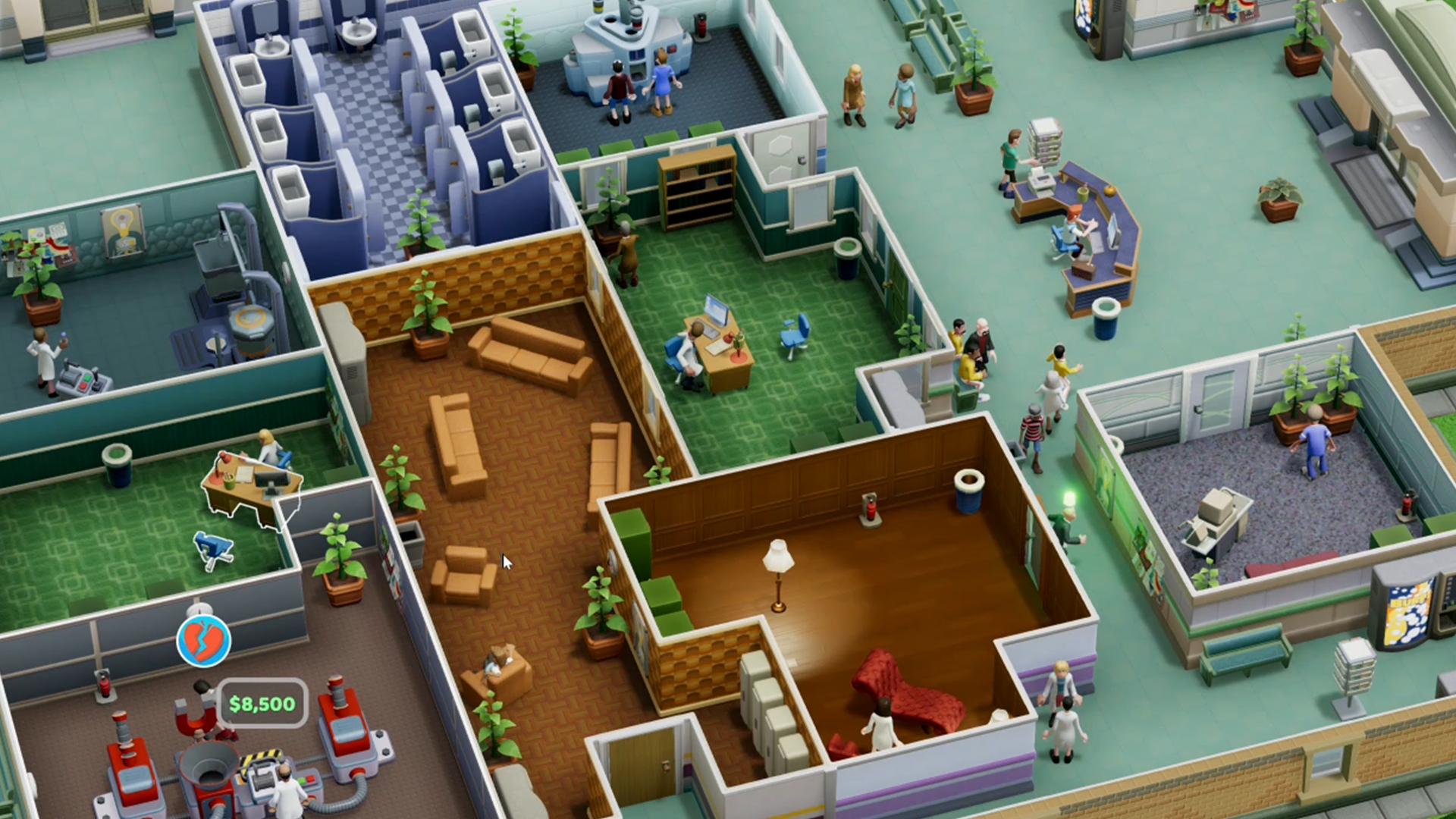
Model risk is a danger that can be caused by the use of inaccurate models. This risk is often associated with the valuation of financial securities. This is a difficult risk to manage. Model risk is a result of unrealistic or inaccurate assumptions. It is an operational risk. Financial institutions should be aware that model risk can still be a concern.
Model risk can be subsets of operational risk
Model risk refers to the risks associated with predictive models being used in business processes. These models can be extremely valuable but also come with a higher risk, especially if they're not properly built or don't make accurate predictions. Bad models can have devastating consequences so it is essential to manage this risk. Fortunately, automated machine learning can help to reduce this risk.
Model risk affects the firm creating and using the model more than the model itself. A model that is incorrectly or incomplete could result in inaccurate or erroneous results which can adversely affect the business's financial performance.
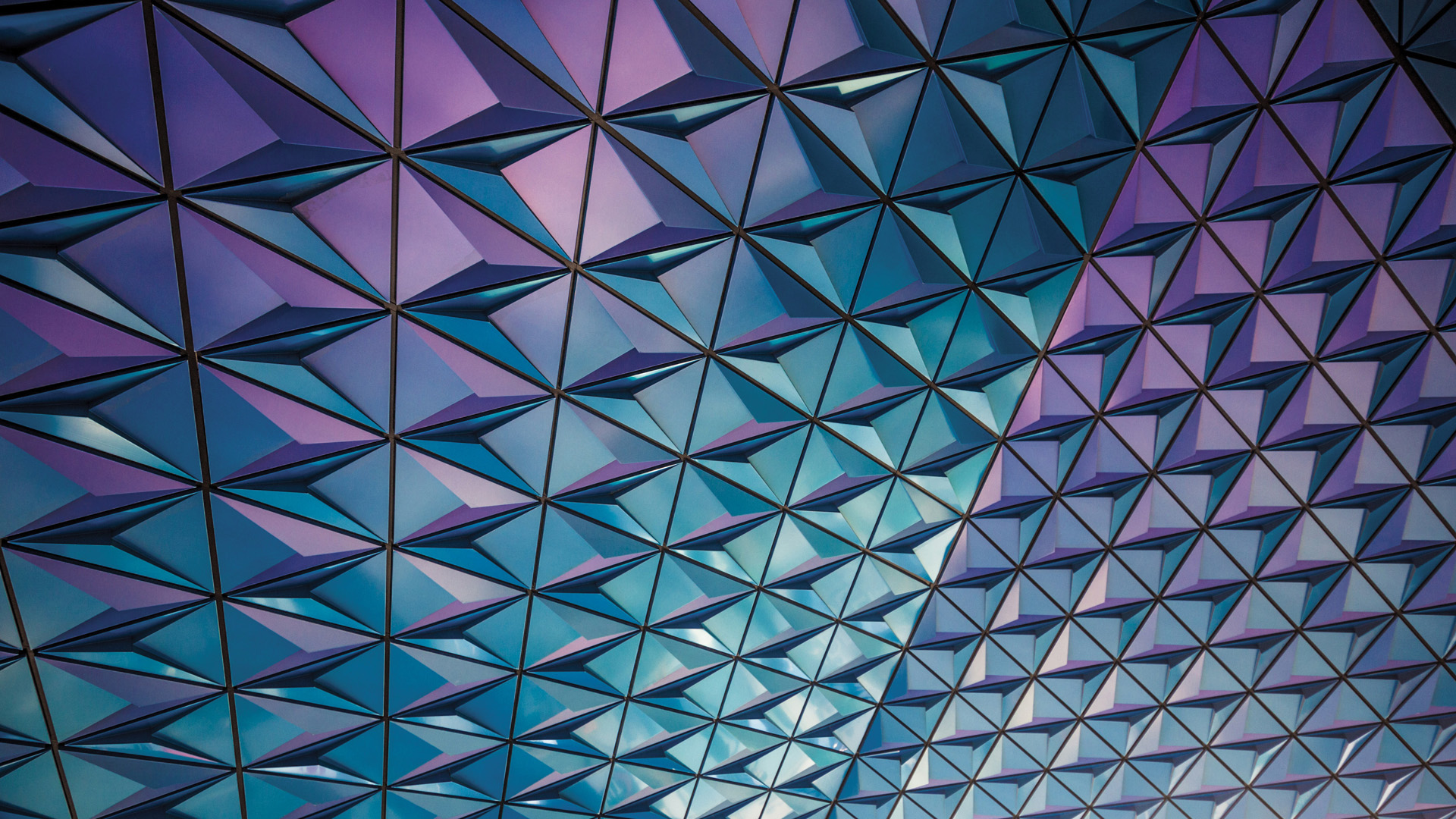
It's due to inaccurate and unrealistic assumptions
Incorrect assumptions or data can lead to inaccurate model results, and even incorrect decisions. These errors can lead to significant financial loss and poor decision-making by an organization. They also damage a company’s reputation. Incorrect modeling can have an impact on different industries. A wrong model might overestimate the chance of a terrorist attack against a plane or make fraudulent credit card transactions. Bad data and programming errors can lead to model errors.
Failure to follow a model’s guidelines can cause financial loss, regulatory penalty, and reputational damages. By enforcing governance and monitoring models, you can reduce the risk of model failure. However, model developers bear the responsibility for identifying model failures and assessing them.
It can be difficult to manage.
Predictive modeling is becoming more integral to business processes. However, there are growing risks. While the benefits are great, the potential consequences of a bad model are equally significant. Model Risk Management, as such, is vital to managing this risk. A good governance process and process will help organizations minimize the risk of these models, and can enable them to grow in any vertical.
Proper model risk management requires the development of a disciplined model development and implementation process. Model risk management should be in line with model governance policies. Every employee of the organization is responsible for understanding the risks associated model failure. Enterprise MLOps is a key part of model risk management.
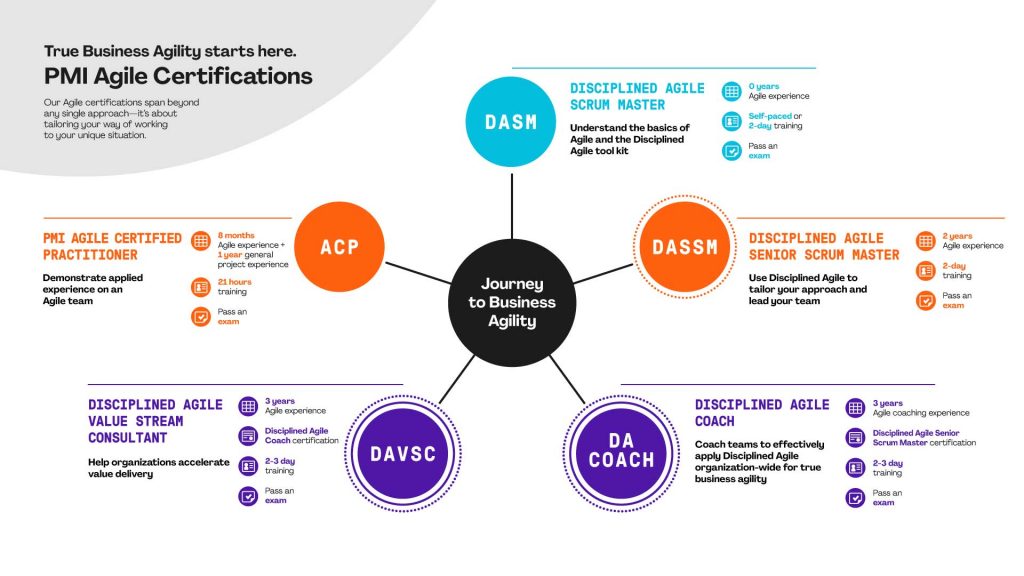
While there are a variety of ways to minimize model risk, it is difficult to completely eliminate it. It can be managed with other tools such as monitoring model performance, supplementing model results with analytical techniques, and other methods. An effective governance framework for managing model risk requires that it identifies the relevant risks and allocates funds appropriately. It should also include internal auditors who can examine models to verify they conform to acceptable policies.
FAQ
What are the five management steps?
The five stages of a business include planning, execution (monitoring), review, evaluation, and review.
Setting goals for the future requires planning. Planning involves defining your goals and how to get there.
Execution takes place when you actually implement the plans. They must be followed by all parties.
Monitoring is checking on progress towards achieving your objectives. Regular reviews of performance against budgets and targets should be part of this process.
Review events take place at each year's end. These reviews allow you to evaluate whether the year was successful. If not then, you can make changes to improve your performance next year.
After each year's review, evaluation occurs. It helps identify which aspects worked well and which didn't. It provides feedback about how people perform.
What is Six Sigma?
It's a method for quality improvement that focuses on customer service as well as continuous learning. The objective is to eliminate all defects through statistical methods.
Motorola's 1986 efforts to improve manufacturing process efficiency led to the creation of Six Sigma.
The idea spread quickly throughout the industry, and today, many organizations are using six sigma methods to improve product design, production, delivery, and customer service.
What are the main four functions of management
Management is responsible for organizing, managing, directing and controlling people, resources, and other activities. It also includes developing policies and procedures and setting goals.
Management assists an organization in achieving its goals by providing direction, coordination and control, leadership, motivation, supervision and training, as well as evaluation.
The following are the four core functions of management
Planning - Planning refers to deciding what is needed.
Organizing - Organization involves deciding what should be done.
Directing - This refers to getting people follow instructions.
Controlling: Controlling refers to making sure that people do what they are supposed to.
What does Six Sigma mean?
Six Sigma employs statistical analysis to identify problems, measure them and analyze root causes. Six Sigma also uses experience to correct problems.
The first step is identifying the problem.
The next step is to collect data and analyze it in order to identify trends or patterns.
The problem can then be fixed by taking corrective measures.
Finally, data is reanalyzed to determine whether the problem has been eliminated.
This cycle continues until there is a solution.
What are the steps that management takes to reach a decision?
Managers face complex and multifaceted decision-making challenges. It includes many factors such as analysis, strategy planning, implementation and measurement. Evaluation, feedback and feedback are just some of the other factors.
When managing people, the most important thing to remember is that they are just human beings like you and make mistakes. There is always room to improve, especially if your first priority is to yourself.
In this video, we explain what the decision-making process looks like in Management. We will explain the importance of different types decisions and how every manager can make them. Here are some topics you'll be learning about:
Statistics
- Hire the top business lawyers and save up to 60% on legal fees (upcounsel.com)
- The average salary for financial advisors in 2021 is around $60,000 per year, with the top 10% of the profession making more than $111,000 per year. (wgu.edu)
- UpCounsel accepts only the top 5 percent of lawyers on its site. (upcounsel.com)
- Your choice in Step 5 may very likely be the same or similar to the alternative you placed at the top of your list at the end of Step 4. (umassd.edu)
- 100% of the courses are offered online, and no campus visits are required — a big time-saver for you. (online.uc.edu)
External Links
How To
What is Lean Manufacturing?
Lean Manufacturing methods are used to reduce waste through structured processes. These processes were created by Toyota Motor Corporation, Japan in the 1980s. The main goal was to produce products at lower costs while maintaining quality. Lean manufacturing seeks to eliminate unnecessary steps and activities in the production process. It is made up of five elements: continuous improvement, continuous improvement, just in-time, continuous change, and 5S. Pull systems involve producing only what the customer wants without any extra work. Continuous improvement involves constantly improving upon existing processes. Just-in-time is when components and other materials are delivered at their destination in a timely manner. Kaizen is continuous improvement. This can be achieved by making small, incremental changes every day. Finally, 5S stands for sort, set in order, shine, standardize, and sustain. These five elements are used together to ensure the best possible results.
Lean Production System
Six key concepts underlie the lean production system.
-
Flow - The focus is on moving information and material as close as possible to customers.
-
Value stream mapping: This is a way to break down each stage into separate tasks and create a flowchart for the entire process.
-
Five S’s - Sorted, In Order. Shine. Standardize. And Sustain.
-
Kanban – visual signals like colored tape, stickers or other visual cues are used to keep track inventory.
-
Theory of constraints: Identify bottlenecks and use lean tools such as kanban boards to eliminate them.
-
Just-in-time delivery - Deliver components and materials right to your point of use.
-
Continuous improvement: Make incremental improvements to the process instead of overhauling it completely.