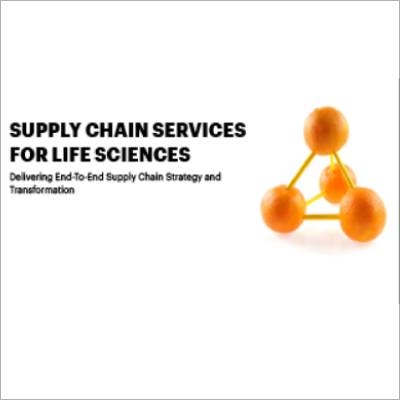
There are many factors to consider when determining if your workplace is OSHA compliant. One of these factors is paying attention to details and adhering fully to all standards. Other factors include creating a safe work environment and making sure that inspections are conducted. By following these guidelines, you will be on your way to being OSHA compliant.
Attention to detail
Attention to detail is a key aspect of making a product OSHA compliant. While this may seem obvious, OSHA regulations require careful consideration. OSHA standards will ensure that your workplace is safe. You'll need to pay close attention to detail.
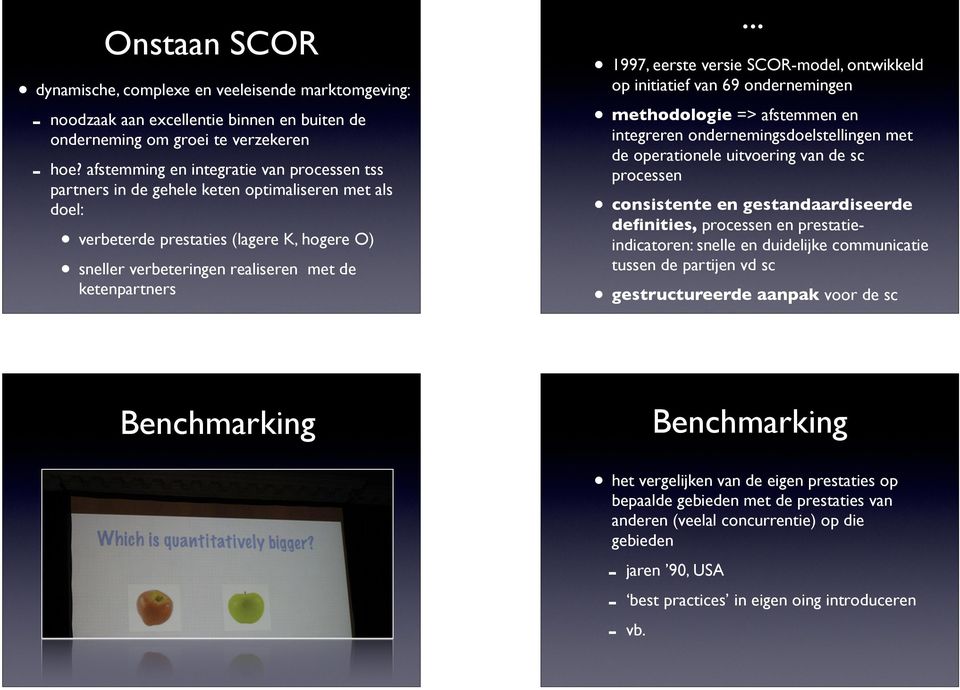
Conforming to all rules and standards
OSHA's rule-making process is based upon Advance Notices. These notices solicit information from interested parties regarding proposed changes. These notices detail the proposed rule, and provide a specific time for public comment. After this period, interested parties can request a public hearing, which is typically scheduled for a specific date.
Creating a safe working environment
For any company, safety is a top priority. However, even with the best intentions, accidents can still happen. Employers should remind employees about workplace safety. Employers should review their safety manuals against the recommended practices.
Inspections
OSHA-compliant inspections are conducted by a compliance officer who comes to your workplace with a purpose. These inspections are brief and designed to gain a better understanding of the operation of your business. The inspector will examine your safety and discuss with you privately. He or she may also review your records. The inspector will work with your company to find the best way to prevent or eliminate hazards. He/she will keep the inspection short and efficient.
Penalties
OSHA compliance penalty are a key part of workplace safety. There are three types OSHA penalties: repeated violations, willful violations and failure to abate violations. For each of these offenses, a fine can range from $1,036 up to $14,502 for a first offense. The penalties for repeated violations are even greater, as repeat violations are often more severe and can even result in jail time.

Resources
OSHA is an acronym that stands for the Safety of Workplaces. Congress passed the OSH Act on December 7, 1970. It establishes federal standards for workplace safety. It also offers resources to small businesses such as training, filing reports and raising safety concerns.
FAQ
What are the 3 basic management styles?
There are three types of management: participative, laissez faire, and authoritarian. Each style is unique and has its strengths as well as weaknesses. Which style do YOU prefer? Why?
Autoritarian – The leader sets the direction for everyone and expects them to follow. This style works best if the organization is large and stable.
Laissez-faire: The leader lets each person decide for themselves. This style is most effective when the organization's size and dynamics are small.
Participative – The leader listens and takes in ideas from all. This style works best in smaller organizations where everyone feels valued.
Why is Six Sigma so popular?
Six Sigma is easy to implement and can produce significant results. It also provides a framework for measuring improvements and helps companies focus on what matters most.
What is Kaizen?
Kaizen is a Japanese term which means "continuous improvement." This philosophy encourages employees to continually look for ways to improve the work environment.
Kaizen is a belief that everyone should have the ability to do their job well.
Why does it sometimes seem so hard to make good business decisions
Complex systems with many moving parts are the hallmark of businesses. Their leaders must manage multiple priorities, as well as dealing with uncertainty.
The key to making good decisions is to understand how these factors affect the system as a whole.
This requires you to think about the purpose and function of each component. Then, you need to think about how these pieces interact with one another.
It is also worth asking yourself if you have any unspoken assumptions about how you have been doing things. If not, you might want to revisit them.
If you're still stuck after all this, try asking someone else for help. They might have different perspectives than you, and could offer insight that could help you solve your problem.
What's the difference between a program and a project?
A project is temporary, while a program lasts forever.
Projects usually have a goal and a deadline.
It is usually done by a group that reports back to another person.
A program typically has a set goal and objective.
It is typically done by one person.
Why is it important that companies use project management methods?
Project management techniques can be used to ensure smooth project execution and meeting deadlines.
Because most businesses depend heavily on project work to produce goods or services,
These projects must be managed efficiently and effectively by companies.
Without effective project management, companies may lose money, time, and reputation.
Statistics
- The BLS says that financial services jobs like banking are expected to grow 4% by 2030, about as fast as the national average. (wgu.edu)
- Hire the top business lawyers and save up to 60% on legal fees (upcounsel.com)
- 100% of the courses are offered online, and no campus visits are required — a big time-saver for you. (online.uc.edu)
- This field is expected to grow about 7% by 2028, a bit faster than the national average for job growth. (wgu.edu)
- As of 2020, personal bankers or tellers make an average of $32,620 per year, according to the BLS. (wgu.edu)
External Links
How To
How can you implement the Kaizen technique?
Kaizen means continuous improvement. The Japanese philosophy emphasizes small, incremental improvements to achieve continuous improvement. This term was created by Toyota Motor Corporation in 1950. It's where people work together in order to improve their processes constantly.
Kaizen is one method that Lean Manufacturing uses to its greatest advantage. Kaizen is a concept where employees in charge of the production line are required to spot problems during the manufacturing process before they become major issues. This way, the quality of products increases, and the cost decreases.
Kaizen is a way to raise awareness about what's happening around you. It is important to correct any problems immediately if they are discovered. If someone is aware of a problem at work, he/she should inform his/her manager immediately.
Kaizen is based on a few principles. Start with the end product, and then move to the beginning. To improve our factory, for example, we need to fix the machines that produce the final product. Next, we fix the machines which produce components. And finally, we fix the workers who work directly with those machines.
This approach is called 'kaizen' because it focuses on improving everything steps by step. Once the factory is fixed, we return to the original site and work our way back until we get there.
It is important to understand how to measure the effectiveness and implementation of kaizen in your company. There are many ways you can determine if kaizen has been implemented well. Another method is to see how many defects are found on the products. Another way is determining how much productivity increased after implementing kaizen.
A good way to determine whether kaizen has been implemented is to ask why. Is it because the law required it or because you want to save money. Did you really believe it would lead to success?
Suppose you answered yes to any of these questions, congratulations! Now you're ready for kaizen.