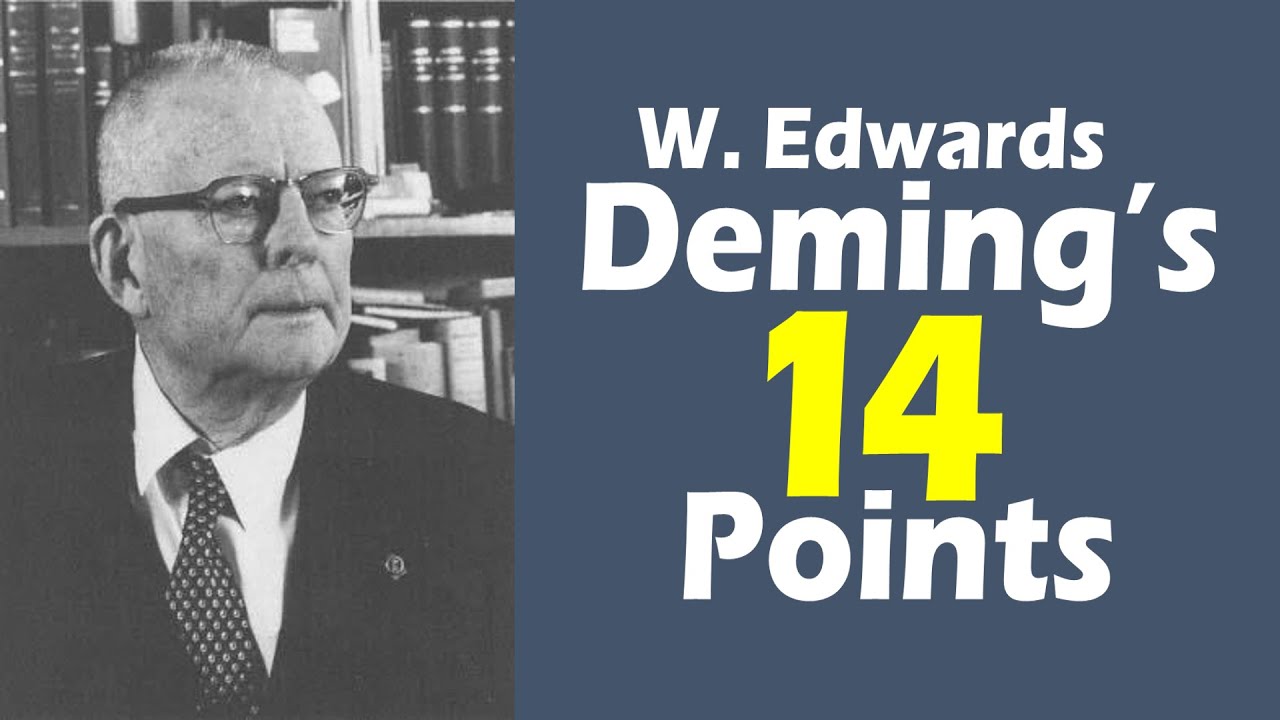
Idea prioritization matrix
Prioritizing ideas can be a crucial step in the innovation cycle. The idea prioritization matrix is a tool that helps teams prioritize ideas based on their feasibility, impact, and importance. Teams can also compare the merits between different ideas using the matrix. It is recommended to use a multidisciplinary team to develop a prioritization matrix.
A matrix of idea prioritization is used to rank the wish-list items in larger projects. If you are working on a website redesign, your team might have many ideas from different departments and stakeholders. Using a matrix is a great way to visually represent the top ideas that are most likely to be implemented during the development process.
FAQ
What is the difference between a project and a program?
A project is temporary, while a program lasts forever.
A project usually has a specific goal and deadline.
It is often carried out by a team of people who report back to someone else.
A program will usually have a set number of goals and objectives.
It is usually implemented by a single person.
What role can a manager fill in a company’s management?
Each industry has a different role for a manager.
A manager is generally responsible for overseeing the day to day operations of a company.
He/she makes sure that the company meets its financial obligations, and that it produces goods or services that customers desire.
He/she is responsible for ensuring that employees comply with all regulations and follow quality standards.
He/she oversees marketing campaigns and plans new products.
What are some common mistakes managers make when managing people?
Sometimes managers make their job harder than they need to.
They may not delegate enough responsibilities and not provide sufficient support.
Additionally, many managers lack communication skills that are necessary to motivate and direct their teams.
Managers set unrealistic expectations and make it difficult for their team.
Some managers may try to solve every problem themselves instead of delegating responsibility to others.
How can we create a culture of success in our company?
A successful company culture is one that makes people feel valued and respected.
It's based on three main principles:
-
Everyone has something valuable to contribute
-
People are treated fairly
-
There is mutual respect between individuals and groups
These values reflect in how people behave. They will treat others with consideration and courtesy.
They will respect the opinions of others.
These people will inspire others to share thoughts and feelings.
A company culture encourages collaboration and communication.
People feel free to express their views openly without fear of reprisal.
They are aware that mistakes can be accepted if they are treated honestly.
Finally, the company culture encourages honesty as well as integrity.
Everyone is aware that truth must be told.
Everyone knows that there are rules and regulations that apply to them.
No one is entitled to any special treatment or favors.
Statistics
- As of 2020, personal bankers or tellers make an average of $32,620 per year, according to the BLS. (wgu.edu)
- The profession is expected to grow 7% by 2028, a bit faster than the national average. (wgu.edu)
- The average salary for financial advisors in 2021 is around $60,000 per year, with the top 10% of the profession making more than $111,000 per year. (wgu.edu)
- Your choice in Step 5 may very likely be the same or similar to the alternative you placed at the top of your list at the end of Step 4. (umassd.edu)
- 100% of the courses are offered online, and no campus visits are required — a big time-saver for you. (online.uc.edu)
External Links
How To
How is Lean Manufacturing done?
Lean Manufacturing processes are used to reduce waste and improve efficiency through structured methods. They were developed in Japan by Toyota Motor Corporation (in the 1980s). The main goal was to produce products at lower costs while maintaining quality. Lean manufacturing is about eliminating redundant steps and activities from the manufacturing process. It consists of five basic elements: pull systems, continuous improvement, just-in-time, kaizen (continuous change), and 5S. It is a system that produces only the product the customer requests without additional work. Continuous improvement is constantly improving upon existing processes. Just-in–time refers when components or materials are delivered immediately to their intended destination. Kaizen stands for continuous improvement. Kaizen can be described as a process of making small improvements continuously. The 5S acronym stands for sort in order, shine standardize and maintain. These five elements are combined to give you the best possible results.
Lean Production System
Six key concepts make up the lean manufacturing system.
-
Flow - The focus is on moving information and material as close as possible to customers.
-
Value stream mapping- This allows you to break down each step of a process and create a flowchart detailing the entire process.
-
Five S’s - Sorted, In Order. Shine. Standardize. And Sustain.
-
Kanban: Use visual signals such stickers, colored tape, or any other visual cues, to keep track your inventory.
-
Theory of constraints: identify bottlenecks in your process and eliminate them using lean tools, such as kanban board.
-
Just-in-time delivery - Deliver components and materials right to your point of use.
-
Continuous improvement - make incremental improvements to the process rather than overhauling it all at once.