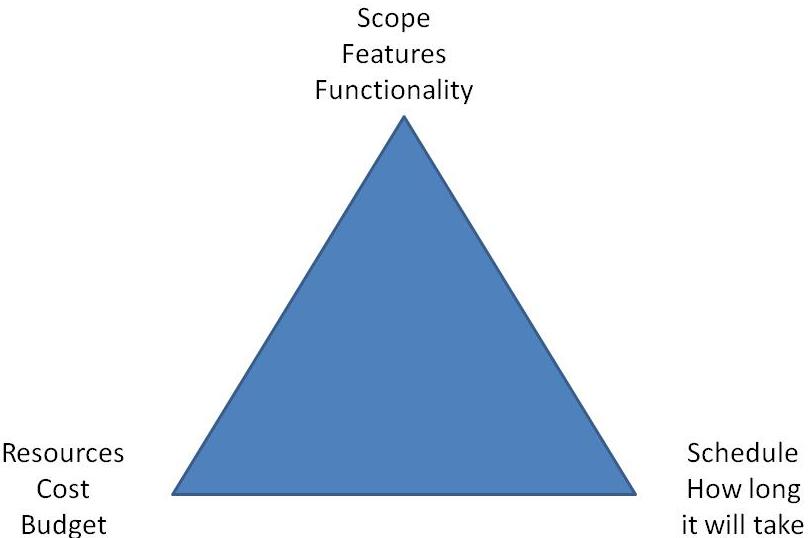
Recognizing client's strengths, and their weaknesses
A key step in management consulting is to determine the strengths and weaknesses of a client. Many clients provide mixed information or a distorted view about their problems, and the management consultant must filter this information to pinpoint specific challenges. A business may be tempted to assume that its past strategies will still work in a new marketplace, but it will likely face new challenges. This information must be assessed by the management consultant. They should then present their recommendations to clients in an easy-to-understand manner, based on the client's business needs.
Management consultants should not be seen as advocates for one management style. Their work should enhance the overall effectiveness and efficiency of the company. They must be able communicate with clients and other departments to address their concerns. The consultant should be able to link issues to the client’s larger goals, and future plans. A consulting process should lower barriers to improvement, encourage experimentation with better management methods, and stimulate the client's larger goals.
Efficiency in business processes
To keep your business competitive and profitable, it is essential to create efficiency in business processes. To maximize their product quality, profits, and resource utilization, businesses will need to constantly improve their processes as technology advances. A Process Efficiency Consultant is able to provide objective analysis of your business processes, and suggest ways to improve them. They can then develop solutions to bring about change.
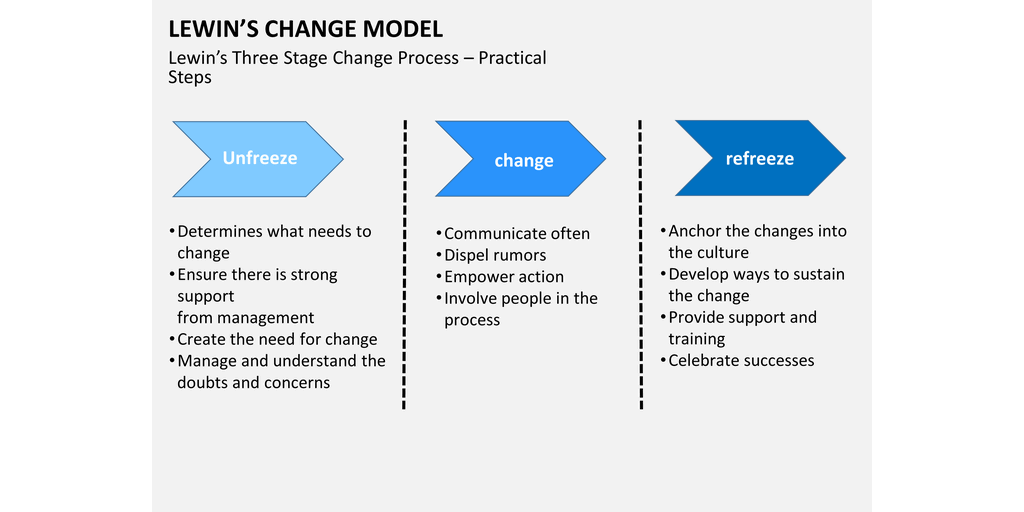
A business process is an organized sequence of activities that produces a product or service to satisfy a customer's need. Creating speedy, efficient processes is essential to achieve your business goals and delight customers. Inefficient processes cost money to maintain and decrease efficiency as your business grows. If left untreated, these problems can grow exponentially.
Many financial institutions have turned to business process consultants for a range of organizational needs. As the public perception of financial institutions changes, these companies will need to adopt secure strategies for growth, increase system resilience and improve regulatory compliance and management of risk and evolve client-facing technology.
Implementing the recommendations
Consultants are often hired by clients to help solve problems. However they are not responsible for implementing the recommendations. The recommendations of consulting are crucial to the reputation and credibility the firm. It is therefore crucial to follow the recommendations. Fortunately, there are a few steps that consulting firms can take to increase their chances of success.
First, be sure to include implementation in your contract. It is possible to request an extension. This extension may be of interest to the consulting client and can strengthen the relationship between them and the firm. It can also help the consultant ensure that recommendations are implemented, as it strengthens the consultant-client relationship.
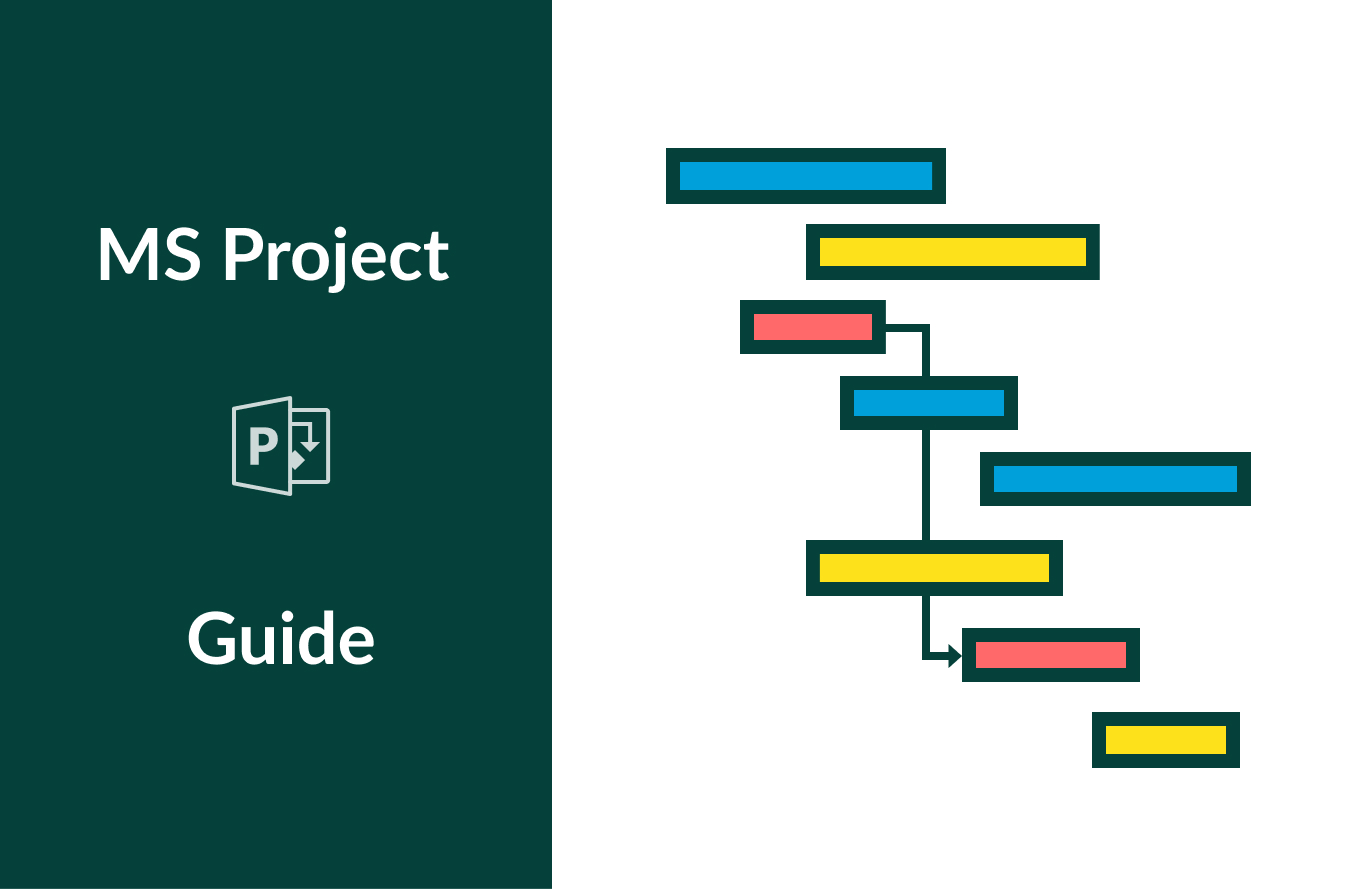
The purpose of consulting should be to remove any obstacles that might be hindering the organization's implementation of the recommendations. The consultant shouldn't be a crusader; they should be a practitioner who is consistent in his or her views. The consulting process should promote experimentation through more effective management styles.
FAQ
How can we create a successful company culture?
A positive company culture creates a sense of belonging and respect in its people.
It is based on three principles:
-
Everyone has something valuable to contribute
-
People are treated fairly
-
There is mutual respect between individuals and groups
These values are evident in the way that people act. They will treat others with respect and kindness.
They will be respectful of the opinions of other people.
They encourage others to express their feelings and ideas.
The company culture promotes collaboration and open communication.
People can freely express their opinions without fear or reprisal.
They understand that mistakes can be forgiven as long as they're dealt with honestly.
Finally, the company culture encourages honesty as well as integrity.
Everybody knows they have to tell the truth.
Everyone is aware that rules and regulations apply to them.
People don't expect special treatment or favors.
How do you manage your employees effectively?
The key to effective management of employees is ensuring their happiness and productivity.
This also involves setting clear expectations and monitoring their performance.
Managers need to establish clear goals for their team and for themselves.
They need to communicate clearly and openly with staff members. They also need to make sure that they discipline and reward the best performers.
They should also keep records of all activities within their team. These include:
-
What was achieved?
-
What was the work involved?
-
Who did it?
-
What was the moment it was completed?
-
Why it was done?
This information is useful for monitoring performance and evaluating the results.
What is TQM?
When manufacturing companies realized that price was not enough to compete, the industrial revolution brought about the quality movement. They needed to improve the quality and efficiency of their products if they were to be competitive.
Management developed Total Quality Management to address the need for improvement. It focused on all aspects of an organisation's performance. It involved continuous improvement, employee participation, and customer satisfaction.
What is Six Sigma?
It's a method for quality improvement that focuses on customer service as well as continuous learning. This is an approach to quality improvement that uses statistical techniques to eliminate defects.
Motorola developed Six Sigma in 1986 to help improve its manufacturing processes.
This idea quickly spread throughout the industry. Today, many organizations use six sigma methods for product design, production and delivery.
What are the steps in the decision-making process in management?
Managers have to make complex decisions. It involves many elements, including analysis, strategy. planning. implementation. measurement. evaluation. feedback.
The key thing to remember when managing people is that they are human beings just as you are and therefore make mistakes. You can always improve your performance, provided you are willing to make the effort.
This video will explain how decision-making works in Management. We will explain the importance of different types decisions and how every manager can make them. Here are some topics you'll be learning about:
Statistics
- Hire the top business lawyers and save up to 60% on legal fees (upcounsel.com)
- 100% of the courses are offered online, and no campus visits are required — a big time-saver for you. (online.uc.edu)
- Your choice in Step 5 may very likely be the same or similar to the alternative you placed at the top of your list at the end of Step 4. (umassd.edu)
- The BLS says that financial services jobs like banking are expected to grow 4% by 2030, about as fast as the national average. (wgu.edu)
- The average salary for financial advisors in 2021 is around $60,000 per year, with the top 10% of the profession making more than $111,000 per year. (wgu.edu)
External Links
How To
How do I do the Kaizen Method?
Kaizen means continuous improvement. This Japanese term refers to the Japanese philosophy of continuous improvement that emphasizes incremental improvements and constant improvement. It's where people work together in order to improve their processes constantly.
Kaizen is one method that Lean Manufacturing uses to its greatest advantage. Kaizen is a concept where employees in charge of the production line are required to spot problems during the manufacturing process before they become major issues. This increases the quality of products and reduces the cost.
The main idea behind kaizen is to make every worker aware of what happens around him/her. It is important to correct any problems immediately if they are discovered. So, if someone notices a problem while working, he/she should report it to his/her manager.
When doing kaizen, there are some principles we must follow. The end product is always our starting point and we work toward the beginning. If we want to improve our factory for example, we start by fixing the machines that make the final product. Then, we fix the machines that produce components and then the ones that produce raw materials. Then we fix the workers, who directly work with these machines.
This approach is called 'kaizen' because it focuses on improving everything steps by step. Once the factory is fixed, we return to the original site and work our way back until we get there.
Before you can implement kaizen into your business, it is necessary to learn how to measure its effectiveness. There are many ways you can determine if kaizen has been implemented well. One of these ways is to check the number of defects found on the finished products. Another method is to determine how much productivity has improved since the implementation of kaizen.
A good way to determine whether kaizen has been implemented is to ask why. You were trying to save money or obey the law? It was a way to save money or help you succeed.
Let's say you answered yes or all of these questions. Congratulations! Now you're ready for kaizen.