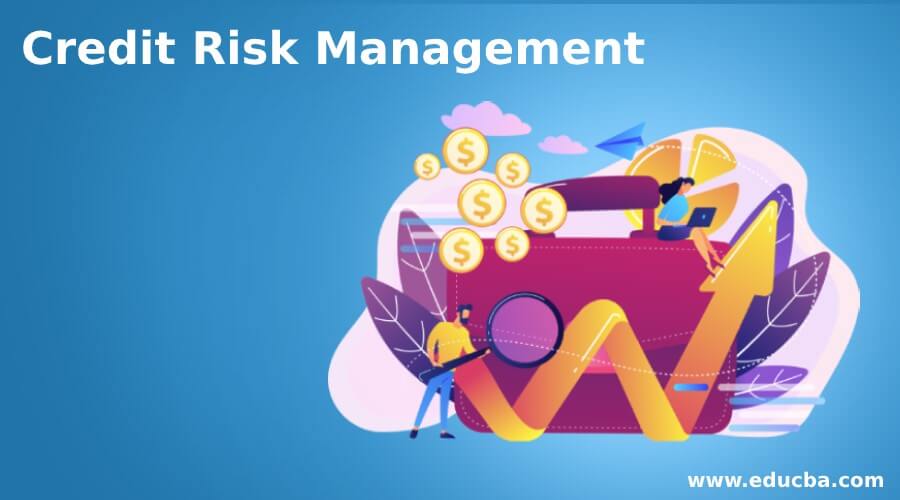
Mismanagement refers when you make a mess or attempt to do something wrong. This can range from spending money to the wrong things, or even breaching legal obligations. Mismanagement can also occur when there is a conflict of opinions. Here are some instances. Here are some examples of workplace mismanagement.
It requires a difference of opinions
Mismanagement refers to activities that are perceived as a waste. This label is often associated with grudges, which can lead to less money for your pet projects. Common examples include spending "too much" on internationalization, prioritizing a field of study over another field, or constructing a new building. Mismanagement can also be due to disagreements regarding institutional goals.
It can be considered a breach or contract violation.
Mismanagement is a type of business practice that involves a breach of legal or contractual obligations. While most business contracts are designed for the benefit of all parties involved in the transaction, sometimes delays or financial problems can prevent a contract's fulfillment from being done as agreed. The parties involved may sue each other for breaching contract if this happens.
FAQ
What is the main difference between Six Sigma Six Sigma TQM and Six Sigma Six Sigma?
The main difference between these two quality management tools is that six sigma focuses on eliminating defects while total quality management (TQM) focuses on improving processes and reducing costs.
Six Sigma is an approach for continuous improvement. It emphasizes the elimination and improvement of defects using statistical methods, such as control charts, P-charts and Pareto analysis.
This method has the goal to reduce variation of product output. This is accomplished by identifying the root cause of problems and fixing them.
Total quality management refers to the monitoring and measurement of all aspects in an organization. It also includes training employees to improve performance.
It is often used to increase productivity.
What do we mean when we say "project management"?
That is the management of all activities associated with a project.
Our services include the definition of the scope, identifying requirements, preparing a budget, organizing project teams, scheduling work, monitoring progress and evaluating the results before closing the project.
What is a fundamental management tool for decision-making?
The decision matrix is a powerful tool that managers can use to help them make decisions. They can think about all options and make informed decisions.
A decision matrix represents alternatives in rows and columns. This allows one to see how each alternative impacts other options.
The boxes on the left hand side of this matrix represent four possible choices. Each box represents one option. The top row represents the current state of affairs, and the bottom row is indicative of what would happen in the event that nothing were done.
The middle column displays the impact of selecting Option 1. It would increase sales by $2 million to 3 million in this instance.
The results of choosing Option 2 and 3 can be seen in the columns below. These positive changes result in increased sales of $1 million and $500,000. These positive changes have their downsides. For instance, Option 2 increases cost by $100 thousand while Option 3 reduces profits by $200 thousand.
The final column shows results of choosing Option 4. This results in a decrease of sales by $1,000,000
The best thing about using a decision matrix is that you don't need to remember which numbers go where. The best thing about a decision matrix is that you can simply look at the cells, and immediately know whether one option is better or not.
This is because the matrix has already taken care of the hard work for you. Simply compare the numbers within the cells.
Here's an example of how you might use a decision matrix in your business.
You want to decide whether or not to invest more money into advertising. This will allow you to increase your revenue by $5000 per month. You'll also have additional expenses up to $10,000.
Look at the cell immediately below the one that states "Advertising" to calculate the net investment in advertising. It's $15,000. Advertising is worth more than its cost.
Six Sigma is so popular.
Six Sigma is easy and can deliver significant results. It provides a framework that allows for improvement and helps companies concentrate on what really matters.
What are the most important management skills?
Any business owner needs to be able to manage people, finances, resources and time. These include the ability and willingness to manage people, finances as well resources, time and space.
Managerial skills are required when setting goals and objectives and planning strategies, leading employees, motivating them, solving problems, creating policies, procedures, or managing change.
There are so many managerial tasks!
Statistics
- Your choice in Step 5 may very likely be the same or similar to the alternative you placed at the top of your list at the end of Step 4. (umassd.edu)
- As of 2020, personal bankers or tellers make an average of $32,620 per year, according to the BLS. (wgu.edu)
- UpCounsel accepts only the top 5 percent of lawyers on its site. (upcounsel.com)
- The BLS says that financial services jobs like banking are expected to grow 4% by 2030, about as fast as the national average. (wgu.edu)
- Our program is 100% engineered for your success. (online.uc.edu)
External Links
How To
How can you implement the Kaizen technique?
Kaizen means continuous improvement. The Japanese philosophy emphasizes small, incremental improvements to achieve continuous improvement. This term was created by Toyota Motor Corporation in 1950. It is a process where people come together to improve their processes.
Kaizen, a Lean Manufacturing method, is one of its most powerful. In this concept, employees who are responsible for the production line must identify problems that exist during the manufacturing process and try to solve them before they become big issues. This improves the quality of products, while reducing the cost.
Kaizen is the idea that every worker should be aware of what is going on around them. So that there is no problem, you should immediately correct it if something goes wrong. If someone is aware of a problem at work, he/she should inform his/her manager immediately.
Kaizen is based on a few principles. We always start from the end product and move toward the beginning. For example, if we want to improve our factory, we first fix the machines that produce the final product. Next, we fix the machines which produce components. Then, we fix those who work directly with the machines.
This is why it's called "kaizen" because it works step-by-step to improve everything. When we are done fixing the whole factory, we go back to the beginning and continue until we reach perfection.
Before you can implement kaizen into your business, it is necessary to learn how to measure its effectiveness. There are many ways you can determine if kaizen has been implemented well. One way is to examine the amount of defects on the final products. Another way is to check how much productivity has grown since kaizen was implemented.
To determine if kaizen is effective, you should ask yourself why you chose to implement kaizen. Did you do it because it was legal or to save money? Did you really believe that it would be a success factor?
If you answered yes to any one of these questions, congratulations! Now you're ready for kaizen.