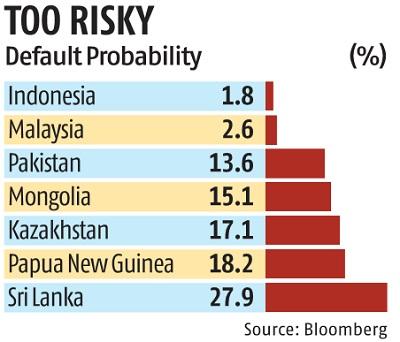
The SCOR model is used in supply-chain management. It can be divided into Levels which represent the levels of the model. Level one relates to the Make process. Level two can be divided into three subprocesses. Each sub-process has its own special tag that represents the beginning of the process. Child-related tags are identified with a number. A scenario is represented by the number. Additionally, there are four types of references. These are the Reference components, the Prescriptive analytics framework, and the Four-tiered analytics framework.
Levels of SCOR Model
SCOR is a model that combines concepts of measurement, benchmarking, and reengineering. It creates a comprehensive view of business processes. It provides a consistent approach to supply-chain evaluation and identifies areas where improvements can be made. This model is applicable to any industry that has a supply network. First, define the scope of your project. This includes context, geography, and key components.
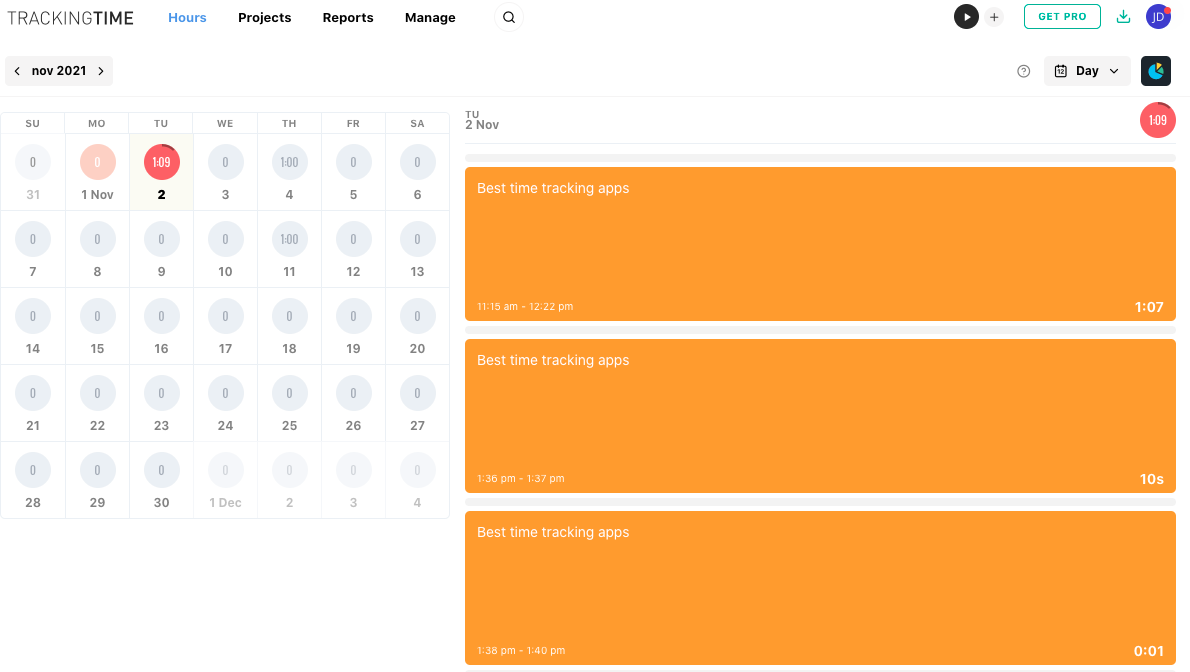
SCOR Model is a multi-industry model that focuses on products, services and transactions. The basic framework is source, make, deliver, and return. While the model may be useful, it loses its value if there is ambiguity in purpose, strategic alignment, and operational excellence. The business context study examines the organization's performance in relation to customers and other companies. It also identifies conformance gaps. You will need to use tools such a SWOT Analysis and Benchmarking as well as Value Stream Mapping to help you analyze your business context.
Four pillars in supply-chain management
Supply-chain management should be in sync with the company’s strategy, financial and service factors. Companies can have confidence in the management of their supply-chain process by focusing on these areas. These four pillars cover many topics such as product integrity, quality and capacity, fraud, and supply-chain management. To make supply chain management work, companies must align these areas to achieve business objectives.
Planning and implementation are critical components of the supply-chain process. Companies can reduce their costs and avoid being short of goods by managing inventory properly. A supply chain that is efficient requires qualified purchasing staff who are familiar with how to manage and maintain inventory. A company without qualified personnel will either overbuy raw materials, or run out, which can lead to financial strain. A company's performance is directly affected by its supply chain.
Framework for Prescriptive Analytics
Predictive analytics frameworks use algorithms that allow computers make decisions based upon statistical data relationships. Bayes classifier or ID3 are two examples of predictive analytics algorithms. These structures graphs show potential outcomes from a given dataset. Predictive Analytics is a technique that creates models based on past data to predict future events. AI and predictive analytics are tools that help companies predict future results or predict customer behavior.
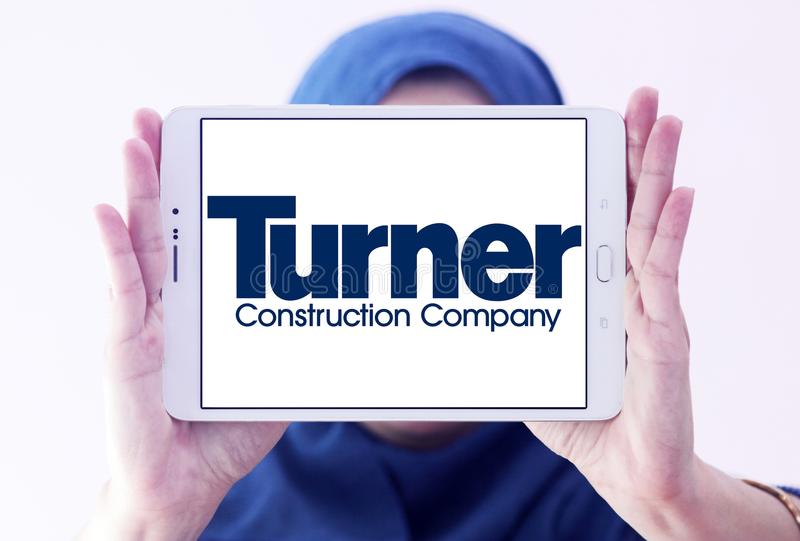
This approach uses machine learning algorithms for large data sets processing and making recommendations based on particular requirements. These algorithms may not be as accurate as human judgment, so they will still require human discernment. Prescriptive analysis can be extremely helpful for businesses, especially in sales. Based on their data, predictive analytics algorithms can assist salespeople in making more informed decisions. Marketers can identify trends and tailor their strategies to customer behavior by identifying them.
FAQ
What is the difference between a project and a program?
A program is permanent while a project can be temporary.
A project typically has a defined goal and deadline.
It is often performed by a team of people, who report back on someone else.
A program often has a set goals and objectives.
It is often done by one person.
What is Six Sigma, exactly?
This is a method of quality improvement that emphasizes customer service, continuous learning, and customer service. The goal is to eradicate defects through statistical techniques.
Motorola invented Six Sigma in 1986 as part its efforts to improve manufacturing.
The idea spread quickly throughout the industry, and today, many organizations are using six sigma methods to improve product design, production, delivery, and customer service.
How do we build a culture that is successful in our company?
A successful company culture is one that makes people feel valued and respected.
It is founded on three basic principles:
-
Everybody has something of value to share
-
People are treated fairly
-
People and groups should respect each other.
These values can be seen in the behavior of people. They will treat others with kindness and consideration.
They will listen to other people's opinions respectfully.
They encourage others to express their feelings and ideas.
Additionally, the company culture encourages open communication as well as collaboration.
People can freely express their opinions without fear or reprisal.
They know that they will not be judged if they make mistakes, as long as the matter is dealt with honestly.
Finally, the company culture encourages honesty as well as integrity.
Everyone is aware that truth must be told.
Everyone recognizes that rules and regulations are important to follow.
Nobody expects to be treated differently or given favors.
What are the key management skills?
No matter if they are running a local business or an international one, management skills are vital. These skills include the ability of managing people, finances, time, space, and other factors.
Management Skills are also needed when you're setting goals and objectives, planning strategies, leading teams, motivating employees, resolving problems, creating policies and procedures, and managing change.
As you can see, there's no end to the list of managerial duties!
What is the difference between management and leadership?
Leadership is about inspiring others. Management is about controlling others.
A leader inspires his followers while a manager directs the workers.
Leaders inspire people to achieve success. Managers keep their workers focused.
A leader develops people; a manager manages people.
What does Six Sigma mean?
Six Sigma uses statistical analyses to locate problems, measure them, analyze root cause, fix problems and learn from the experience.
The first step in solving a problem is to identify it.
The next step is to collect data and analyze it in order to identify trends or patterns.
Then corrective actions are taken to solve the problem.
Finally, data will be reanalyzed to determine if there is an issue.
This cycle continues until the problem is solved.
Statistics
- The profession is expected to grow 7% by 2028, a bit faster than the national average. (wgu.edu)
- The BLS says that financial services jobs like banking are expected to grow 4% by 2030, about as fast as the national average. (wgu.edu)
- 100% of the courses are offered online, and no campus visits are required — a big time-saver for you. (online.uc.edu)
- UpCounsel accepts only the top 5 percent of lawyers on its site. (upcounsel.com)
- As of 2020, personal bankers or tellers make an average of $32,620 per year, according to the BLS. (wgu.edu)
External Links
How To
What is Lean Manufacturing?
Lean Manufacturing processes are used to reduce waste and improve efficiency through structured methods. They were created in Japan by Toyota Motor Corporation during the 1980s. The goal was to produce quality products at lower cost. Lean manufacturing seeks to eliminate unnecessary steps and activities in the production process. It consists of five basic elements: pull systems, continuous improvement, just-in-time, kaizen (continuous change), and 5S. The production of only what the customer needs without extra work is called pull systems. Continuous improvement is constantly improving upon existing processes. Just-in time refers to components and materials being delivered right at the place they are needed. Kaizen stands for continuous improvement. Kaizen can be described as a process of making small improvements continuously. Five-S stands for sort. It is also the acronym for shine, standardize (standardize), and sustain. These five elements are combined to give you the best possible results.
The Lean Production System
Six key concepts are the basis of lean production:
-
Flow - focus on moving material and information as close to customers as possible;
-
Value stream mapping - break down each stage of a process into discrete tasks and create a flowchart of the entire process;
-
Five S’s - Sorted, In Order. Shine. Standardize. And Sustain.
-
Kanban is a visual system that uses visual cues like stickers, colored tape or stickers to keep track and monitor inventory.
-
Theory of constraints - identify bottlenecks during the process and eliminate them with lean tools like Kanban boards.
-
Just-in time - Get components and materials delivered right at the point of usage;
-
Continuous improvement - incremental improvements are made to the process, not a complete overhaul.