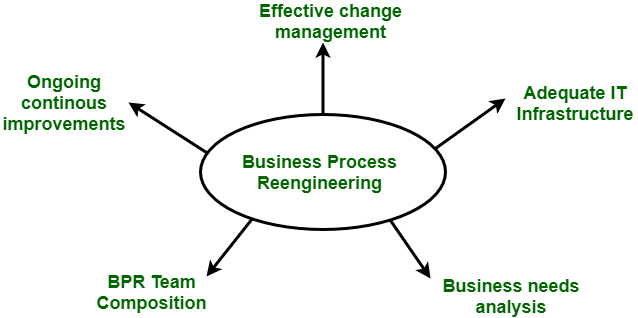
A key aspect of any clean-up is waste remediation. Safeguarding the environment and communities can be achieved by eliminating hazardous substances and other contaminants from contaminated locations. Whether the problem is urban, rural, or industrial, waste remediation can be a critical step. Read on to learn more about the process and costs of waste remediation projects.
Methods of waste remediation
The treatment of hazardous materials is part of waste remediation. Incineration is a method that burns solid waste at high temperatures in order to make energy for heating or electric. This process decreases waste volume, lowers transport costs and reduces greenhouse gas emissions. Gasification, which is a low-temperature method of obtaining energy without polluting the atmosphere, is another option.
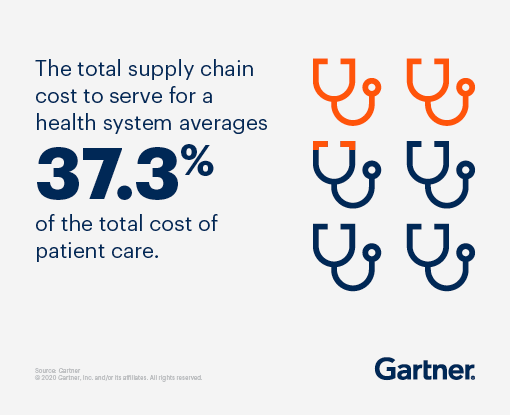
The demand for a more efficient way to dispose waste is increasing as the world population increases. Low-lying areas, such as in developing countries, are often covered with a thin layer containing garbage, and then treated with soil. After proper treatment, an area can be redeveloped into parkland and playgrounds.
Another popular method of waste remediation is the use of chemical disinfectants. Although this is most suitable for liquid waste, it can sometimes be used for solid waste. In determining the best chemical disinfectant for a specific type of waste, a number of factors need to be considered. These factors include the type and concentration of the disinfectant, as well as the contamination. Important is also the length of contact with waste.
Alternatives to RCRA's requirements for managing remediation waste
Although there have been many alternatives to RCRA’s requirements for waste management remediation, their implementation was often difficult, due in part to their legal and technical issues. The EPA has issued a new rule to allow projects to use modified RCRA permits in order to simplify the requirements. These modified versions can also be tailored to fit the specific needs of the facility. The EPA hopes that this will improve safety and cleanup procedures.
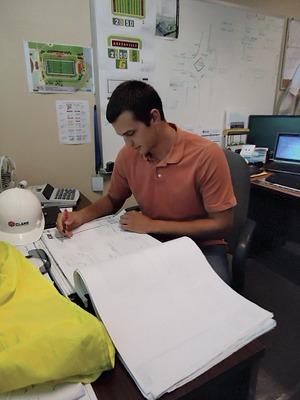
Alternatives to RCRA’s requirements on remediation waste management can be found for both on-site treatment or removal. The former allows for the placement of remediation waste in containers or tanks or is treated ex-situ or removed from the AOC.
FAQ
Six Sigma is so well-known.
Six Sigma is easy to use and can lead to significant improvements. Six Sigma also gives companies a framework for measuring improvement and helps them focus on what is most important.
What are the three basic management styles?
There are three types of management: participative, laissez faire, and authoritarian. Each style is unique and has its strengths as well as weaknesses. What style do you prefer? Why?
Autoritarian – The leader sets the direction for everyone and expects them to follow. This style works best in large organizations that are stable and well-organized.
Laissez-faire – The leader gives each individual the freedom to make decisions for themselves. This style is most effective when the organization's size and dynamics are small.
Participative – The leader listens and takes in ideas from all. This style is most effective in smaller organizations, where everyone feels valued.
What are the steps that management takes to reach a decision?
Managers face complex and multifaceted decision-making challenges. It involves many elements, including analysis, strategy. planning. implementation. measurement. evaluation. feedback.
When managing people, the most important thing to remember is that they are just human beings like you and make mistakes. As such, there is always room for improvement, especially if you're willing to put forth the effort to improve yourself first.
This video explains the process of decision-making in Management. We discuss the different types of decisions and why they are important, every manager should know how to navigate them. These topics are covered in this course:
What is Six Sigma?
Six Sigma uses statistical analysis for problems to be found, measured, analyzed root causes, corrected, and learned from.
The first step to solving the problem is to identify it.
Next, data is collected and analyzed to identify trends and patterns.
Then corrective actions are taken to solve the problem.
Finally, the data are reanalyzed in order to determine if it has been resolved.
This cycle continues until there is a solution.
What are some of the common mistakes made by managers?
Managers sometimes make their own job harder than necessary.
They may not assign enough responsibilities to staff members and provide them with inadequate support.
Managers often lack the communication skills necessary to motivate and guide their teams.
Managers sometimes set unrealistic expectations of their teams.
Some managers may try to solve every problem themselves instead of delegating responsibility to others.
What is TQM, exactly?
The industrial revolution saw the realization that prices alone were not sufficient to sustain manufacturing companies. This led to the birth of quality. If they wanted to stay competitive, they needed to improve their quality and efficiency.
Management realized the need to improve and created Total Quality Management, which focused on improving all aspects within an organization's performance. It involved continuous improvement, employee participation, and customer satisfaction.
What is a management tool to help with decision-making?
The decision matrix is a powerful tool that managers can use to help them make decisions. It allows them to think through all possible options.
A decision matrix allows you to represent alternatives as columns and rows. This allows one to see how each alternative impacts other options.
The boxes on the left hand side of this matrix represent four possible choices. Each box represents an alternative. The top row displays the current situation, and the bottom row shows what might happen if nothing is done.
The effect of selecting Option 1 is shown in the middle column. In this case, it would mean increasing sales from $2 million to $3 million.
The effects of options 2 and 3 are shown in the next columns. These are both positive changes that increase sales by $1million and $500,000. However, these also involve negative consequences. Option 2 increases costs by $100 thousand, while Option 3 decreases profits to $200 thousand.
The last column displays the results of selecting Option 4. This means that sales will decrease by $1 million.
A decision matrix has the advantage that you don’t have to remember where numbers belong. Simply look at the cells to instantly determine if one choice is better than the other.
This is because your matrix has already done the hard work. Simply compare the numbers within the cells.
Here is an example how you might use the decision matrix in your company.
You want to decide whether or not to invest more money into advertising. By doing so, you can increase your revenue by $5 000 per month. But, you will also incur additional expenses of $10 thousand per month.
The net result of advertising investment can be calculated by looking at the cell below that reads "Advertising." It is 15 thousand. Therefore, you should choose to invest in advertising since it is worth more than the cost involved.
Statistics
- Our program is 100% engineered for your success. (online.uc.edu)
- The profession is expected to grow 7% by 2028, a bit faster than the national average. (wgu.edu)
- As of 2020, personal bankers or tellers make an average of $32,620 per year, according to the BLS. (wgu.edu)
- UpCounsel accepts only the top 5 percent of lawyers on its site. (upcounsel.com)
- 100% of the courses are offered online, and no campus visits are required — a big time-saver for you. (online.uc.edu)
External Links
How To
How can Lean Manufacturing be done?
Lean Manufacturing uses structured methods to reduce waste, increase efficiency and reduce waste. They were created by Toyota Motor Corporation in Japan in the 1980s. The primary goal was to make products with lower costs and maintain high quality. Lean manufacturing eliminates unnecessary steps and activities from a production process. It has five components: continuous improvement and pull systems; just-in time; continuous change; and kaizen (continuous innovation). Pull systems involve producing only what the customer wants without any extra work. Continuous improvement is constantly improving upon existing processes. Just-in-time is when components and other materials are delivered at their destination in a timely manner. Kaizen refers to continuous improvement. It is achieved through small changes that are made continuously. Last but not least, 5S is for sort. These five elements work together to produce the best results.
Lean Production System
Six key concepts underlie the lean production system.
-
Flow: The goal is to move material and information as close as possible from customers.
-
Value stream mapping: This is a way to break down each stage into separate tasks and create a flowchart for the entire process.
-
Five S's – Sort, Put In Order Shine, Standardize and Sustain
-
Kanban is a visual system that uses visual cues like stickers, colored tape or stickers to keep track and monitor inventory.
-
Theory of constraints - identify bottlenecks in the process and eliminate them using lean tools like kanban boards;
-
Just-in time - Get components and materials delivered right at the point of usage;
-
Continuous improvement: Make incremental improvements to the process instead of overhauling it completely.