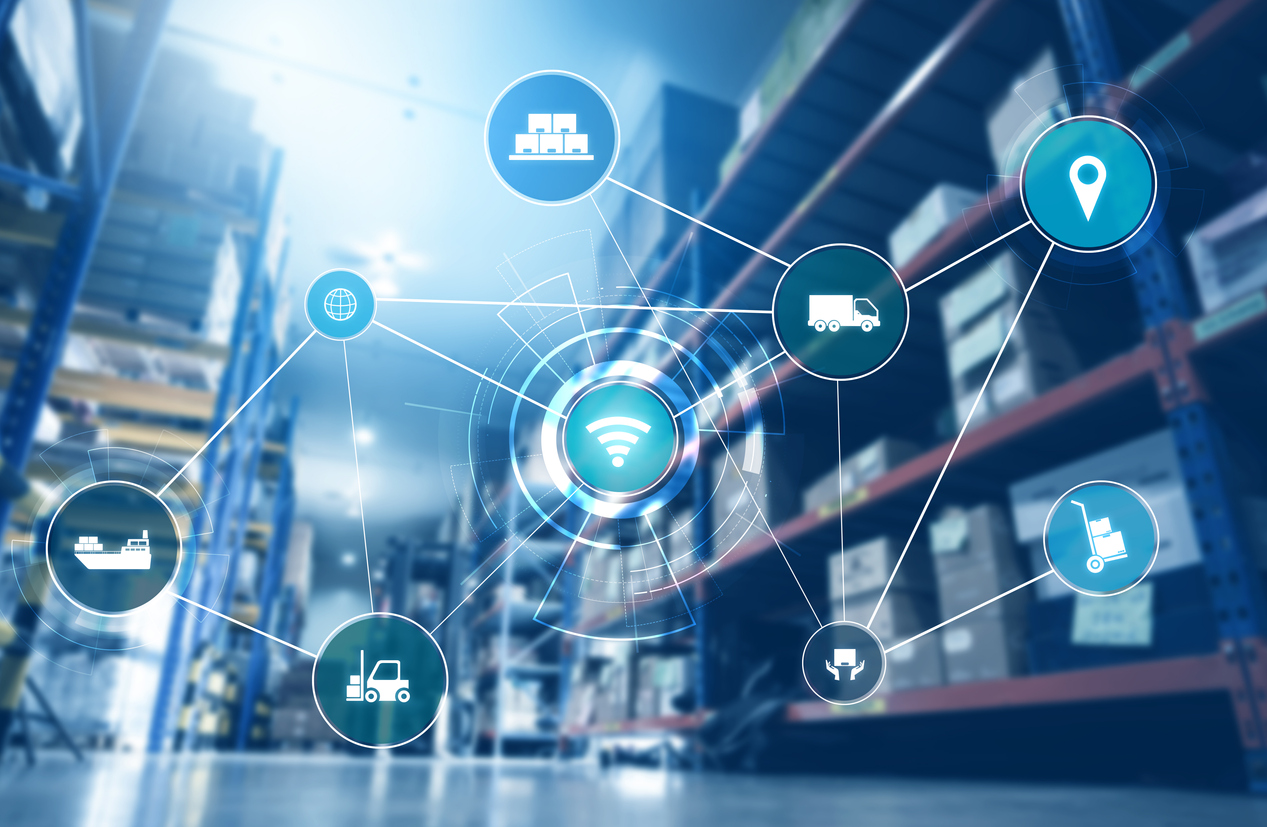
If you're interested in a career in construction management, you've come to the right place. You can read on to learn about the requirements and salary range, as well as what this job entails. Learn how to prepare for a job interview. Are you thinking of applying for a job as a construction manager? The first step is to choose what type construction project you want.
Job description
A job description in construction management should clearly define the responsibilities and duties. They are responsible for managing construction projects and working with architects, engineers, and other professionals to complete the project on time and within budget. Some managers supervise multiple projects at once, ensuring that all aspects of the project are completed in a timely manner. Ultimately, their job will be to maximize the overall value of a project.
Key details for a successful job as a construction manager should include work hours, locations, and benefits. Many potential managers are open-minded to working remotely and having travel opportunities. Highlight any advantages that make your role as construction manager unique. Last but not least, job descriptions that are compelling should end with a call-to-action, encouraging applicants to apply. They should be concise and clearly communicate the unique advantages and requirements of the job.
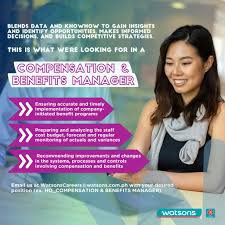
Education required
If you are interested in a career of construction managers, you might have wondered what education you would need. Construction management is a high-level service that uses specialized project management techniques to coordinate the design, planning, and construction phases of a project. This field requires you to work with a team that includes professionals who will ensure each step is done correctly and to client's satisfaction.
There are many entry points into the field of construction management, but a bachelor's in a related field is required for most positions. Because they provide a thorough understanding of the design process, undergraduate degrees in engineering or architecture are extremely helpful. An online bachelor's degree program in construction management from LSU Online is one option. This program will prepare for entry-level and further education in the field. The curriculum will cover design, project management, methods and materials as well as cost estimation. It also covers building codes and standards. The certification exam will also cover management and safety aspects.
Career outlook
The career prospects for construction managers are excellent as the economy continues its improvement. According to Bureau of Labor Statistics, the number of jobs for construction management professionals is expected to increase by 8 per cent over the next ten years. The increase in construction management jobs will be due to a variety of factors including the growth of the population, new sustainability campaigns, and business growth. In addition, the construction industry will continue to be a crucial part of the economy for the foreseeable future. Norwich University, one of the few online colleges offering this degree, offers a Master's program to prepare you for this exciting field.
Construction managers can expect a positive outlook on their job prospects due to the increase in construction activity. The Bureau of Labor Statistics estimates a ten percent increase in jobs between 2016 and 2026, which is enough to fill a large number of open positions. High retirement rates mean that construction managers may have more options than ever. A growing number of building technologies require more supervision. This is an ideal job for individuals with advanced education and skills.
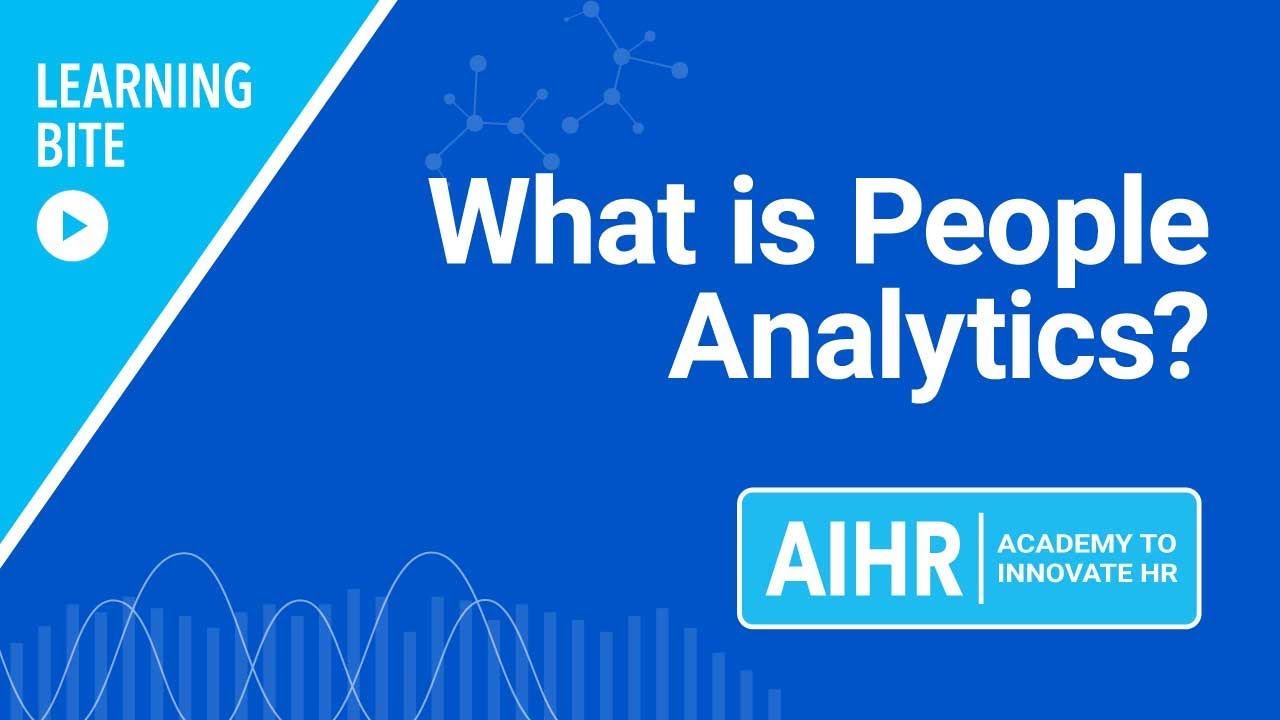
Salary
A description of a job in construction management describes the technical and professional aspects. They are responsible for the design and supervision of construction projects. They have a deep understanding of these areas. Their salary will vary depending on their education and experience. These tips can help you simplify your job search. Find out about the salaries and outlook for professionals in construction management.
Construction management salaries are largely based on experience and education. The average salary for construction managers was $74,950 in July 2017. Experience is a plus, as you might even be able find work right away. The field has good growth prospects as construction in the corporate and industrial sectors is on the rise. Although home building has slow down, it is expected to pick up again. It cannot be outsourced so it is fairly secure.
FAQ
What's the difference between a program and a project?
A project is temporary, while a program lasts forever.
A project usually has a specific goal and deadline.
This is often done by a group of people who report to one another.
A program often has a set goals and objectives.
It is often done by one person.
How do you define Six Sigma?
Six sigma is a common concept for people who have worked in statistics or operations research. Anybody involved in any aspect or business can benefit.
This requires a lot of dedication, so only people with great leadership skills can make the effort to implement it.
What are the 4 main functions of management?
Management is responsible to plan, organize, direct, and control people and resources. It includes the development of policies and procedures as well as setting goals.
Management aids an organization in reaching its goals by providing direction and coordination, control, leadership motivation, supervision, training, evaluation, and leadership.
These are the four major functions of management:
Planning – Planning involves deciding what needs to happen.
Organizing: Organizing refers to deciding how things should work.
Directing – This means to get people to follow directions.
Controlling – Controlling is the process of ensuring that tasks are completed according to plan.
What is a fundamental management tool for decision-making?
The decision matrix is a powerful tool that managers can use to help them make decisions. It allows them to think through all possible options.
A decision matrix is a way to organize alternatives into rows and columns. This allows you to easily see how each choice affects others.
We have four options in this example. They are represented by the boxes to the left of the matrix. Each box represents one option. The top row represents the current state of affairs, and the bottom row is indicative of what would happen in the event that nothing were done.
The effect of selecting Option 1 is shown in the middle column. In this case, it would mean increasing sales from $2 million to $3 million.
These are the results of selecting Options 2 or 3. These are positive changes - they increase sales by $1 million and $500 thousand respectively. However, these also involve negative consequences. Option 2 can increase costs by $100 million, while Option 3 can reduce profits by $200,000.
Finally, the last column shows the results of choosing Option 4. This involves decreasing sales by $1 million.
The best thing about a decision matrix is the fact that you don't have to remember which numbers go with what. It's easy to see the cells and instantly know if any one of them is better than another.
This is because the matrix has already taken care of the hard work for you. It's as easy as comparing numbers in the appropriate cells.
Here's an example showing how you might use a Decision Matrix in your business.
It is up to you to decide whether to spend more money on advertising. By doing so, you can increase your revenue by $5 000 per month. You will still have to pay $10000 per month in additional expenses.
If you look at the cell that says "Advertising", you can see the number $15,000. Advertising is worth more than its cost.
How can a manager improve his/her managerial skills?
Good management skills are essential for success.
Managers must constantly monitor the performance of their subordinates.
If you notice your subordinate isn't performing up to par, you must take action quickly.
You should be able to identify what needs improvement and how to improve things.
Statistics
- UpCounsel accepts only the top 5 percent of lawyers on its site. (upcounsel.com)
- The profession is expected to grow 7% by 2028, a bit faster than the national average. (wgu.edu)
- Hire the top business lawyers and save up to 60% on legal fees (upcounsel.com)
- This field is expected to grow about 7% by 2028, a bit faster than the national average for job growth. (wgu.edu)
- 100% of the courses are offered online, and no campus visits are required — a big time-saver for you. (online.uc.edu)
External Links
How To
How can Lean Manufacturing be done?
Lean Manufacturing uses structured methods to reduce waste, increase efficiency and reduce waste. They were developed in Japan by Toyota Motor Corporation (in the 1980s). It was designed to produce high-quality products at lower prices while maintaining their quality. Lean manufacturing seeks to eliminate unnecessary steps and activities in the production process. It has five components: continuous improvement and pull systems; just-in time; continuous change; and kaizen (continuous innovation). The production of only what the customer needs without extra work is called pull systems. Continuous improvement is the continuous improvement of existing processes. Just-in-time is when components and other materials are delivered at their destination in a timely manner. Kaizen means continuous improvement. Kaizen involves making small changes and improving continuously. Last but not least, 5S is for sort. These five elements can be combined to achieve the best possible results.
Lean Production System
Six key concepts underlie the lean production system.
-
Flow - The focus is on moving information and material as close as possible to customers.
-
Value stream mapping is the ability to divide a process into smaller tasks, and then create a flowchart that shows the entire process.
-
Five S's - Sort, Set In Order, Shine, Standardize, and Sustain;
-
Kanban: Use visual signals such stickers, colored tape, or any other visual cues, to keep track your inventory.
-
Theory of constraints - identify bottlenecks in the process and eliminate them using lean tools like kanban boards;
-
Just-in time - Get components and materials delivered right at the point of usage;
-
Continuous improvement - incremental improvements are made to the process, not a complete overhaul.