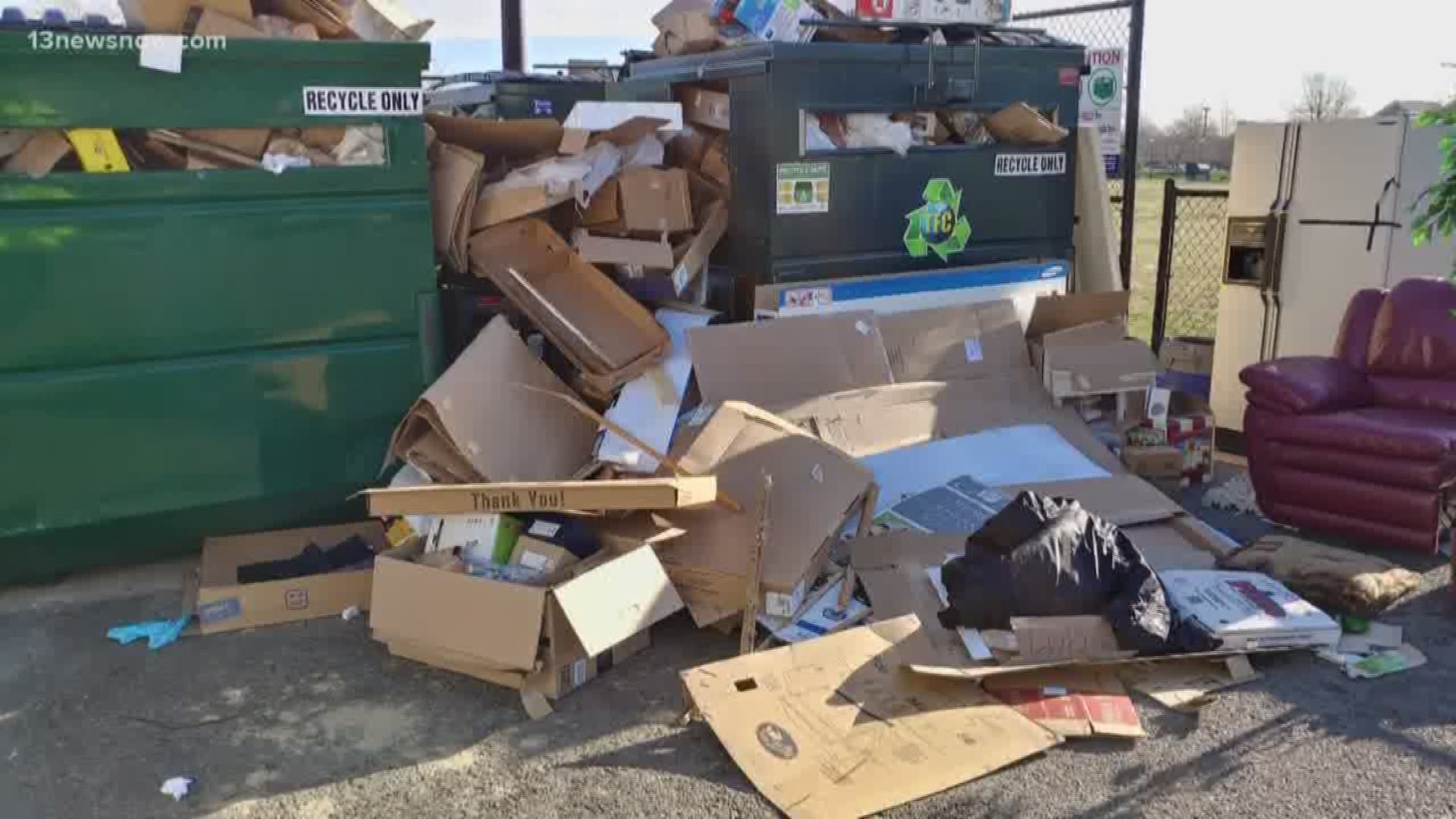
A business flow metric doesn't capture the inherent directionality or directionality supply networks. There are many levels of dependencies in a supply network, and they often interact. Further, a business flow measure does not reflect the natural directionality in information flows within a given network. These issues are essential to developing a digital supply chain.
Sustainability
Multinational corporations need to ensure sustainability of their supply chains. Many companies have made sustainability their top priority and committed to using sustainable suppliers. However, many lower-level suppliers do not follow sustainability standards, posing serious risks for businesses. This article examines three major MNCs' supply networks. The authors found some best practices that companies could adopt to counter this problem. These include including lower-tier suppliers into the sustainability strategy and setting long-term sustainability objectives.
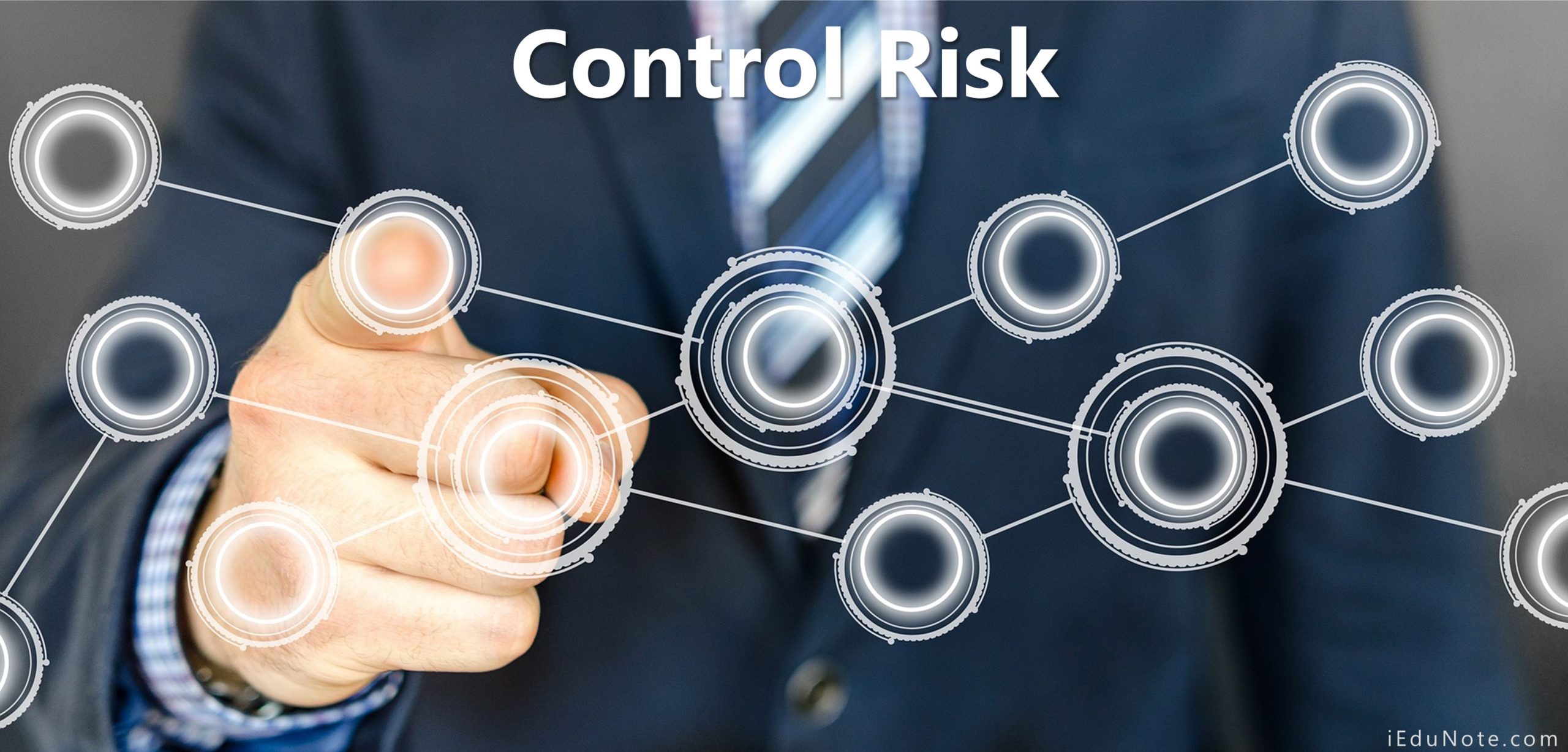
Companies should set goals and measure progress to show improvement in their supply chains. They should also engage all stakeholders across the supply chain, including the internal staff driving change and consumers. The ultimate goal is to communicate the business benefits of sustainable supply network and establish the right governance and organizational structures to ensure sustainability efforts succeed.
Vertical disintegration in supply chains
Companies can suffer from vertical disintegration in supply chains. Not only can it lead to higher costs and greater losses, but it can also affect organisational structures. To improve their overall competitiveness, some companies might choose to decrease their involvement in upstream and downstream activities. However, this is not always a good idea and should only be done in exceptional circumstances.
The key disadvantage of vertical integration is that it limits a company's flexibility. Because it makes it follow specific trends, vertical integration can be detrimental to a company's flexibility. It may prove difficult for retailers to adopt new technology if their competition already uses it. If this were to be the case, then the parent company would have need to invest in the technology to keep up to date with the competition. Rapidly changing technologies can make integration difficult. Furthermore, companies often face challenges integrating different technologies from different parts of their supply chains, which can be costly.
Performance implications of a digital supply network
Digital supply chains can have many benefits. They are more efficient, resilient, and cost-savings. However, they can also increase cybersecurity risk. However, there are several approaches companies can use to mitigate these risks. Let's look at some. These methods involve data analytics. Businesses can use this technology to gain insight into customer needs and improve their products. Companies can use the shared data to predict potential problems and make more informed decisions by incorporating information from multiple sources.
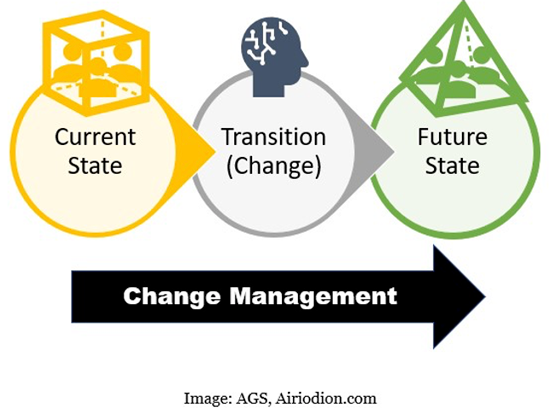
Assessing your current supply chain is the first step to digitalization. This will help you identify and mitigate any risks or issues, as well any potential complications. Then, you can develop an action plan to minimize any risks. Collaboration with your partners is crucial once you have an idea of what you want from the digital supply chain. You will be able to make sure that everyone benefits from the new digital supply system.
FAQ
What role can a manager fill in a company’s management?
Each industry has a different role for a manager.
A manager generally manages the day to-day operations in a company.
He/she makes sure that the company meets its financial obligations, and that it produces goods or services that customers desire.
He/she makes sure that employees adhere to the rules and regulations as well as quality standards.
He/she designs new products or services and manages marketing campaigns.
What are the steps of the management decision-making process?
Managers face complex and multifaceted decision-making challenges. It involves many factors, including but not limited to analysis, strategy, planning, implementation, measurement, evaluation, feedback, etc.
Management of people requires that you remember that they are just as human as you are, and can make mistakes. There is always room to improve, especially if your first priority is to yourself.
This video will explain how decision-making works in Management. We discuss different types of decisions as well as why they are important and how managers can navigate them. Here are some topics you'll be learning about:
What is a fundamental management tool for decision-making?
A decision matrix is an easy but powerful tool to aid managers in making informed decisions. It allows them to consider all possible solutions.
A decision matrix is a way of representing alternatives as rows and columns. This allows one to see how each alternative impacts other options.
In this example, we have four possible alternatives represented by the boxes on the left side of the matrix. Each box represents a different option. The top row depicts the current status quo, while the bottom row represents what would happen if no action was taken.
The middle column displays the impact of selecting Option 1. It would translate into an increase in sales from $2million to $3million.
These are the results of selecting Options 2 or 3. These are positive changes - they increase sales by $1 million and $500 thousand respectively. These changes can also have negative effects. Option 2 can increase costs by $100 million, while Option 3 can reduce profits by $200,000.
The last column displays the results of selecting Option 4. This would result in a reduction of sales of $1 million.
The best thing about using a decision matrix is that you don't need to remember which numbers go where. You can just glance at the cells and see immediately if one given choice is better.
This is because the matrix has done all the hard work. It is as simple as comparing the numbers within the relevant cells.
Here is an example of how a decision matrix might be used in your business.
It is up to you to decide whether to spend more money on advertising. If you do this, you will be able to increase revenue by $5000 per month. You will still have to pay $10000 per month in additional expenses.
By looking at the cell just below "Advertising", the net result can be calculated as $15 thousand. Advertising is worth much more than the investment cost.
What's the difference between a program and a project?
A project is temporary while a programme is permanent.
A project typically has a defined goal and deadline.
This is often done by a group of people who report to one another.
A program is usually defined by a set or goals.
It is typically done by one person.
Statistics
- This field is expected to grow about 7% by 2028, a bit faster than the national average for job growth. (wgu.edu)
- Hire the top business lawyers and save up to 60% on legal fees (upcounsel.com)
- Your choice in Step 5 may very likely be the same or similar to the alternative you placed at the top of your list at the end of Step 4. (umassd.edu)
- The BLS says that financial services jobs like banking are expected to grow 4% by 2030, about as fast as the national average. (wgu.edu)
- Our program is 100% engineered for your success. (online.uc.edu)
External Links
How To
What is Lean Manufacturing?
Lean Manufacturing uses structured methods to reduce waste, increase efficiency and reduce waste. They were created by Toyota Motor Corporation in Japan in the 1980s. The main goal was to produce products at lower costs while maintaining quality. Lean manufacturing focuses on eliminating unnecessary steps and activities from the production process. It consists of five basic elements: pull systems, continuous improvement, just-in-time, kaizen (continuous change), and 5S. Pull systems involve producing only what the customer wants without any extra work. Continuous improvement involves constantly improving upon existing processes. Just-in–time refers when components or materials are delivered immediately to their intended destination. Kaizen means continuous improvement, which is achieved by implementing small changes continuously. Finally, 5S stands for sort, set in order, shine, standardize, and sustain. These five elements are combined to give you the best possible results.
Lean Production System
Six key concepts are the basis of lean production:
-
Flow - The focus is on moving information and material as close as possible to customers.
-
Value stream mapping - Break down each stage in a process into distinct tasks and create an overview of the whole process.
-
Five S’s - Sorted, In Order. Shine. Standardize. And Sustain.
-
Kanban: Use visual signals such stickers, colored tape, or any other visual cues, to keep track your inventory.
-
Theory of constraints - identify bottlenecks in the process and eliminate them using lean tools like kanban boards;
-
Just-in-time - deliver components and materials directly to the point of use;
-
Continuous improvement - incremental improvements are made to the process, not a complete overhaul.