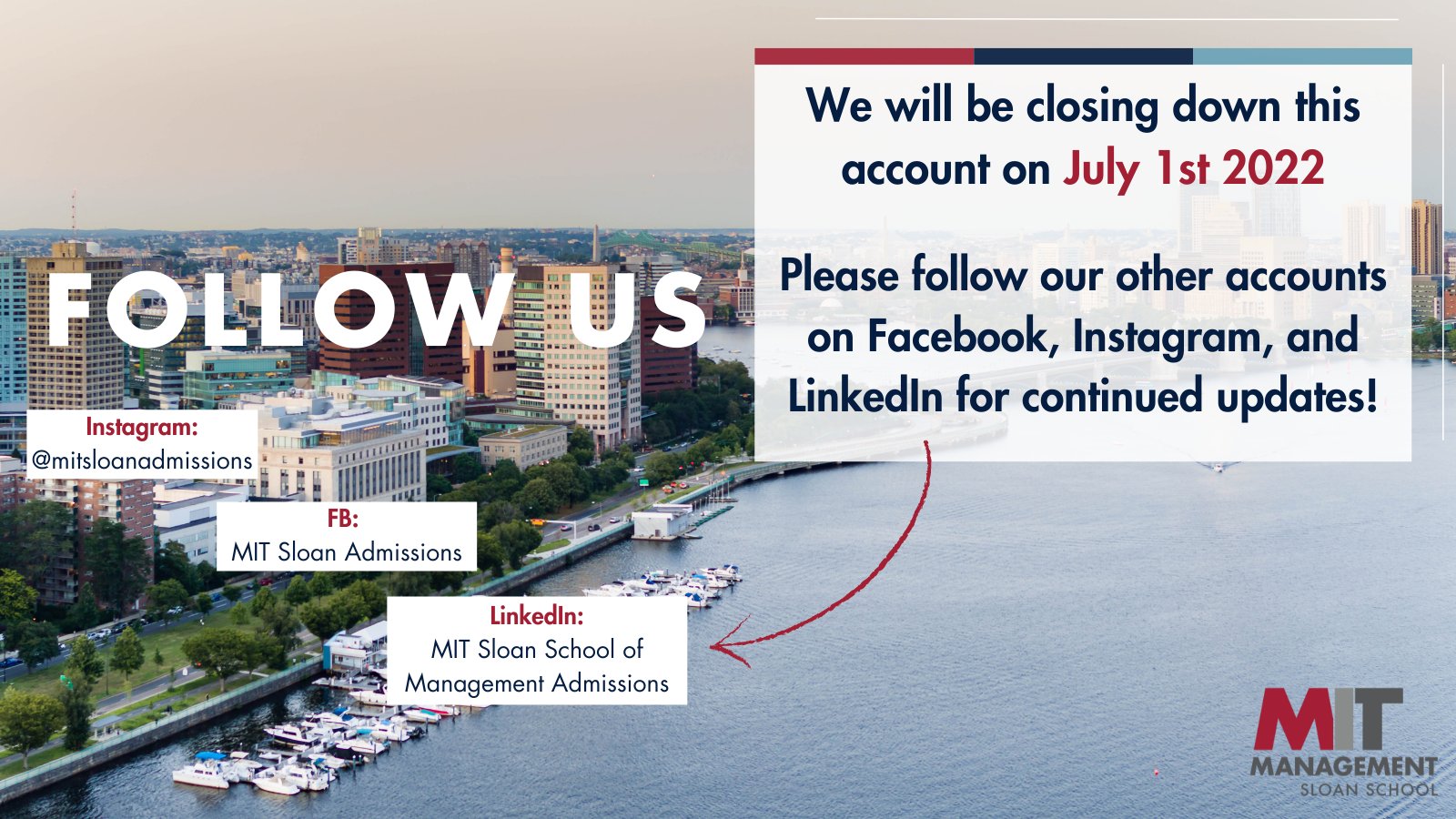
A risk register is a document that acts as a repository for all of your company's risks. The document can include additional information about each potential risk. This document will help you to identify your risks and track them. It will also keep your team, clients, and investors informed about any changes in the company that could impact their business.
Description
A risk register is an important tool for managing the risks associated to your project. It will help you determine which risks are high-priority and which are lower. To indicate the risk priority, you can use a color-coded system. You can also add a field for risk ownership to identify the department responsible for each risk. Status options are also available to provide information on risks.
A risk register contains both the qualitative and quantitative results of a risk analysis, along with a plan to respond to it. It lists the identified risks, their potential impact on the objectives, the proposed responses, as well as the current status. Your project management plan should include a risk register.
Purpose
A risk register helps to keep track and manage known risks that could affect businesses. It may be used for projects and business units as well as the entire organization. Whether the register is used for good or ill depends on the information collected. The information collected, along with the software platform used to manage the register, can all impact the value of a risk management registry.
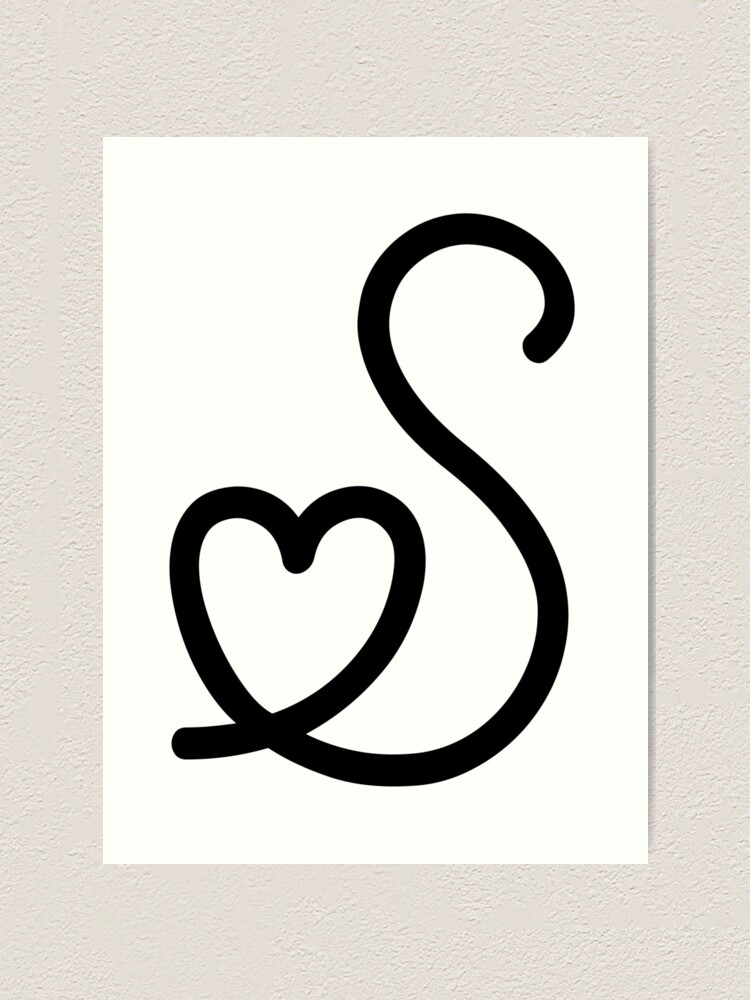
A purpose-built risk management software makes it simple to document risks, visualize and communicate with leadership teams. For example, Hyperproof's secure and intuitive risk register helps you document risks, link them to controls, and measure the risk's residual impact.
Contents
A risk register is an important tool for managing risks in a business. It is a document listing all known risks and key information about them on a single page. Each risk has a rating. The ratings are categorized according to subcategories or categories. There may also be residual risks.
Each risk should be identified and given detailed instructions. Even a minor risk may become a major problem later. It's important for project managers to know that not all risk have the same consequences. They need to prioritize which risks are to be prioritized and which risks should be ignored. Risks can generally be classified into three categories: high, medium, low, or both.
Format
For many reasons, a risk register can be useful. This allows you to track potential hazards and problems, and how they could affect your business. To help avoid future risks, a risk registry can be created. You can create a list of potential hazards if your business is susceptible to natural disasters.
Risk registers can be simple lists or complex spreadsheets. They should provide details on each risk, as well the severity and who is responsible.
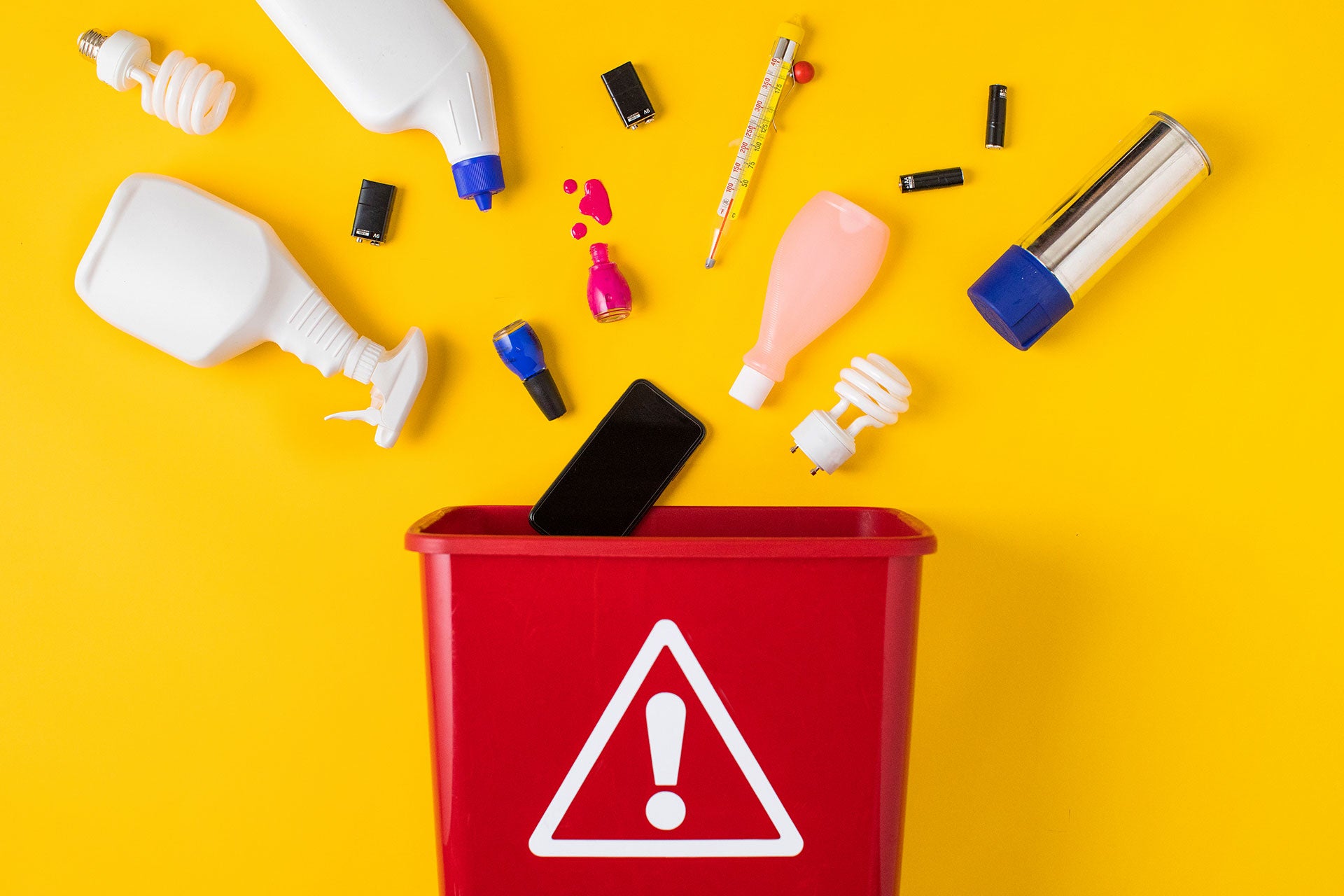
Review
You are responsible for reviewing the risks registry regularly if the business is responsible for assessing its risks. The risk register should be updated at least once a month. This is because it serves as a history log, and you can use it to evaluate the risks and identify potential issues. It is especially useful when you are looking at the feasibility of a particular project.
Risk management must be a continuous process as the risks evolve over time. Regular risk assessments are necessary to ensure that the risks are being properly managed. Risk reviews can also be used to communicate future risks to stakeholders, which helps manage expectations and secure engagement.
FAQ
What are the five management methods?
Planning, execution, monitoring and review are the five stages of any business.
Planning involves setting goals for the future. This includes setting goals for the future and defining what you want.
Execution happens when you actually do the plan. Everyone involved must follow them.
Monitoring is a way to track progress towards your objectives. Regular reviews should be done of your performance against targets or budgets.
Every year, there are reviews. These reviews allow you to evaluate whether the year was successful. If not there are changes that can be made to improve the performance next year.
After the annual review, evaluation takes place. It helps to identify what went well and what didn’t. It also provides feedback on how well people performed.
How do you effectively manage employees?
Effectively managing employees requires that you ensure their happiness and productivity.
This includes setting clear expectations for their behavior and tracking their performance.
To do this successfully, managers need to set clear goals for themselves and for their teams.
They should communicate clearly to staff members. And they need to ensure that they reward good performance and discipline poor performers.
They should also keep records of all activities within their team. These include:
-
What was the result?
-
What was the work involved?
-
Who did it and why?
-
It was done!
-
Why was it done?
This information is useful for monitoring performance and evaluating the results.
How do we build a culture that is successful in our company?
Successful company culture is one where people feel valued and respected.
It's founded on three principal principles:
-
Everybody can contribute something valuable
-
People are treated fairly
-
It is possible to have mutual respect between groups and individuals
These values reflect in how people behave. They will show consideration and courtesy to others.
They will listen respectfully to the opinions of others.
They will also encourage others to share their ideas and feelings.
Company culture also encourages open communication, collaboration, and cooperation.
People are free to speak out without fear of reprisal.
They understand that mistakes can be forgiven as long as they're dealt with honestly.
The company culture encourages honesty and integrity.
Everyone knows that they must always tell truth.
Everyone recognizes that rules and regulations are important to follow.
Everyone does not expect to receive special treatment.
What is a simple management tool that aids in decision-making and decision making?
A decision matrix is a simple but powerful tool for helping managers make decisions. They can think about all options and make informed decisions.
A decision matrix is a way to organize alternatives into rows and columns. This allows one to see how each alternative impacts other options.
The boxes on the left hand side of this matrix represent four possible choices. Each box represents a different option. The top row shows the status quo (the current situation), and the bottom row shows what would happen if nothing was done at all.
The middle column shows the effect of choosing Option 1. In this example, it would lead to an increase in sales of between $2 million and $3 million.
The next two columns show the effects of choosing Options 2 and 3. These positive changes can increase sales by $1 million or $500,000. These positive changes have their downsides. Option 2 can increase costs by $100 million, while Option 3 can reduce profits by $200,000.
The final column shows results of choosing Option 4. This results in a decrease of sales by $1,000,000
The best part of using a decision-matrix is that it doesn't require you to know which numbers belong where. Simply look at the cells to instantly determine if one choice is better than the other.
This is because the matrix has done all the hard work. It is as simple as comparing the numbers within the relevant cells.
Here's an example of how you might use a decision matrix in your business.
Advertising is a decision that you make. This will allow you to increase your revenue by $5000 per month. You'll also have additional expenses up to $10,000.
If you look at the cell that says "Advertising", you can see the number $15,000. Advertising is more valuable than its costs.
What is the main difference between Six Sigma Six Sigma TQM and Six Sigma Six Sigma?
The key difference between the two quality management tools is that while six-sigma focuses its efforts on eliminating defects, total quality management (TQM), focuses more on improving processes and reducing cost.
Six Sigma is a methodology for continuous improvement. This method emphasizes eliminating defects using statistical methods such p-charts, control charts, and Pareto analysis.
This method aims to reduce variation in product production. This is done by identifying root causes and rectifying them.
Total Quality Management involves monitoring and measuring every aspect of the organization. Training employees is also part of total quality management.
It is often used as a strategy to increase productivity.
How can a manager motivate employees?
Motivation refers to the desire to perform well.
Enjoyable activities can motivate you.
Another way to get motivated is to see yourself as a contributor to the success of the company.
For example, if you want to become a doctor, you'll probably find it more motivating to see patients than to study medicine books all day.
Motivation comes from within.
You may feel strongly that you are responsible to help others.
Perhaps you enjoy working hard.
If you don’t feel motivated, find out why.
Next, think of ways you can improve your motivation.
What is Kaizen?
Kaizen is a Japanese term meaning "continuous improvement." It is a philosophy that encourages employees to constantly look for ways to improve their work environment.
Kaizen is a belief that everyone should have the ability to do their job well.
Statistics
- Our program is 100% engineered for your success. (online.uc.edu)
- UpCounsel accepts only the top 5 percent of lawyers on its site. (upcounsel.com)
- The profession is expected to grow 7% by 2028, a bit faster than the national average. (wgu.edu)
- Hire the top business lawyers and save up to 60% on legal fees (upcounsel.com)
- The BLS says that financial services jobs like banking are expected to grow 4% by 2030, about as fast as the national average. (wgu.edu)
External Links
How To
How is Lean Manufacturing done?
Lean Manufacturing uses structured methods to reduce waste, increase efficiency and reduce waste. These processes were created by Toyota Motor Corporation, Japan in the 1980s. The goal was to produce quality products at lower cost. Lean manufacturing focuses on eliminating unnecessary steps and activities from the production process. It consists of five basic elements: pull systems, continuous improvement, just-in-time, kaizen (continuous change), and 5S. Pull systems involve producing only what the customer wants without any extra work. Continuous improvement is the continuous improvement of existing processes. Just-in time refers to components and materials being delivered right at the place they are needed. Kaizen refers to continuous improvement. It is achieved through small changes that are made continuously. The 5S acronym stands for sort in order, shine standardize and maintain. These five elements are used together to ensure the best possible results.
Lean Production System
Six key concepts are the basis of lean production:
-
Flow is about moving material and information as near as customers can.
-
Value stream mapping: This is a way to break down each stage into separate tasks and create a flowchart for the entire process.
-
Five S's - Sort, Set In Order, Shine, Standardize, and Sustain;
-
Kanban – visual signals like colored tape, stickers or other visual cues are used to keep track inventory.
-
Theory of constraints - identify bottlenecks during the process and eliminate them with lean tools like Kanban boards.
-
Just-in-time - deliver components and materials directly to the point of use;
-
Continuous improvement - make incremental improvements to the process rather than overhauling it all at once.