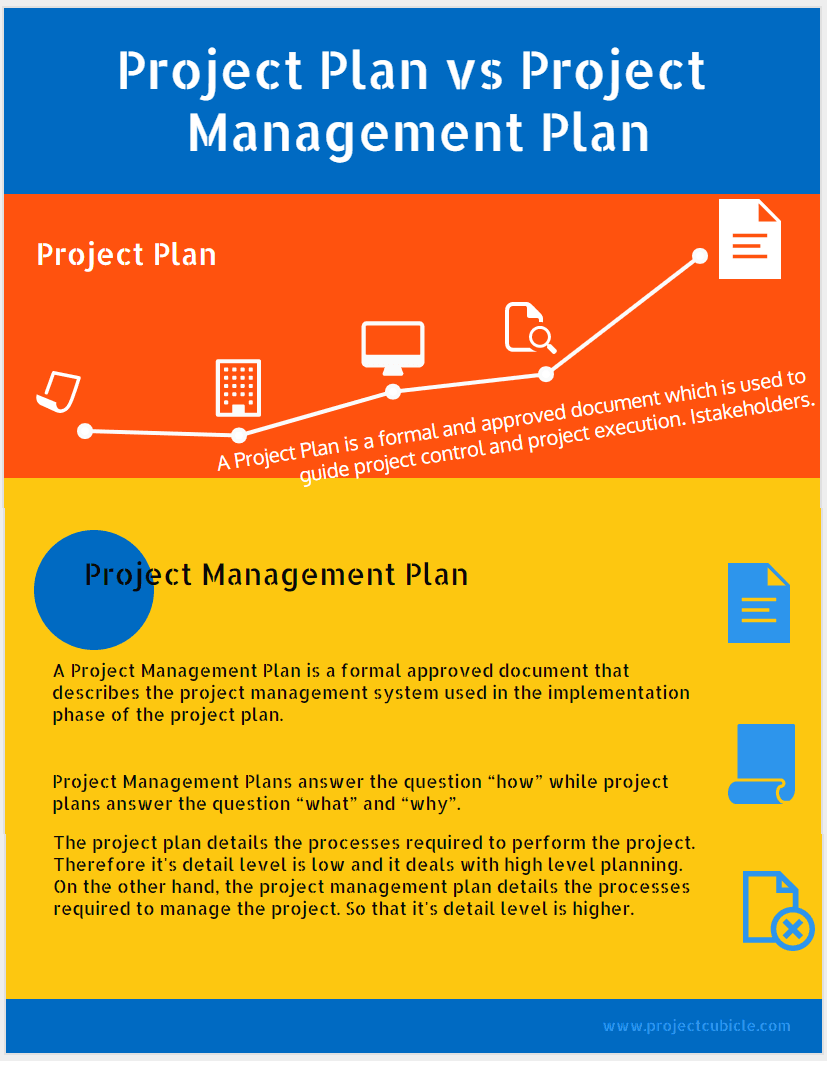
The skills and qualifications required to work in construction are essential. There are several different occupations in the construction industry. These classes will help to explain the different trades you can choose from in the construction sector. You'll also learn how you can use specifications, plans, specifications and green technologies. You will also get to practice the use of power tools and measuring equipment.
Overview of the Construction Industry
Many types of work are part of the construction industry. There are many types of projects. Some are smaller than others. Others require a lot of expertise and services. There are also companies that specialize in particular types of work. This article will examine the differences between the construction sector and other industries, as well as the roles that different types play in the industry.
Although the overall growth rate of the construction industry has been slow, it still faces many challenges. Increasing population means more stress on housing and infrastructure.
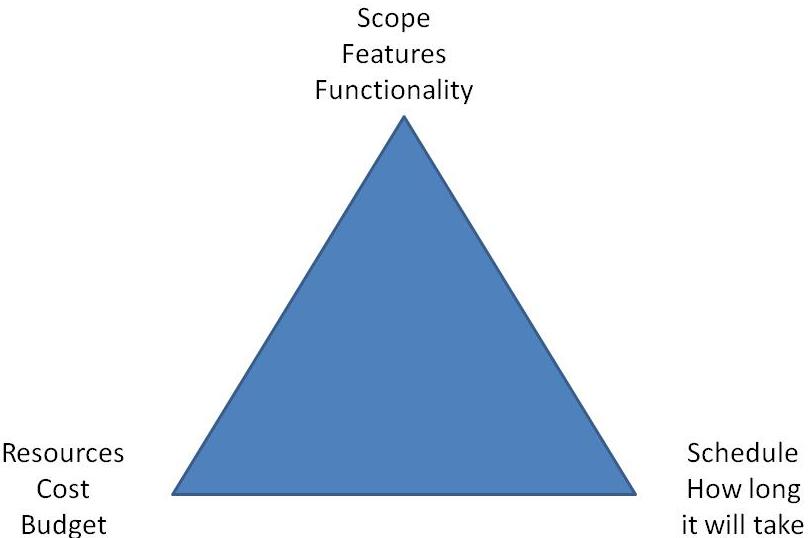
Opportunities for career advancement in the industry
There are many options for anyone interested in working in construction. There are many options for you to get started in this field. The Bureau of Labor Statistics expects that the construction industry will expand by nearly 10% over the next decade. It is a promising career choice. This industry is highly diverse with increasing numbers of minorities and women choosing to work there.
The construction industry offers a variety of career options for those with an engineering or construction degree. You could be a project manager if you are a problem solver. These professionals are responsible for overseeing all aspects a construction project's execution, including planning and budgeting. They should have exceptional problem-solving abilities and strong leadership skills. A degree in surveying or civil engineering is also required. Many project managers start out as construction engineers.
Required skills to work within the industry
You will need a variety of skills to perform a construction job. It is essential that you are able to accurately calculate the dimensions and understand construction documents. Basic math and English language skills are also necessary. Effective communication is essential when working in a construction environment.
Construction skills include bricklaying, carpentry and pouring cement. Other skills include using specific equipment or putting up drywall. In addition, the ability to think critically and work under tight deadlines is critical for any construction position. To succeed in the construction sector, you'll need a range of soft abilities, such as communication skills, conflict management, and collaboration.
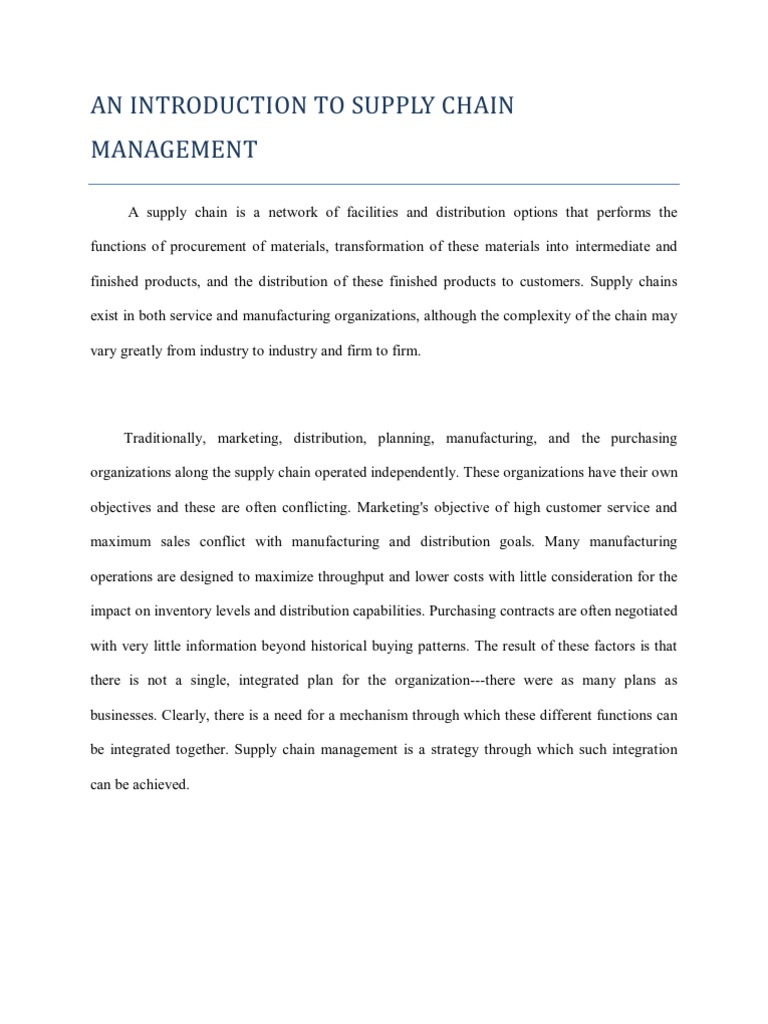
For entry to the industry, you must have a degree.
There are different educational requirements that you need to be able to work in the construction industry, depending on which type of occupation. Apprenticeship programs and college courses will help you acquire the knowledge and skills needed to succeed within this industry. You can also take an OSHA certification course to get a better understanding of safety regulations. Specialty certifications are available that allow you to be trained for certain work environments. These courses may be taken online, but you will need to do hands-on training.
An associate's or certificate in construction management can be earned. It takes approximately two years to complete a construction management program. You will gain the practical skills you need to be successful in the field. You can also choose a program that teaches you the business side of the industry.
FAQ
What are the five management process?
The five stages of a business include planning, execution (monitoring), review, evaluation, and review.
Planning involves setting goals for the future. Planning involves defining your goals and how to get there.
Execution is the actual execution of the plans. These plans must be adhered to by everyone.
Monitoring is checking on progress towards achieving your objectives. Monitoring should include regular reviews of performance against goals and budgets.
Review events take place at each year's end. They are a chance to see if everything went smoothly during the year. If not, then it may be possible to make adjustments in order to improve performance next time.
After the annual review, evaluation takes place. It helps you identify the successes and failures. It also provides feedback on how well people performed.
What are the 4 main functions of management?
Management is responsible in planning, organizing and directing people and resources. It also includes developing policies and procedures and setting goals.
Management assists an organization in achieving its goals by providing direction, coordination and control, leadership, motivation, supervision and training, as well as evaluation.
The four main functions of management are:
Planning - This is the process of deciding what should be done.
Organizing is the act of deciding how things should go.
Direction - This is the art of getting people to follow your instructions.
Controlling – This refers to ensuring that tasks are carried out according to plan.
What are the main management skills?
Any business owner needs to be able to manage people, finances, resources and time. These skills include the ability manage people, finances and resources as well as other factors.
These skills are necessary for setting goals and objectives as well as planning strategies, leading groups, motivating employees and solving problems.
As you can see there is no end to the number of managerial tasks.
What does the term "project management” mean?
This refers to managing all activities that are involved in a project's execution.
We help you define the scope of your project, identify the requirements, prepare the budget, organize the team, plan the work, monitor progress and evaluate the results before closing down the project.
What are the steps of the management decision-making process?
Managers face complex and multifaceted decision-making challenges. It involves many elements, including analysis, strategy. planning. implementation. measurement. evaluation. feedback.
It is important to remember that people are human beings, just like you. They make mistakes. As such, there are always opportunities for improvement, especially when you put in the effort to improve yourself.
In this video, we explain what the decision-making process looks like in Management. We will explain the importance of different types decisions and how every manager can make them. Here are some topics you'll be learning about:
What's the difference between Six Sigma and TQM?
The major difference between the two tools for quality management is that six Sigma focuses on eliminating defect while total quality control (TQM), on improving processes and decreasing costs.
Six Sigma can be described as a strategy for continuous improvement. It emphasizes the elimination and improvement of defects using statistical methods, such as control charts, P-charts and Pareto analysis.
This method seeks to decrease variation in product output. This is achieved by identifying and addressing the root causes of problems.
Total quality management refers to the monitoring and measurement of all aspects in an organization. It also includes the training of employees to improve performance.
It is frequently used as an approach to increasing productivity.
What are some of the common mistakes made by managers?
Managers can make their jobs more difficult than necessary.
They may not assign enough responsibilities to staff members and provide them with inadequate support.
Managers often lack the communication skills necessary to motivate and guide their teams.
Some managers create unrealistic expectations for their teams.
Some managers may try to solve every problem themselves instead of delegating responsibility to others.
Statistics
- 100% of the courses are offered online, and no campus visits are required — a big time-saver for you. (online.uc.edu)
- As of 2020, personal bankers or tellers make an average of $32,620 per year, according to the BLS. (wgu.edu)
- Your choice in Step 5 may very likely be the same or similar to the alternative you placed at the top of your list at the end of Step 4. (umassd.edu)
- This field is expected to grow about 7% by 2028, a bit faster than the national average for job growth. (wgu.edu)
- The BLS says that financial services jobs like banking are expected to grow 4% by 2030, about as fast as the national average. (wgu.edu)
External Links
How To
How does Lean Manufacturing work?
Lean Manufacturing uses structured methods to reduce waste, increase efficiency and reduce waste. They were developed in Japan by Toyota Motor Corporation (in the 1980s). It was designed to produce high-quality products at lower prices while maintaining their quality. Lean manufacturing eliminates unnecessary steps and activities from a production process. It has five components: continuous improvement and pull systems; just-in time; continuous change; and kaizen (continuous innovation). The production of only what the customer needs without extra work is called pull systems. Continuous improvement refers to continuously improving existing processes. Just-in-time is when components and other materials are delivered at their destination in a timely manner. Kaizen is continuous improvement. This can be achieved by making small, incremental changes every day. Finally, 5S stands for sort, set in order, shine, standardize, and sustain. These five elements work together to produce the best results.
Lean Production System
Six key concepts form the foundation of the lean production system:
-
Flow: The goal is to move material and information as close as possible from customers.
-
Value stream mapping: This is a way to break down each stage into separate tasks and create a flowchart for the entire process.
-
Five S's, Sort, Set in Order, Shine. Standardize. and Sustain.
-
Kanban - visual cues such as stickers or colored tape can be used to track inventory.
-
Theory of constraints: Identify bottlenecks and use lean tools such as kanban boards to eliminate them.
-
Just-in-time - deliver components and materials directly to the point of use;
-
Continuous improvement - make incremental improvements to the process rather than overhauling it all at once.