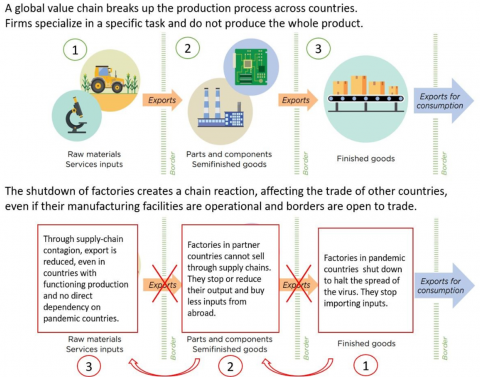
Ofshoring is often called outsourcing. This strategy allows companies to cut costs while keeping their core business in focus. It can also be a cost-effective way for companies increase their competitiveness. This article will discuss the benefits and drawbacks of outsourcing.
Offshoring refers to a form outsourcing
Offshoring can be used to lower costs by moving production or service to another country. The practice can be used for various purposes, such as reducing labor costs or lowering the price of product and services. But offshoring doesn't always improve efficiency.
Offshoring involves the hiring of an outside team to perform a certain task. This outsourcing involves repetitive, monotonous, and time-consuming tasks. These tasks are outsourced to increase productivity, efficiency, quality, and work efficiency. These tasks are usually done in-house but many of them cannot be done by one person, making them ideal for offshoring.
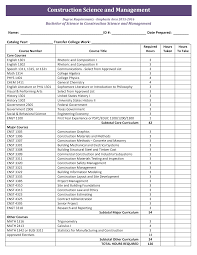
It is cost-savings.
Outsourcing can be a cost-saving strategy for companies. Outsourcing can be beneficial for companies in different industries. Additionally, it can increase shareholder value. Outsourcing can provide companies with the opportunity to improve their core competencies, enhance IT knowledge and implement planned upgrades within them. However, outsourcing business operations can be complex.
Outsourcing reduces the amount of time staff spends on non-core tasks, such as telemarketing or technical support. They can now focus on other business areas, such as product development. This allows them to focus on other areas of business, such as product development. This allows them to focus on new product and service ideas, which will help the company grow.
It allows companies to focus on their core business
Companies are increasingly looking for ways to save money and increase productivity. Outsourcing common functions include customer service, design, content, legal services, accounting, customer support, marketing, customer care, marketing, customer management, design, content, legal, and human resources. Employing outside help to complete these tasks will allow companies to concentrate on their core strengths, which can reduce payroll expenses. Outsourcing also allows companies to focus on their core competencies, such as product development and sales.
Outsourcing can reduce risk for businesses. A lot of outside providers have experienced staff that can provide valuable insight and advice. This makes it easy to make necessary changes. If call volume fluctuates, for example, an outsourcing customer service team can add agents quickly. A provider can scale up and down according to the need for marketing and accounting functions.
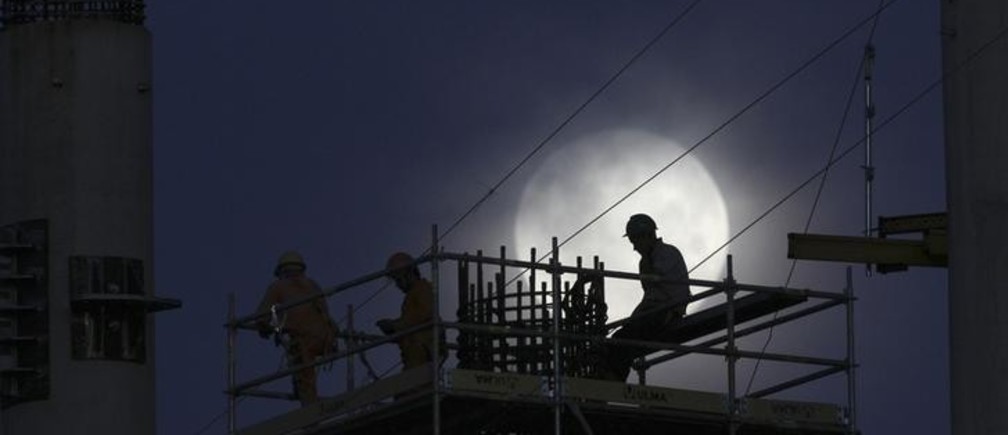
It enhances their competitiveness
Companies are beginning to see the value of outsourcing non-core functions and are building strong vendor-purchaser relationships. This type of relationship involves complete partnership between the organizations involved and regular reviews of progress and performance. It helps to ensure the vendor is working in the organisation's best interest and also provides a means for resolving problems. There are risks associated with outsourcing. Companies must be cautious when choosing partners to outsource.
Outsourcing gives companies the opportunity to tap into a global network of knowledge and resources. Companies that specialize on outsourcing invest considerable time and money in selecting the best experts. This allows them not only to be competitive but also ensures that their customers receive the best quality service at the most affordable price.
FAQ
What is a management tool to help with decision-making?
A decision matrix, a simple yet powerful tool for managers to make decisions, is the best. They can think about all options and make informed decisions.
A decision matrix allows you to represent alternatives as columns and rows. This allows you to easily see how each choice affects others.
This example shows four options, each represented by the boxes on either side of the matrix. Each box represents a different option. The top row represents the current state of affairs, and the bottom row is indicative of what would happen in the event that nothing were done.
The middle column displays the impact of selecting Option 1. In this case, it would mean increasing sales from $2 million to $3 million.
The effects of options 2 and 3 are shown in the next columns. These are good changes, they increase sales by $1million or $500,000. However, these also involve negative consequences. Option 2 increases the cost of goods by $100,000. Option 3 decreases profits and makes them less attractive by $200,000.
The final column shows the results for Option 4. This will result in sales falling by $1,000,000
The best part about using a decision matrix to guide you is that you don’t need to keep track of which numbers go where. You just look at the cells and know immediately whether any given a choice is better than another.
This is because the matrix has already taken care of the hard work for you. It is as simple a matter of comparing all the numbers in each cell.
Here's a sample of how you might use decision matrixes in your business.
You need to decide whether to invest in advertising. If you do, you'll be able to increase your revenue by $5 thousand per month. But, you will also incur additional expenses of $10 thousand per month.
Look at the cell immediately below the one that states "Advertising" to calculate the net investment in advertising. It's $15,000. Advertising is worth much more than the investment cost.
What are the four major functions of Management?
Management is responsible in planning, organizing and directing people and resources. Management also involves setting goals and developing policies.
Management is the ability to direct, coordinate, control, motivate, supervise, train, and evaluate an organization's efforts towards achieving its goals.
The following are the four core functions of management
Planning - This is the process of deciding what should be done.
Organizing - Organization involves deciding what should be done.
Directing - Directing is when you get people to do what you ask.
Controlling: Controlling refers to making sure that people do what they are supposed to.
Which kind of people use Six Sigma
People who have worked with statistics and operations research will usually be familiar with the concepts behind six sigma. Anyone involved in business can benefit.
Because it requires a high degree of commitment, only leaders with strong leadership skills can implement it successfully.
Statistics
- Our program is 100% engineered for your success. (online.uc.edu)
- As of 2020, personal bankers or tellers make an average of $32,620 per year, according to the BLS. (wgu.edu)
- 100% of the courses are offered online, and no campus visits are required — a big time-saver for you. (online.uc.edu)
- The profession is expected to grow 7% by 2028, a bit faster than the national average. (wgu.edu)
- The BLS says that financial services jobs like banking are expected to grow 4% by 2030, about as fast as the national average. (wgu.edu)
External Links
How To
What is Lean Manufacturing?
Lean Manufacturing techniques are used to reduce waste while increasing efficiency by using structured methods. These processes were created by Toyota Motor Corporation, Japan in the 1980s. It was designed to produce high-quality products at lower prices while maintaining their quality. Lean manufacturing focuses on eliminating unnecessary steps and activities from the production process. It consists of five basic elements: pull systems, continuous improvement, just-in-time, kaizen (continuous change), and 5S. It is a system that produces only the product the customer requests without additional work. Continuous improvement is constantly improving upon existing processes. Just-in-time refers to when components and materials are delivered directly to the point where they are needed. Kaizen is continuous improvement. This can be achieved by making small, incremental changes every day. Finally, 5S stands for sort, set in order, shine, standardize, and sustain. These five elements work together to produce the best results.
Lean Production System
Six key concepts underlie the lean production system.
-
Flow - focuses on moving information and materials as close to customers as possible.
-
Value stream mapping is the ability to divide a process into smaller tasks, and then create a flowchart that shows the entire process.
-
Five S's, Sort, Set in Order, Shine. Standardize. and Sustain.
-
Kanban is a visual system that uses visual cues like stickers, colored tape or stickers to keep track and monitor inventory.
-
Theory of constraints: Identify bottlenecks and use lean tools such as kanban boards to eliminate them.
-
Just-in time - Get components and materials delivered right at the point of usage;
-
Continuous improvement - Make incremental improvements rather than overhauling the entire process.