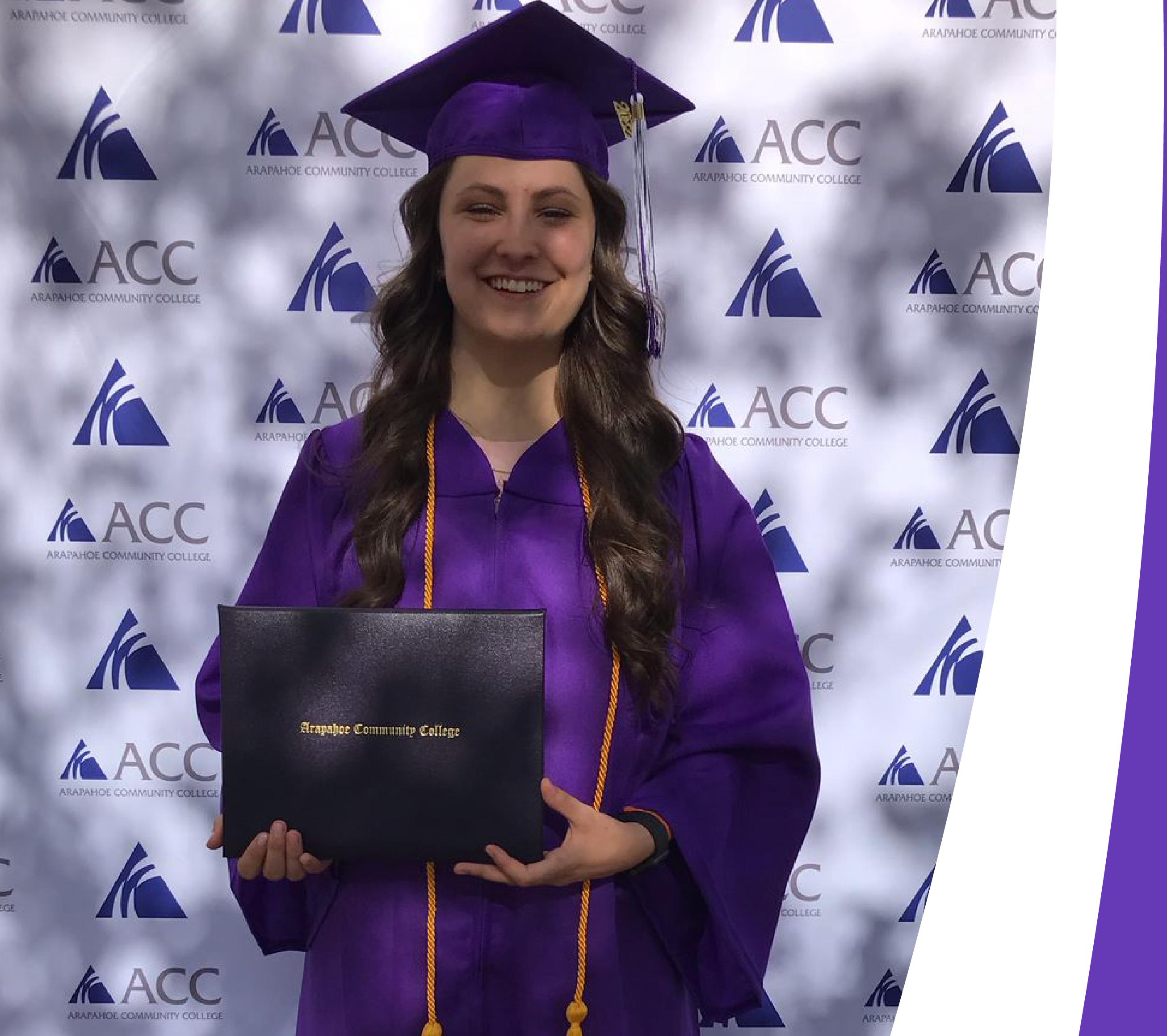
Accreditation is necessary for those who are interested in a career in construction management. Accreditation ensures that the college or university meets the standards for the profession it prepares its graduates. Find out more about the accreditation options available including ABET and ACCE.
ABET accreditation ensures that a college/university's program meets the requirements of the profession in which it prepares graduates.
The ABET accreditation process certifies that a college/university program meets quality standards. It prepares its graduates for success in their chosen career. ABET's voluntary peer reviewing process is highly regarded and adds value for technical programs.
A group of volunteers is responsible for ABET’s voluntary accreditation process. They represent industry, government, academia, private practice, and academia. The team's work is focused on the quality of the program's curriculum, faculty, and institutional support.

ACCE accreditation
ACCE accreditation for construction management programs is a valuable asset to prospective students, employers, and employees. Accredited programs offer students the skills, knowledge and experience necessary to be successful in a career in construction management. Accreditation makes it easier for employers find qualified employees. Accredited programs can also foster leadership development, foster networking and keep abreast of construction trends.
The American Council for Construction Education (ACCE) accredits two levels of education in construction management: the Associate of Applied Science and the Bachelor of Science. For the Bachelor's degree, you must complete a capstone course as well as internships within three year. Both programs require an average GPA of 3.0 as well as a minimum GRE score not less than 550. A few academic requirements are met and applicants may be allowed up to nine credits transfer from another institution. ACCE accreditation is rigorous. Accredited programs in construction management education must meet industry requirements.
ABET accreditation
ABET accreditation for construction management programs is a great way to ensure quality education and to ensure that the program content is approved by an external, independent governing body. Accreditation Boards for Engineering Technology (ABET), usually grant accreditation to construction management programs. Programs must meet certain standards in order to be accredited by ABET. Accredited programs make sure that students are ready for careers in technical fields, and they stay current with new technologies.
Some schools may have multiple curricula, which are not all accredited with the same ABET. The curriculum might contain core courses that are common to both programs in such cases. This may create competition for students and a risk of overextending resources.
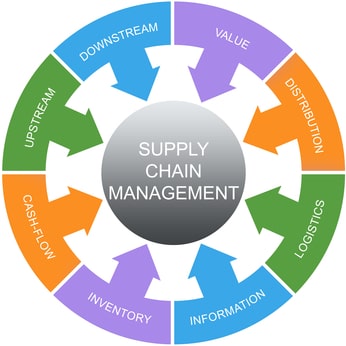
Louisiana State University accreditation
Louisiana State University offers a master's in construction management. This will equip you with the knowledge and skills to manage a construction project. This program teaches you how to plan, design, and deliver construction projects. You'll also learn how to integrate sustainable practices into the construction process. This program, which is accredited by American Council for Construction Education (ACCE), combines core construction courses with leadership coursework. This will allow you to be a skilled construction manager.
Whether you're looking for a career in construction management, or are just interested in the field as a career change, Louisiana State University offers an online Bachelor of Science in Construction Management. This program consists in six CM courses. These will provide you with a basic knowledge base of the field. Once you have completed the requirements of the program, you will gain an unique perspective on this field.
FAQ
What is a fundamental management tool for decision-making?
A decision matrix is a simple but powerful tool for helping managers make decisions. They can think about all options and make informed decisions.
A decision matrix is a way to organize alternatives into rows and columns. This allows you to easily see how each choice affects others.
This example shows four options, each represented by the boxes on either side of the matrix. Each box represents an option. The top row depicts the current status quo, while the bottom row represents what would happen if no action was taken.
The effect of Option 1 can be seen in the middle column. It would translate into an increase in sales from $2million to $3million.
The next two columns show the effects of choosing Options 2 and 3. These are both positive changes that increase sales by $1million and $500,000. They also have negative consequences. Option 2 increases the cost of goods by $100,000. Option 3 decreases profits and makes them less attractive by $200,000.
Finally, the last column shows the results of choosing Option 4. This will result in sales falling by $1,000,000
The best part about using a decision matrix to guide you is that you don’t need to keep track of which numbers go where. It's easy to see the cells and instantly know if any one of them is better than another.
The matrix already does all the work. Simply compare the numbers within the cells.
Here is an example of how a decision matrix might be used in your business.
You need to decide whether to invest in advertising. If you do, you'll be able to increase your revenue by $5 thousand per month. You will still have to pay $10000 per month in additional expenses.
The net result of advertising investment can be calculated by looking at the cell below that reads "Advertising." It is 15 thousand. Therefore, you should choose to invest in advertising since it is worth more than the cost involved.
What are the main management skills?
Business owners need to have management skills, no matter how small or large they may be. These skills include the ability manage people, finances and resources as well as other factors.
These skills are necessary for setting goals and objectives as well as planning strategies, leading groups, motivating employees and solving problems.
As you can see there is no end to the number of managerial tasks.
What is the difference between leadership and management?
Leadership is about being a leader. Management is about controlling others.
A leader inspires followers while a manager directs workers.
Leaders inspire people to achieve success. Managers keep their workers focused.
A leader develops people; a manager manages people.
What are some common mistakes managers make?
Sometimes managers make their job harder than they need to.
They may not be able to delegate enough responsibility to staff or provide adequate support.
Many managers lack the communication skills to motivate and lead their employees.
Some managers set unrealistic expectations for their staff.
Managers may attempt to solve all problems themselves, rather than delegating it to others.
Why is it important that companies use project management methods?
Project management techniques ensure that projects run smoothly while meeting deadlines.
This is because most businesses rely heavily on project work to produce goods and services.
Companies need to manage these projects efficiently and effectively.
Companies that do not manage their projects effectively risk losing time, money, or reputation.
What are management concepts, you ask?
Management concepts are the fundamental principles and practices that managers use when managing people and their resources. These topics include job descriptions, performance evaluations and training programs. They also cover human resource policies, job description, job descriptions, job descriptions, employee motivation, compensation systems, organizational structures, and many other topics.
Statistics
- As of 2020, personal bankers or tellers make an average of $32,620 per year, according to the BLS. (wgu.edu)
- Our program is 100% engineered for your success. (online.uc.edu)
- Hire the top business lawyers and save up to 60% on legal fees (upcounsel.com)
- The profession is expected to grow 7% by 2028, a bit faster than the national average. (wgu.edu)
- UpCounsel accepts only the top 5 percent of lawyers on its site. (upcounsel.com)
External Links
How To
How can Lean Manufacturing be done?
Lean Manufacturing uses structured methods to reduce waste, increase efficiency and reduce waste. These processes were created by Toyota Motor Corporation, Japan in the 1980s. It was designed to produce high-quality products at lower prices while maintaining their quality. Lean manufacturing is about eliminating redundant steps and activities from the manufacturing process. It is composed of five fundamental elements: continuous improvement; pull systems, continuous improvements, just-in–time, kaizen, continuous change, and 5S. Pull systems are able to produce exactly what the customer requires without extra work. Continuous improvement refers to continuously improving existing processes. Just-in-time refers to when components and materials are delivered directly to the point where they are needed. Kaizen means continuous improvement, which is achieved by implementing small changes continuously. Five-S stands for sort. It is also the acronym for shine, standardize (standardize), and sustain. These five elements work together to produce the best results.
Lean Production System
Six key concepts form the foundation of the lean production system:
-
Flow - focuses on moving information and materials as close to customers as possible.
-
Value stream mapping - break down each stage of a process into discrete tasks and create a flowchart of the entire process;
-
Five S’s - Sorted, In Order. Shine. Standardize. And Sustain.
-
Kanban – visual signals like colored tape, stickers or other visual cues are used to keep track inventory.
-
Theory of Constraints - Identify bottlenecks in the process, and eliminate them using lean tools such kanban boards.
-
Just-in-time - deliver components and materials directly to the point of use;
-
Continuous improvement - make incremental improvements to the process rather than overhauling it all at once.