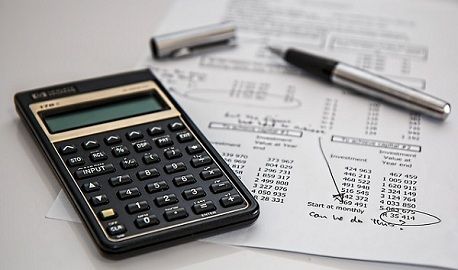
Ad hoc job means a job that is temporary. This type of project requires people with the right skills and the time to complete it. Project managers will often consult other department managers to determine the amount of people needed to complete the job. The project manager will then need to request the help of qualified individuals.
The management of ad hoc and emergency projects
If you have to deal with a lot of ad-hoc work, it is important that you establish a process for managing them. You can achieve this by having a project diary that contains details about tasks, due dates, and other information. This can help you remember the tasks and also keep track of other people's work, improving communication and management. It is also important to update the log whenever tasks change or new ones arise.
It is important to make sure everyone in a project team is clear about the expectations. This is especially important if you are working with multiple stakeholders. The project's objectives and scope must be understood by all members of the team. You can ask someone who is more experienced to help you determine the goals of your project.
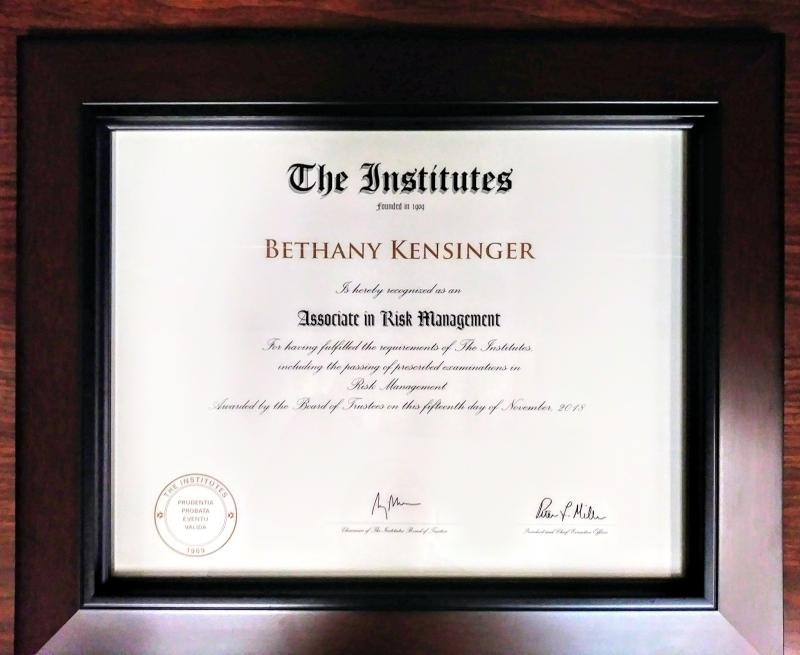
Ad hoc assignments are usually short-term and not subject to long-term commitments. They often have a short deadline, require multiple items, and depend on multiple teams. Project managers will have to coordinate the team and assign resources.
Management of ad-hoc employees
Ad hoc jobs may require you manage multiple people who might not be on your payroll frequently. You must ensure they have the required skills and are available to work on the project. If this happens, you might need to contact other department managers. Decide how many people you will need and send out requests for the necessary resources.
A good system can make managing ad-hoc projects easier. This allows you to see how resources are being used. This will help you make more informed decisions regarding project management. It's crucial to keep track if you work with an ad hoc group.
You can either hire an outside contractor or internal employee to take on ad-hoc projects. They can be full-time or part-time, and they're great for projects that don't disrupt ongoing initiatives. You can be inefficient, waste your resources, and end up missing your project goals if you don't plan for the unexpected.
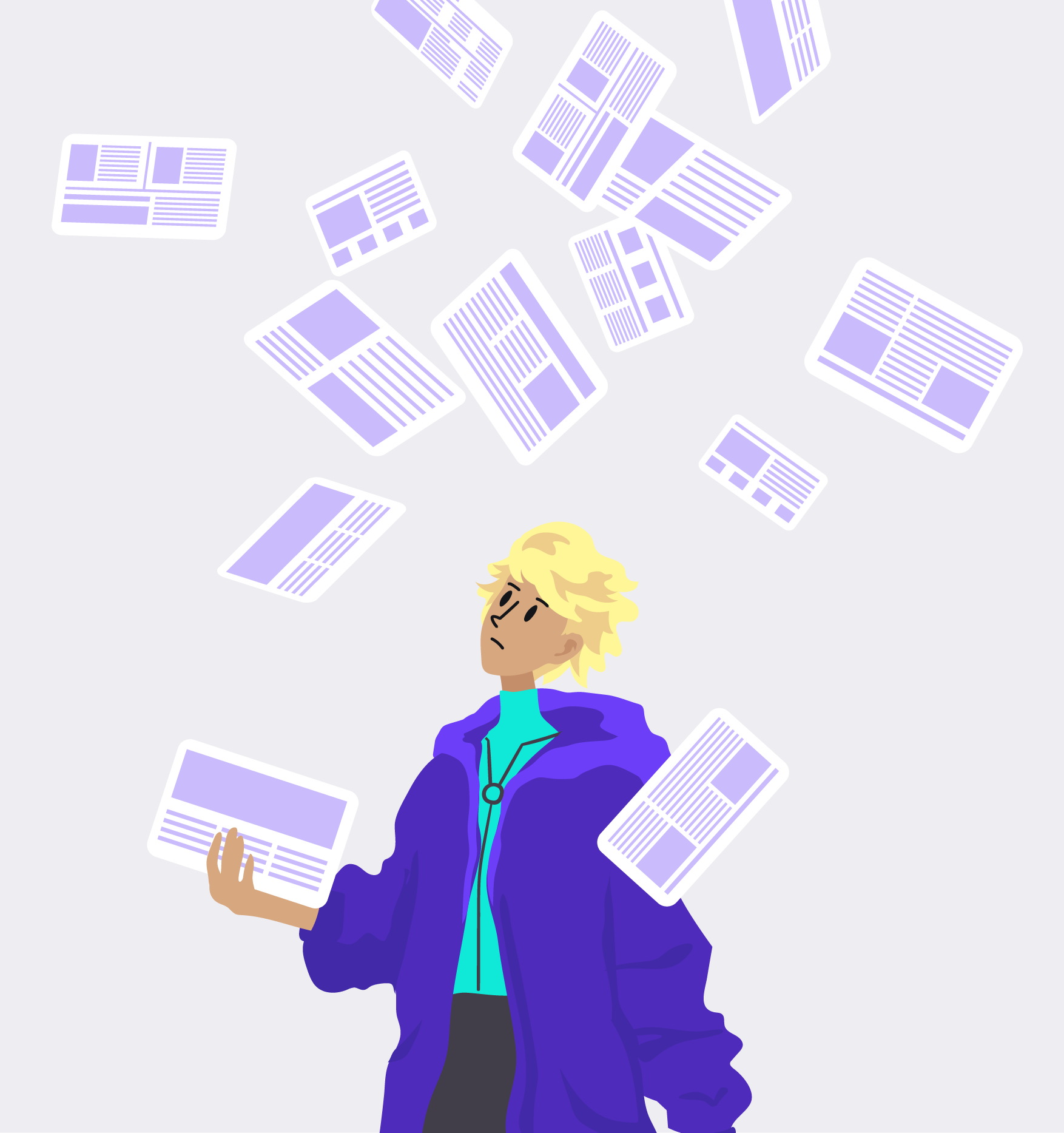
While ad hoc requests can be convenient, they can also bog down your entire team. Your marketing team should prioritize the requests and determine what is more important. Although ad-hoc requests can be an unfortunate part of maintaining customer satisfaction, you must know how to deal with them before they affect your team's productivity.
FAQ
What is a management tool to help with decision-making?
The decision matrix is a powerful tool that managers can use to help them make decisions. It allows them to think through all possible options.
A decision matrix is a way of representing alternatives as rows and columns. This makes it easy to see how each alternative affects other choices.
In this example, we have four possible alternatives represented by the boxes on the left side of the matrix. Each box represents an alternative. The top row represents the current state of affairs, and the bottom row is indicative of what would happen in the event that nothing were done.
The middle column shows the effect of choosing Option 1. In this example, it would lead to an increase in sales of between $2 million and $3 million.
The results of choosing Option 2 and 3 can be seen in the columns below. These are both positive changes that increase sales by $1million and $500,000. They also have negative consequences. Option 2 increases the cost of goods by $100,000. Option 3 decreases profits and makes them less attractive by $200,000.
The last column shows you the results of Option 4. This results in a decrease of sales by $1,000,000
A decision matrix has the advantage that you don’t have to remember where numbers belong. You just look at the cells and know immediately whether any given a choice is better than another.
This is because the matrix has done all the hard work. Simply compare the numbers within the cells.
Here's a sample of how you might use decision matrixes in your business.
You want to decide whether or not to invest more money into advertising. If you do this, you will be able to increase revenue by $5000 per month. You'll also have additional expenses up to $10,000.
If you look at the cell that says "Advertising", you can see the number $15,000. Advertising is worth much more than the investment cost.
What is the difference in Six Sigma and TQM?
The main difference between these two quality-management tools is that six-sigma concentrates on eliminating defects while total QM (TQM), focuses upon improving processes and reducing expenses.
Six Sigma is an approach for continuous improvement. This approach emphasizes eliminating defects through statistical methods like control charts, Pareto analysis, and p-charts.
This method aims to reduce variation in product production. This is achieved by identifying and addressing the root causes of problems.
Total quality management is the measurement and monitoring of all aspects within an organization. It also involves training employees to improve performance.
It is used to increase productivity.
Six Sigma is so beloved.
Six Sigma is simple to implement and can yield significant results. It also provides a framework for measuring improvements and helps companies focus on what matters most.
What is the difference in leadership and management?
Leadership is all about influencing others. Management is about controlling others.
Leaders inspire others, managers direct them.
Leaders inspire people to achieve success. Managers keep their workers focused.
A leader develops people; a manager manages people.
What are the 4 major functions of management
Management is responsible to plan, organize, direct, and control people and resources. It includes creating policies and procedures, as well setting goals.
Management helps an organization achieve its objectives by providing direction, coordination, control, leadership, motivation, supervision, training, and evaluation.
These are the four major functions of management:
Planning – Planning involves deciding what needs to happen.
Organizing – Organizing means deciding how to organize things.
Directing - Directing is when you get people to do what you ask.
Controlling – This refers to ensuring that tasks are carried out according to plan.
Statistics
- Hire the top business lawyers and save up to 60% on legal fees (upcounsel.com)
- The average salary for financial advisors in 2021 is around $60,000 per year, with the top 10% of the profession making more than $111,000 per year. (wgu.edu)
- Our program is 100% engineered for your success. (online.uc.edu)
- 100% of the courses are offered online, and no campus visits are required — a big time-saver for you. (online.uc.edu)
- This field is expected to grow about 7% by 2028, a bit faster than the national average for job growth. (wgu.edu)
External Links
How To
What is Lean Manufacturing?
Lean Manufacturing uses structured methods to reduce waste, increase efficiency and reduce waste. These processes were created by Toyota Motor Corporation, Japan in the 1980s. The goal was to produce quality products at lower cost. Lean manufacturing seeks to eliminate unnecessary steps and activities in the production process. It is made up of five elements: continuous improvement, continuous improvement, just in-time, continuous change, and 5S. Pull systems are able to produce exactly what the customer requires without extra work. Continuous improvement involves constantly improving upon existing processes. Just-in time refers to components and materials being delivered right at the place they are needed. Kaizen stands for continuous improvement. Kaizen can be described as a process of making small improvements continuously. Finally, 5S stands for sort, set in order, shine, standardize, and sustain. These five elements are used together to ensure the best possible results.
The Lean Production System
Six key concepts underlie the lean production system.
-
Flow is about moving material and information as near as customers can.
-
Value stream mapping - break down each stage of a process into discrete tasks and create a flowchart of the entire process;
-
Five S's, Sort, Set in Order, Shine. Standardize. and Sustain.
-
Kanban is a visual system that uses visual cues like stickers, colored tape or stickers to keep track and monitor inventory.
-
Theory of constraints: Identify bottlenecks and use lean tools such as kanban boards to eliminate them.
-
Just-in Time - Send components and material directly to the point-of-use;
-
Continuous improvement: Make incremental improvements to the process instead of overhauling it completely.