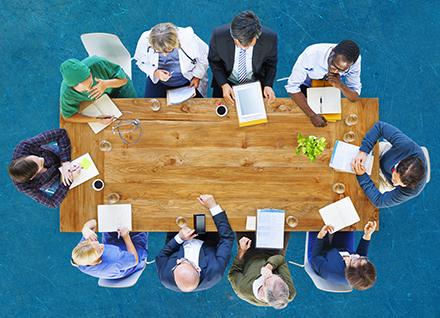
Value at risk is a calculation that estimates the possible loss on investments. Normally, this calculation estimates how much an investment can lose in a single day. It can also consider other factors like market volatility. This calculation is vital for any investor in stocks or bonds. This calculation will allow you to determine the best investments for you, according to your risk tolerance. Also, you can use the value at risk calculation to plan your retirement strategy.
Probability to lose a certain sum depending on how much is being risked
Probabilities are used when we invest to determine our chances of success. There is a 12% chance we'll lose our $10,000 invested in stocks. Loss refers to the amount of money that was lost as a result of a failure. For example, we could lose $5,000 on an investment and suffer $4000 of damage. It is important to note that probability does not guarantee a successful outcome.
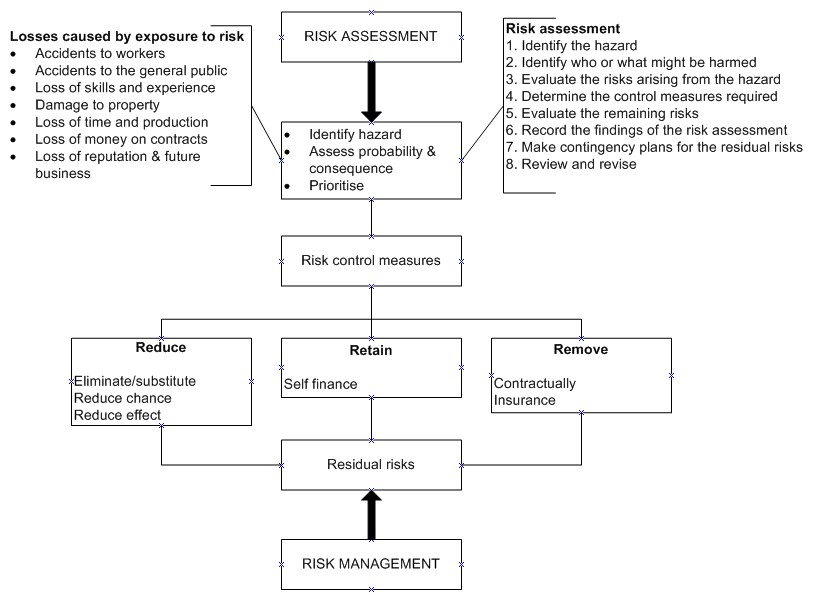
Calculation of VaR
To determine the level of risk associated with any investment, value at Risk is an important tool. Value at risk measures the probability of losing money based on the past performance of the investment. It also takes current market conditions into account. This calculation can be used for calculating the average loss within a portfolio. The calculation of value-at-risk is straightforward. The expected loss in 5% equals the portfolio's percentage value.
Monte Carlo method
The Monte Carlo technique is widely used in financial risks management. It is one of the most powerful approaches to VAR, because it is flexible and allows for a wide range of scenarios. Simulations can be used to account for complex pricing patterns as well as nonlinear exposures. This method can also be used to develop more complicated models and measure risk. However, there are limitations to this approach.
Historical method
Popular in investing is the Historical method of Value at Risk (VaR). This method uses historical data to calculate risk factors and then applies those values to current market prices. It is a straightforward and intuitive way to calculate VaR, which corresponds to a maximum loss over a specified period. It is important to note that a VaR calculation is only as good as the number of correct data points it uses. To maximize its accuracy, it is imperative to capture changing market dynamics, such as a major crisis.
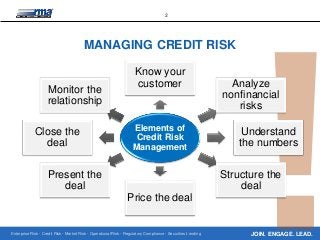
Effects of VaR upon liquidity
Value at Risk, also known as VaR, measures an asset's riskiness. It is the ratio of the asset's current value and its expected future value. It is the most common measure of risk among financial institutions. This concept is based upon a mathematical model that only considers rare events. The risk distribution can be parametric. This means that the mass of the distribution is at the mean and the tails are at a low point. In the FTSE, there are five such days within a 25 years period.
FAQ
How does a manager develop his/her management skills?
It is important to have good management skills.
Managers need to monitor their subordinates' performance.
You must quickly take action if your subordinate fails to perform.
It is essential to know what areas need to be improved and how to do it.
What are some common management mistakes?
Sometimes managers make their job harder than they need to.
They may not be able to delegate enough responsibility to staff or provide adequate support.
In addition, many managers lack the communication skills required to motivate and lead their teams.
Some managers set unrealistic expectations for their staff.
Managers may prefer to solve every problem for themselves than to delegate responsibility.
What is the difference in Six Sigma and TQM?
The main difference between these two quality-management tools is that six-sigma concentrates on eliminating defects while total QM (TQM), focuses upon improving processes and reducing expenses.
Six Sigma is an approach for continuous improvement. This method emphasizes eliminating defects using statistical methods such p-charts, control charts, and Pareto analysis.
This method attempts to reduce variations in product output. This is done by identifying and correcting the root causes of problems.
Total Quality Management involves monitoring and measuring every aspect of the organization. It also includes the training of employees to improve performance.
It is used to increase productivity.
Why is Six Sigma so popular?
Six Sigma can be implemented quickly and produce impressive results. Six Sigma also gives companies a framework for measuring improvement and helps them focus on what is most important.
What is the difference in leadership and management?
Leadership is all about influencing others. Management is about controlling others.
Leaders inspire others, managers direct them.
A leader motivates people and keeps them on task.
A leader develops people; a manager manages people.
What are management principles?
Management Concepts are the principles and practices managers use to manage people and resources. These topics include job descriptions, performance evaluations and training programs. They also cover human resource policies, job description, job descriptions, job descriptions, employee motivation, compensation systems, organizational structures, and many other topics.
What is TQM and how can it help you?
The quality movement was born during the industrial revolution when manufacturing companies realized they could not compete on price alone. To remain competitive, they had to improve quality as well as efficiency.
Management realized the need to improve and created Total Quality Management, which focused on improving all aspects within an organization's performance. It included continual improvement processes, employee involvement, customer satisfaction, and customer satisfaction.
Statistics
- 100% of the courses are offered online, and no campus visits are required — a big time-saver for you. (online.uc.edu)
- This field is expected to grow about 7% by 2028, a bit faster than the national average for job growth. (wgu.edu)
- The average salary for financial advisors in 2021 is around $60,000 per year, with the top 10% of the profession making more than $111,000 per year. (wgu.edu)
- The BLS says that financial services jobs like banking are expected to grow 4% by 2030, about as fast as the national average. (wgu.edu)
- Our program is 100% engineered for your success. (online.uc.edu)
External Links
How To
How can Lean Manufacturing be done?
Lean Manufacturing is a method to reduce waste and increase efficiency using structured methods. They were developed by Toyota Motor Corporation in Japan during the 1980s. The aim was to produce better quality products at lower costs. Lean manufacturing emphasizes removing unnecessary steps from the production process. It includes five main elements: pull systems (continuous improvement), continuous improvement (just-in-time), kaizen (5S), and continuous change (continuous changes). The production of only what the customer needs without extra work is called pull systems. Continuous improvement is constantly improving upon existing processes. Just-in time refers to components and materials being delivered right at the place they are needed. Kaizen refers to continuous improvement. It is achieved through small changes that are made continuously. Five-S stands for sort. It is also the acronym for shine, standardize (standardize), and sustain. These five elements work together to produce the best results.
Lean Production System
Six key concepts are the basis of lean production:
-
Flow: The goal is to move material and information as close as possible from customers.
-
Value stream mapping - break down each stage of a process into discrete tasks and create a flowchart of the entire process;
-
Five S's – Sort, Put In Order Shine, Standardize and Sustain
-
Kanban - use visual signals such as colored tape, stickers, or other visual cues to keep track of inventory;
-
Theory of Constraints - Identify bottlenecks in the process, and eliminate them using lean tools such kanban boards.
-
Just-in Time - Send components and material directly to the point-of-use;
-
Continuous improvement - make incremental improvements to the process rather than overhauling it all at once.