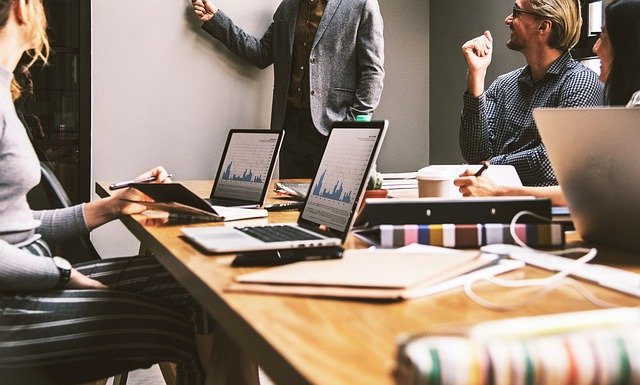
As a construction manager, you need to be familiar with mathematics. Basic construction projects, such as building a concrete wall, can require math. The concrete wall can measure 100 feet in length and be ten feet high. It may also be one foot thick. Brick veneer walls can also be built. These bricks would measure eight inches in length and three inches high. This is not an easy task so you will need to be more advanced in algebra and geometry.
Prerequisites for construction management degree
If you want to be a successful construction manager, it is important that you have a solid foundation in math. Math and statistics skills are important for general contractors and construction managers. Federal agencies often hire graduates. A high school diploma in math is required. Math is essential to all careers in construction. There are many levels in construction management. Students can choose from a variety of specialties, including general or heavy/civil building construction.
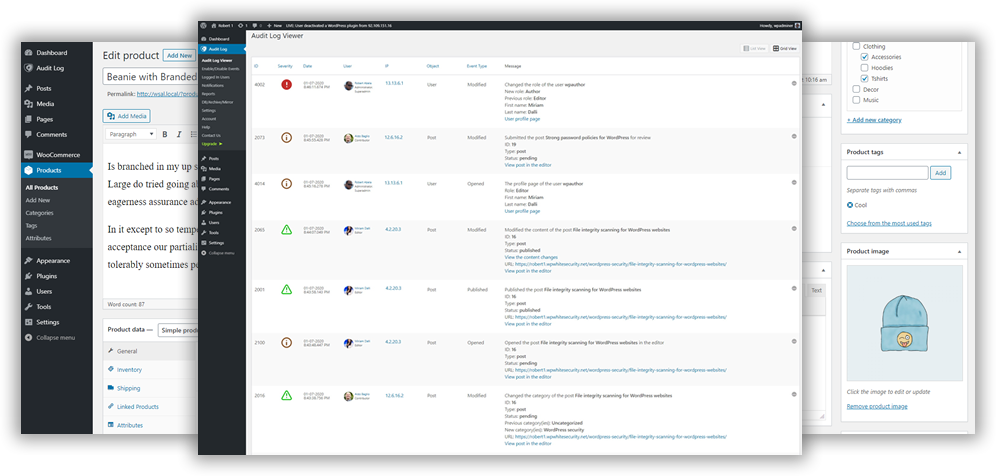
Precalculus math is essential for students who wish to study construction management master's degrees. The program will require students to understand the properties of materials and the mechanics of construction. It is important that students have an understanding of contracts and how to estimate. It is also important to be familiar with the use of computer programs in construction. This will assist students in preparing for various jobs in the industry. This course is required for all students interested in this field.
Construction management degrees require math and physics skills
Construction management degrees combine math and physical skills to help students manage large-scale construction projects. You'll learn about basic structural design and analysis, building layout, and materials testing. Additionally, you will learn how to read construction drawings. All technical courses are dependent on computers. This course will teach you about building information modelling and computer-aided design. This education combined with a solid foundation in industry standards and construction principles can make you a successful construction manager.
Surveying operations include horizontal measurement, differential leveling, transverse loop calculations, and other types of measurements. In addition, students learn how to interpret and create construction plans. They will also learn to use software programs to calculate costs, and prepare takeoffs. They will also be able to learn about quality assurance standards and cost estimating. Students will also learn electrical and mechanical systems. Finally, they will be able to get real experience in project management.
English and foreign languages are required for the construction management degree
A few requirements are common for construction management degrees. These include English and foreign languages. These courses usually take place in the first-year of the program. These courses should be completed by students with a minimum grade of C. Diverse course content with a strong focus on engineering and construction management principles is the main focus. Students must have a basic knowledge of law, economics, and business administration. Students also need to know some basic principles of structural design and equipment. Students must be knowledgeable about safety, health, environmental principles and other aspects of the profession.
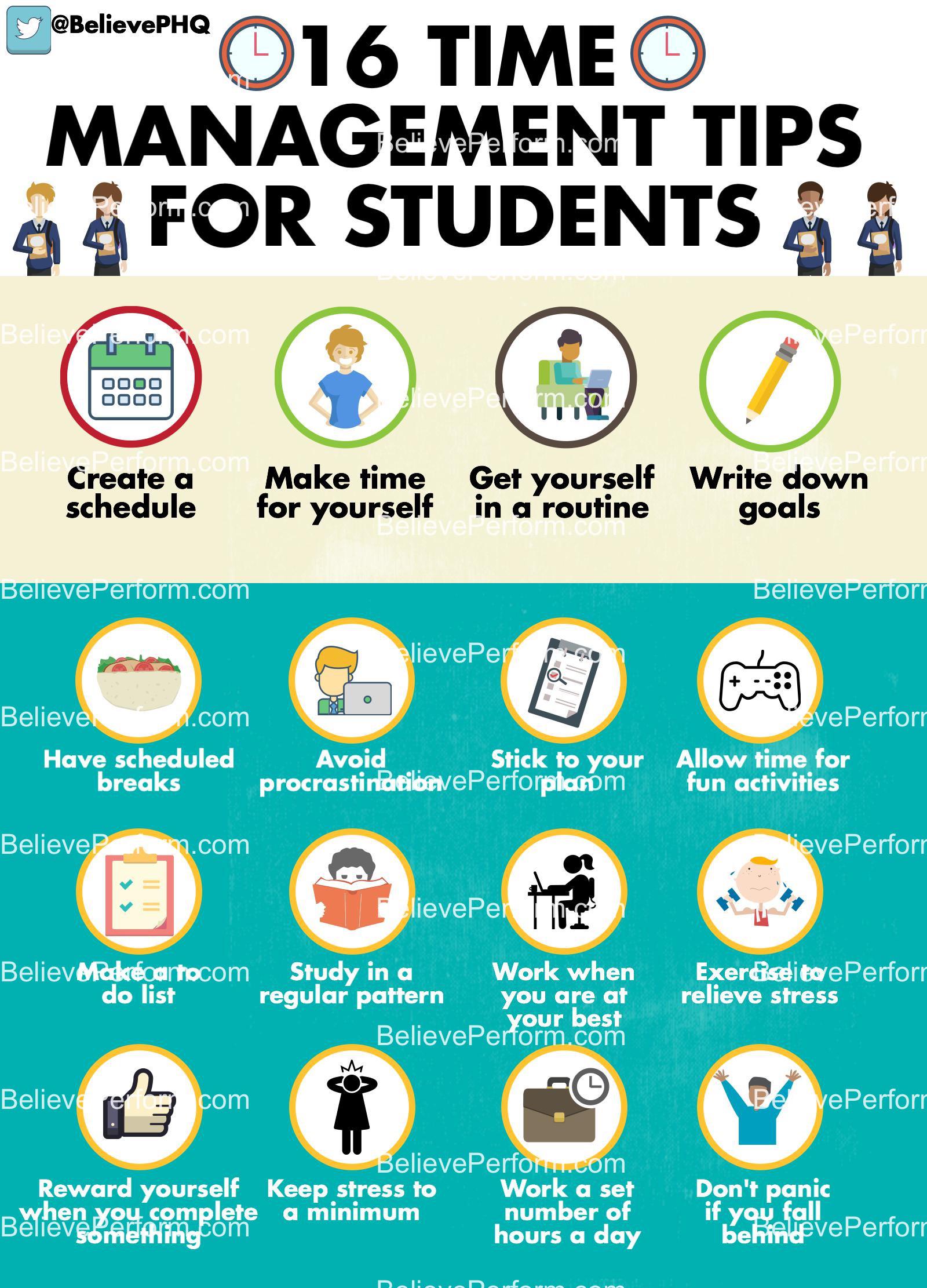
For the Master of Science in Construction Management degree, applicants must have a bachelor’s degree or an equivalent. They should also have relevant construction experience. Non-engineering applicants must also be willing to take any leveling courses that aren't part of the program plan. ToEFL scores will be required from students who come from non-English speaking universities. To be admitted to the program, you will need a TOEFL score greater than 550
FAQ
Six Sigma is so popular.
Six Sigma is easy and can deliver significant results. Six Sigma also gives companies a framework for measuring improvement and helps them focus on what is most important.
What is Six Sigma?
It's an approach to quality improvement that emphasizes customer service and continuous learning. The goal is to eradicate defects through statistical techniques.
Motorola created Six Sigma as part of their efforts to improve manufacturing processes in 1986.
The idea spread quickly throughout the industry, and today, many organizations are using six sigma methods to improve product design, production, delivery, and customer service.
What are the three basic management styles?
The three major management styles are authoritarian (left-faire), participative and laissez -faire. Each style has its advantages and disadvantages. Which style do YOU prefer? Why?
Authority - The leader is the one who sets the direction and expects everyone in the organization to follow it. This style is most effective when an organization is large, stable, and well-run.
Laissez-faire – The leader gives each individual the freedom to make decisions for themselves. This approach works best in small, dynamic organizations.
Participative – Leaders are open to suggestions and ideas from everyone. This style is best for small organizations where everyone feels valued.
What are management concepts, you ask?
Management Concepts are the principles and practices managers use to manage people and resources. These include topics such as human resource policies and job descriptions, performance assessments, training programs and employee motivation.
What are the most common errors made by managers?
Sometimes managers make it harder for their employees than is necessary.
They may not assign enough responsibilities to staff members and provide them with inadequate support.
Managers often lack the communication skills necessary to motivate and guide their teams.
Some managers set unrealistic expectations for their staff.
Managers may prefer to solve every problem for themselves than to delegate responsibility.
Statistics
- Hire the top business lawyers and save up to 60% on legal fees (upcounsel.com)
- The profession is expected to grow 7% by 2028, a bit faster than the national average. (wgu.edu)
- UpCounsel accepts only the top 5 percent of lawyers on its site. (upcounsel.com)
- The average salary for financial advisors in 2021 is around $60,000 per year, with the top 10% of the profession making more than $111,000 per year. (wgu.edu)
- As of 2020, personal bankers or tellers make an average of $32,620 per year, according to the BLS. (wgu.edu)
External Links
How To
How do I do the Kaizen Method?
Kaizen means continuous improvement. This term was first used by Toyota Motor Corporation in the 1950s. It refers to the Japanese philosophy that emphasizes continuous improvement through small incremental changes. It is a process where people come together to improve their processes.
Kaizen, a Lean Manufacturing method, is one of its most powerful. Employees responsible for the production line should identify potential problems in the manufacturing process and work together to resolve them. This way, the quality of products increases, and the cost decreases.
The main idea behind kaizen is to make every worker aware of what happens around him/her. If something is wrong, it should be corrected immediately so that no problem occurs. If someone spots a problem while at work, they should immediately report it to their manager.
Kaizen is based on a few principles. We always start from the end product and move toward the beginning. We can improve the factory by first fixing the machines that make it. First, we fix machines that produce components. Next, we fix machines that produce raw material. And finally, we fix the workers who work directly with those machines.
This is known as "kaizen", because it emphasizes improving each step. Once we have finished fixing the factory, we return to the beginning and work until perfection.
To implement kaizen in your business, you need to find out how to measure its effectiveness. There are several ways that you can tell if your kaizen system is working. One way is to examine the amount of defects on the final products. Another way is to see how much productivity has increased since implementing kaizen.
A good way to determine whether kaizen has been implemented is to ask why. You were trying to save money or obey the law? Did you really believe that it would be a success factor?
If you answered yes to any one of these questions, congratulations! You are ready to start kaizen.