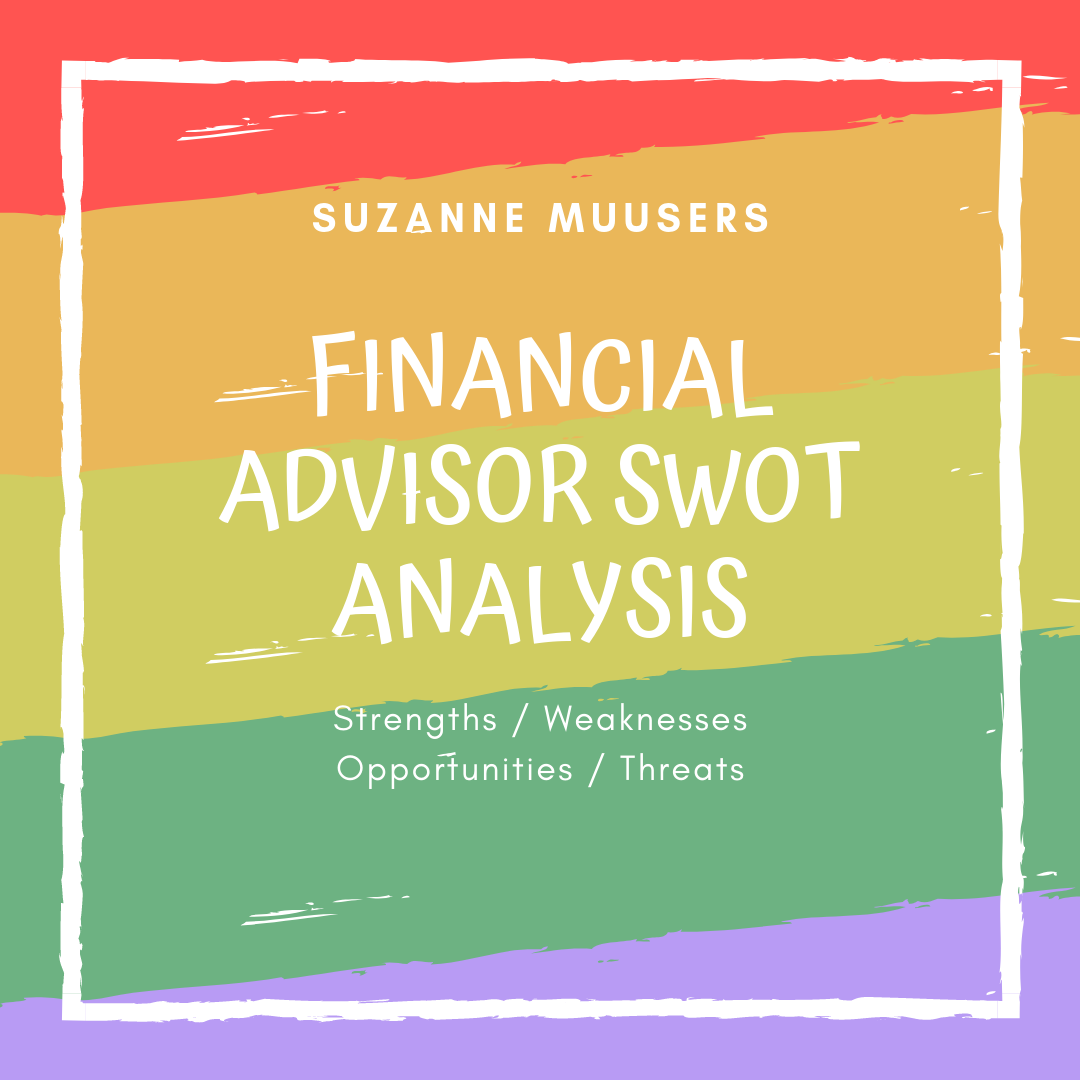
Here are the top methods to reduce your carbon footprint and lower your supply chain's emission. These include engaging stakeholders, managing sustainable procurement, and taking responsibility. This will allow you to create a more sustainable, predictable supply chain.
Engagement of stakeholders
The successful engagement of stakeholders is critical to the long-term success of a company's sustainability efforts. Engaging stakeholders can help speed up your sustainability journey. With robust engagement strategies, companies can develop a collaborative culture and effectively work with multiple stakeholders. In addition to improving the supply chain, engaging stakeholders helps a company gain valuable insights on risks and opportunities.
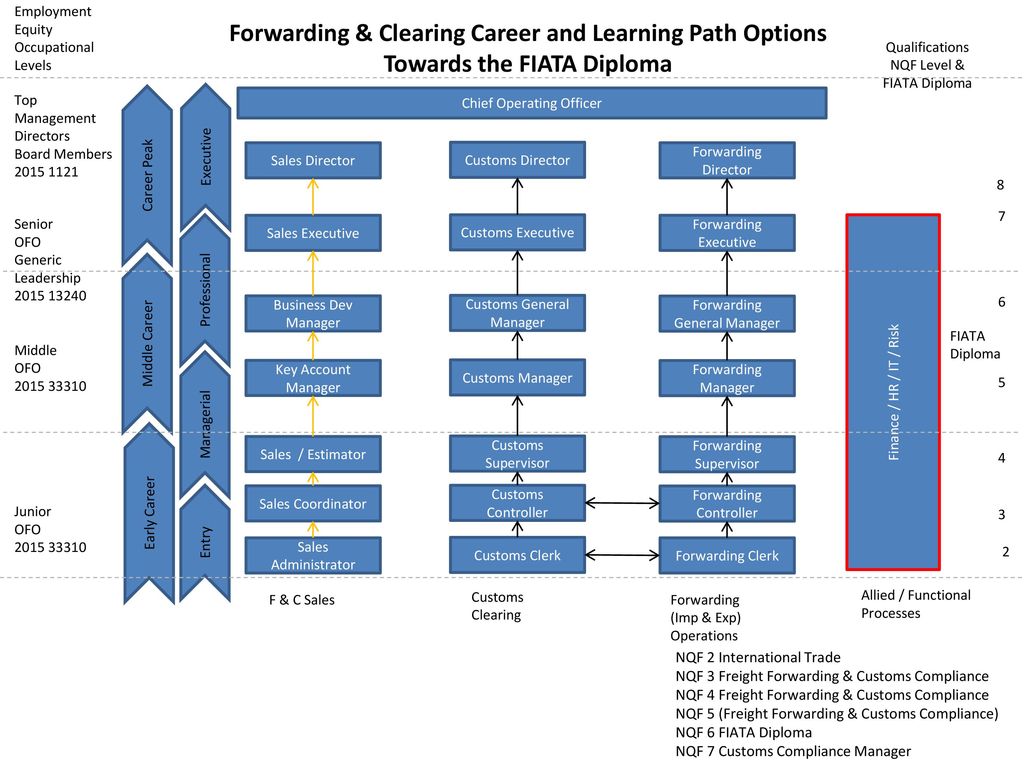
In order to engage stakeholders in a sustainable supply chain, companies should carefully select the metrics they are interested in tracking. When choosing metrics, it is important to consider the environmental and social aspects of a company. Environmental and social metrics can be difficult to measure for any company. Engagement can be difficult because many stakeholders might not know about the company's sustainability efforts.
Managing sustainable procurement
Any company must manage sustainable procurement. It is essential to ensure transparency in the supply chain and that Tier 1 suppliers are accountable for sustainable practices. However, some organizations have trouble implementing sustainable practices because they don't have full visibility into their supply chains. EcoVadis conducted a survey and found that half of the organizations did not have full visibility into supply chains. 28% of those surveyed didn't even have such visibility. Implementing sustainability measures can take many years. However, organizations can start with small wins like auditing suppliers.
The procurement team can make sustainable procurement a part of every procurement process. This helps to reduce risk, identify incremental improvements and ensures that internal customers understand the impact of purchases. For true sustainability to be achieved, organizations must look beyond the traditional options available and find new ways to procure sustainable goods. For example, they need to work with their suppliers in a new way, acquire new technical skills and have sufficient data and information for their goals.
Social responsibility management
A sustainable supply chain must include social responsibility management (CSR). CSR principles must be applied at all levels of the supply chains. Businesses must collaborate to ensure that their products and services do not adversely affect the environment. This includes assessing product lifecycle phases, developing re-use strategies, and developing transportation capabilities. Companies must also consider the needs of their customers and comply with all applicable regulations.
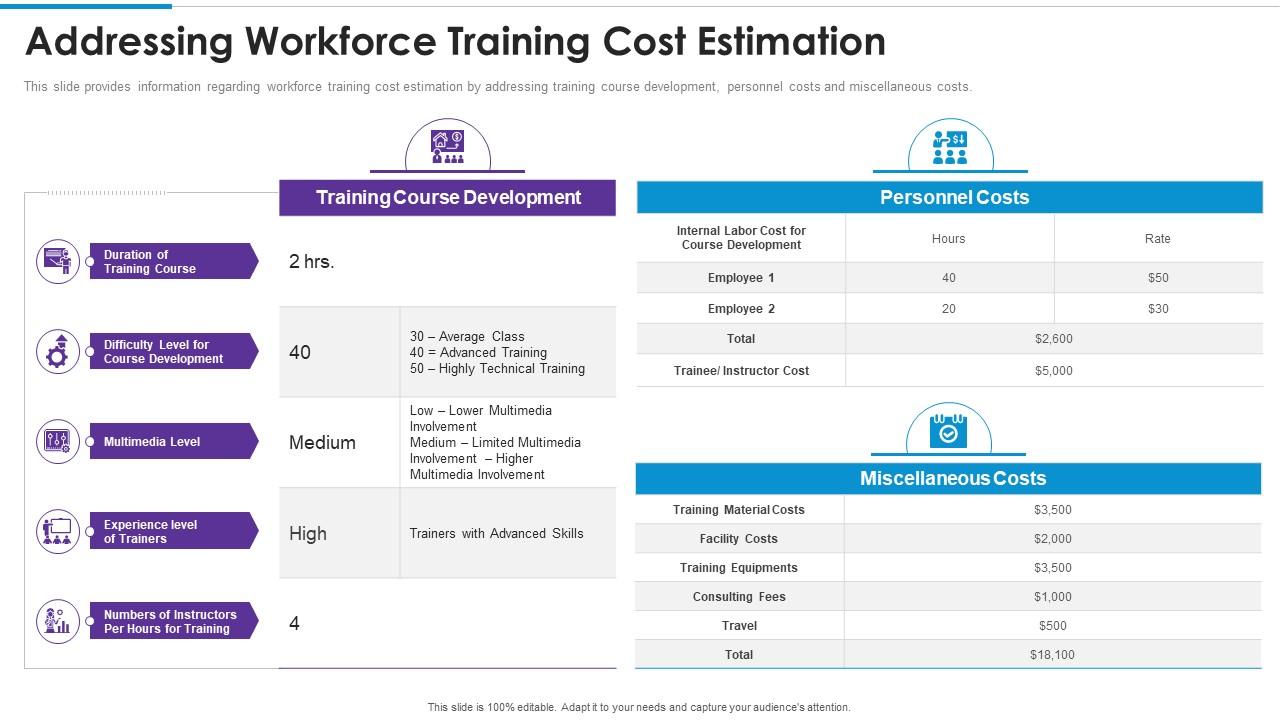
Sustainability is not only about meeting current needs while not compromising the future, but it also includes social, economic and environmental issues. Social responsibility is a commitment of a business to conduct business ethically, to benefit its workforce, local community, society, and the wider world.
FAQ
What are some common mistakes managers make?
Managers sometimes make their own job harder than necessary.
They may not delegate enough responsibilities and not provide sufficient support.
Many managers lack the communication skills to motivate and lead their employees.
Managers set unrealistic expectations and make it difficult for their team.
Managers may choose to solve every problem all by themselves, instead of delegating to others.
What kind of people use Six Sigma
People who have worked with statistics and operations research will usually be familiar with the concepts behind six sigma. But anyone can benefit from it.
Because it requires a high level of commitment, only those with strong leadership skills will make an effort necessary to implement it successfully.
What's the difference between a program and a project?
A program is permanent, whereas a project is temporary.
Projects usually have a goal and a deadline.
It is often performed by a team of people, who report back on someone else.
A program is usually defined by a set or goals.
It is often implemented by one person.
Statistics
- This field is expected to grow about 7% by 2028, a bit faster than the national average for job growth. (wgu.edu)
- 100% of the courses are offered online, and no campus visits are required — a big time-saver for you. (online.uc.edu)
- UpCounsel accepts only the top 5 percent of lawyers on its site. (upcounsel.com)
- The average salary for financial advisors in 2021 is around $60,000 per year, with the top 10% of the profession making more than $111,000 per year. (wgu.edu)
- The BLS says that financial services jobs like banking are expected to grow 4% by 2030, about as fast as the national average. (wgu.edu)
External Links
How To
How do I do the Kaizen Method?
Kaizen means continuous improvement. This Japanese term refers to the Japanese philosophy of continuous improvement that emphasizes incremental improvements and constant improvement. This is a collaborative process in which people work together to improve their processes continually.
Kaizen is one of Lean Manufacturing's most efficient methods. Employees responsible for the production line should identify potential problems in the manufacturing process and work together to resolve them. This increases the quality of products and reduces the cost.
Kaizen is an approach to making every worker aware and alert to what is happening around them. Correct any errors immediately to avoid future problems. If someone spots a problem while at work, they should immediately report it to their manager.
There are some basic principles that we follow when doing kaizen. We always start from the end product and move toward the beginning. For example, if we want to improve our factory, we first fix the machines that produce the final product. Then, we fix the machines that produce components and then the ones that produce raw materials. Then, we fix those who work directly with the machines.
This approach is called 'kaizen' because it focuses on improving everything steps by step. When we are done fixing the whole factory, we go back to the beginning and continue until we reach perfection.
Before you can implement kaizen into your business, it is necessary to learn how to measure its effectiveness. There are several ways to determine whether kaizen is working well. One way is to examine the amount of defects on the final products. Another way is to check how much productivity has grown since kaizen was implemented.
To determine if kaizen is effective, you should ask yourself why you chose to implement kaizen. It was because of the law, or simply because you wanted to save some money. Did you really believe it would lead to success?
Congratulations! Now you're ready for kaizen.