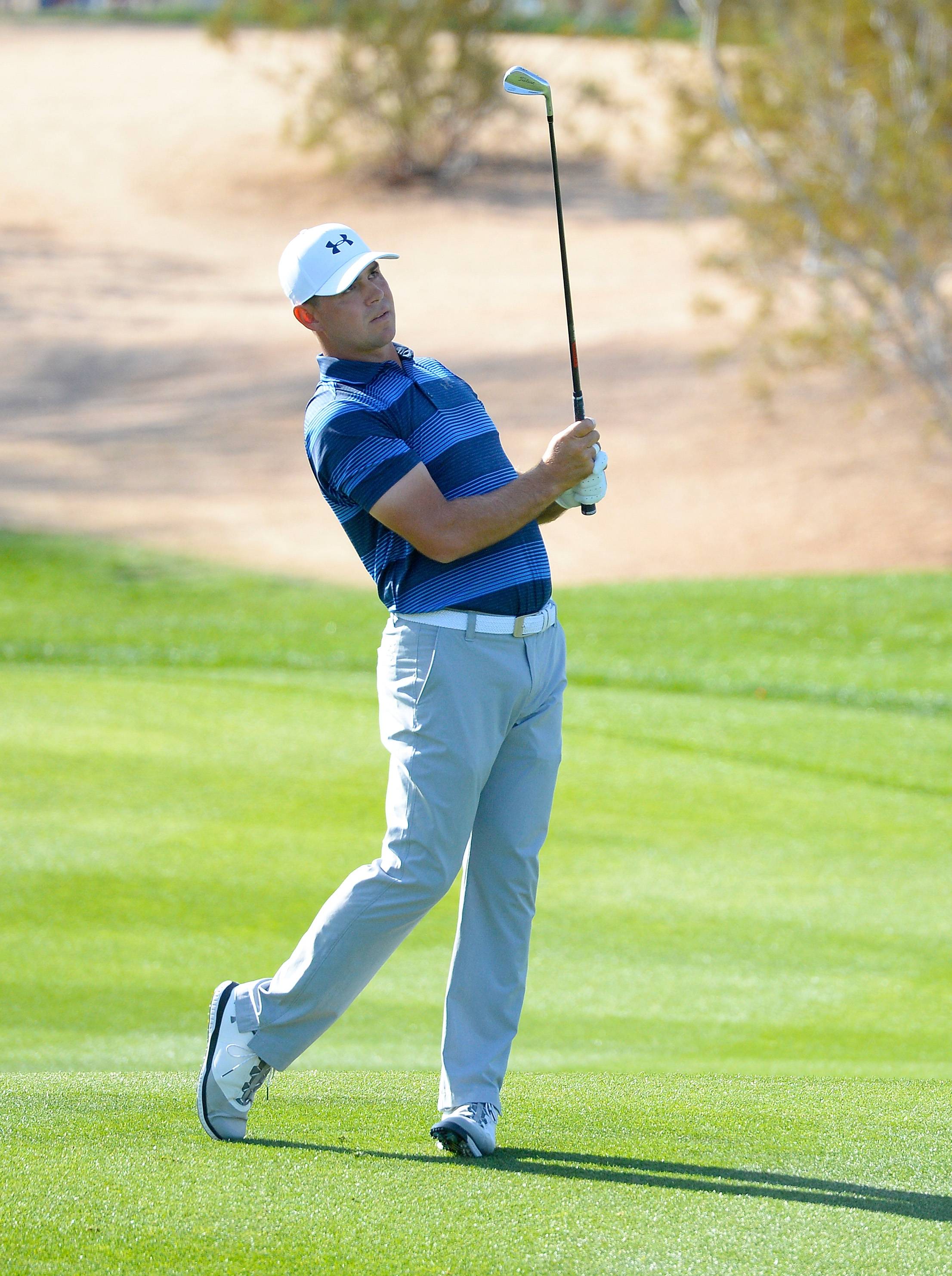
The hierarchy of control is an effective way to protect workers from hazards. In practice, it is used in many industries and is widely recognized by many safety organizations. This system is widely adopted and adopted by industry managers. However, this system can be modified in certain ways. To learn more, please check out our guide to the NFPA 70E hazard classification system and the ARECC variation. You will be able to apply the hierarchy more effectively in your workplace once you have this information.
NFPA 70E
NFPA70E is a set if standards that ensure electrical safety at work. The new 2018 edition has a new section called Annex Q that describes human performance and human error and their potential negative consequences. This section includes a hierarchy that prioritizes the elimination and prevention of hazards. For electrical hazards, the first step is to eliminate the hazard or source of energy. Personal protective equipment should only be used as a last resort.
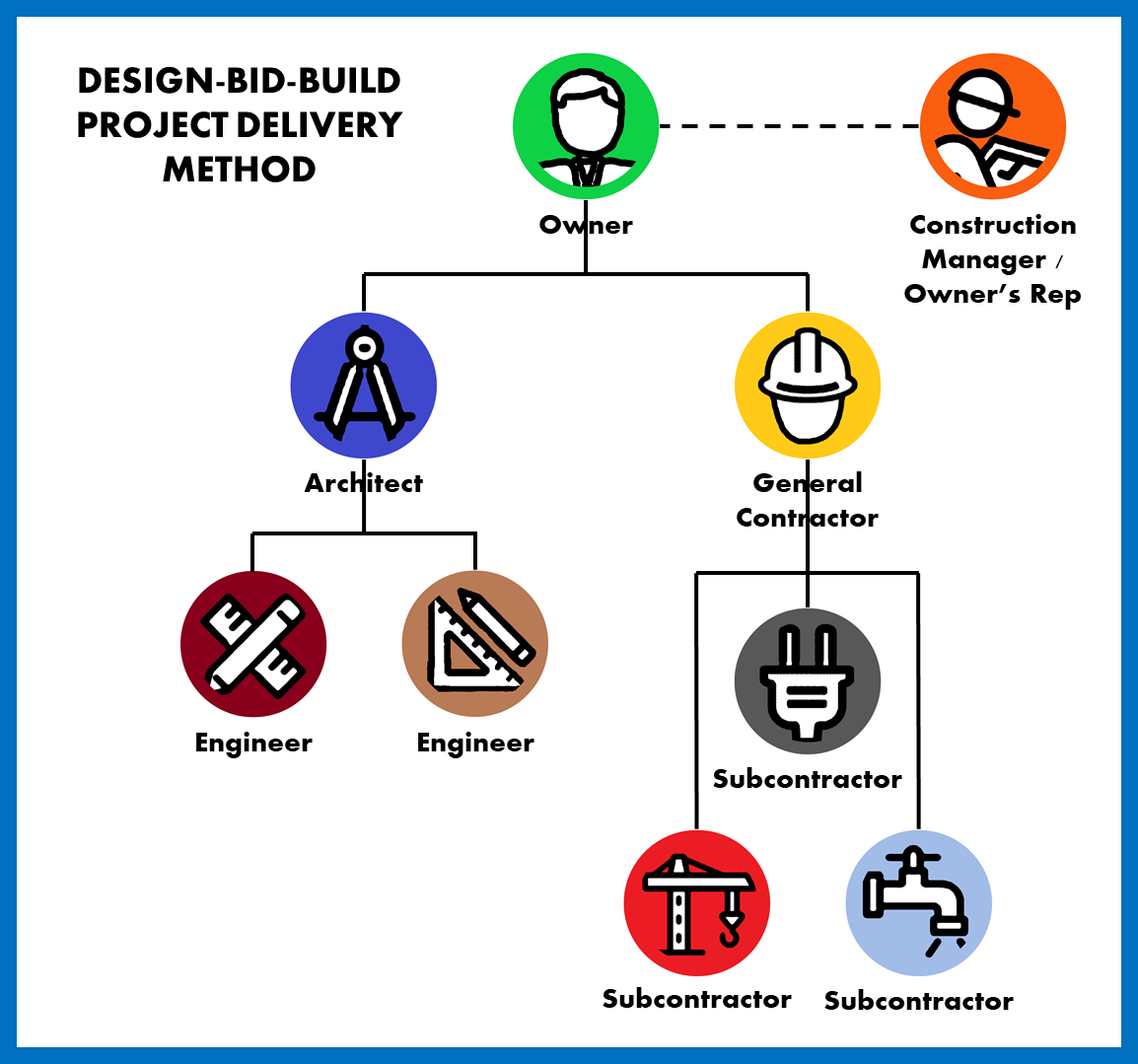
The next step is to determine how much exposure there is to hazards, and to identify the best engineering controls to reduce its severity. Although engineering controls can reduce exposure to hazardous substances but cannot eliminate the risk entirely, they can help minimize the risk. The hierarchy is designed to minimize exposure to hazards and reduce their severity. A common example is an engineering control, such as a fog machine or ventilation system, or a fire alarm.
Appendices can also be found in the NFPA70E standard. These documents provide information about specific procedures and practices and guidance on how to follow them. Appendices contain sample forms, PPE guidance and design requirements as well as risk assessment guidelines. The annexes, like the main text are intended to give guidance on how to implement this standard. In certain cases, they might provide useful information to help in the safety of a building and/or workplace.
ARECC variation
The ARECC Variation in the Hierarchy of Control is a method of reducing the exposure to a given hazard. The system was originally used in the United States and Canada. However, it has been modified in other countries. Some countries prefer isolation over engineering controls, while other combine both. The ARECC variations include warnings and employee training. Important to understand that warnings can't eliminate all hazards from a workplace.
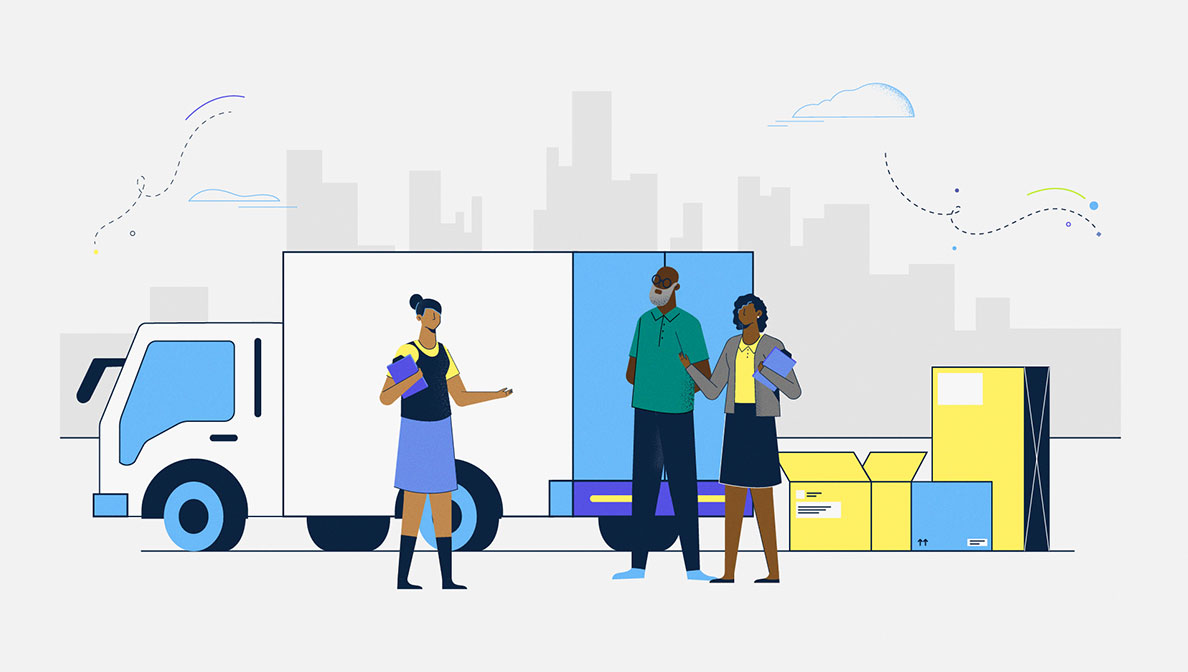
The ARECC hierarchy of controls is a framework for occupational safety and health. It helps to identify feasible solutions and ranks them according their effectiveness. The hierarchy contains five categories of controls: engineering controls and administrative controls. Each category is unique and important in a particular context. Some of the controls that are included in the ARECC hierarchy are more effective than others.
FAQ
Why is project management important for companies?
To ensure projects run smoothly and meet deadlines, project management techniques are employed.
This is due to the fact that most businesses rely heavily upon project work in order to produce goods, and services.
These projects require companies to be efficient and effective managers.
Companies can lose time, money, and reputation if they don't have a good project management system.
What are your main management skills
Managerial skills are crucial for every business owner, regardless of whether they run a small store in their locality or a large corporation. They include the ability to manage people, finances, resources, time, and space, as well as other factors.
These skills are necessary for setting goals and objectives as well as planning strategies, leading groups, motivating employees and solving problems.
As you can see, there are many managerial responsibilities!
What is the role of a manager in a company?
Each industry has a different role for a manager.
A manager is generally responsible for overseeing the day to day operations of a company.
He/she makes sure that the company meets its financial obligations, and that it produces goods or services that customers desire.
He/she is responsible for ensuring that employees comply with all regulations and follow quality standards.
He/she plans and oversees marketing campaigns.
What are the steps that management takes to reach a decision?
The decision-making process for managers is complex and multifaceted. It involves many elements, including analysis, strategy. planning. implementation. measurement. evaluation. feedback.
Remember that people are humans just like you, and will make mistakes. This is the key to managing them. You can always improve your performance, provided you are willing to make the effort.
We explain in this video how the Management decision-making process works. We will discuss the various types of decisions, and why they are so important. Every manager should be able to make them. Here are some topics you'll be learning about:
How do you manage employees effectively?
The key to effective management of employees is ensuring their happiness and productivity.
It means setting clear expectations for them and keeping an eye on their performance.
To do this successfully, managers need to set clear goals for themselves and for their teams.
They should communicate clearly with employees. And they need to ensure that they reward good performance and discipline poor performers.
They also need to keep records of their team's activities. These include:
-
What did we accomplish?
-
How much work was put in?
-
Who did it?
-
When it was done?
-
Why was it done?
This information can help you monitor your performance and to evaluate your results.
What is Six Sigma?
It's an approach to quality improvement that emphasizes customer service and continuous learning. The objective is to eliminate all defects through statistical methods.
Motorola developed Six Sigma in 1986 to help improve its manufacturing processes.
This idea quickly spread throughout the industry. Today, many organizations use six sigma methods for product design, production and delivery.
Statistics
- Our program is 100% engineered for your success. (online.uc.edu)
- The profession is expected to grow 7% by 2028, a bit faster than the national average. (wgu.edu)
- This field is expected to grow about 7% by 2028, a bit faster than the national average for job growth. (wgu.edu)
- Your choice in Step 5 may very likely be the same or similar to the alternative you placed at the top of your list at the end of Step 4. (umassd.edu)
- The BLS says that financial services jobs like banking are expected to grow 4% by 2030, about as fast as the national average. (wgu.edu)
External Links
How To
How can Lean Manufacturing be done?
Lean Manufacturing is a method to reduce waste and increase efficiency using structured methods. They were developed by Toyota Motor Corporation in Japan during the 1980s. The goal was to produce quality products at lower cost. Lean manufacturing focuses on eliminating unnecessary steps and activities from the production process. It is composed of five fundamental elements: continuous improvement; pull systems, continuous improvements, just-in–time, kaizen, continuous change, and 5S. Pull systems allow customers to get exactly what they want without having to do extra work. Continuous improvement involves constantly improving upon existing processes. Just-in–time refers when components or materials are delivered immediately to their intended destination. Kaizen refers to continuous improvement. It is achieved through small changes that are made continuously. Last but not least, 5S is for sort. These five elements can be combined to achieve the best possible results.
Lean Production System
Six key concepts make up the lean manufacturing system.
-
Flow: The goal is to move material and information as close as possible from customers.
-
Value stream mapping- This allows you to break down each step of a process and create a flowchart detailing the entire process.
-
Five S’s - Sorted, In Order. Shine. Standardize. And Sustain.
-
Kanban: Use visual signals such stickers, colored tape, or any other visual cues, to keep track your inventory.
-
Theory of constraints: Identify bottlenecks and use lean tools such as kanban boards to eliminate them.
-
Just-in-time delivery - Deliver components and materials right to your point of use.
-
Continuous improvement - Make incremental improvements rather than overhauling the entire process.