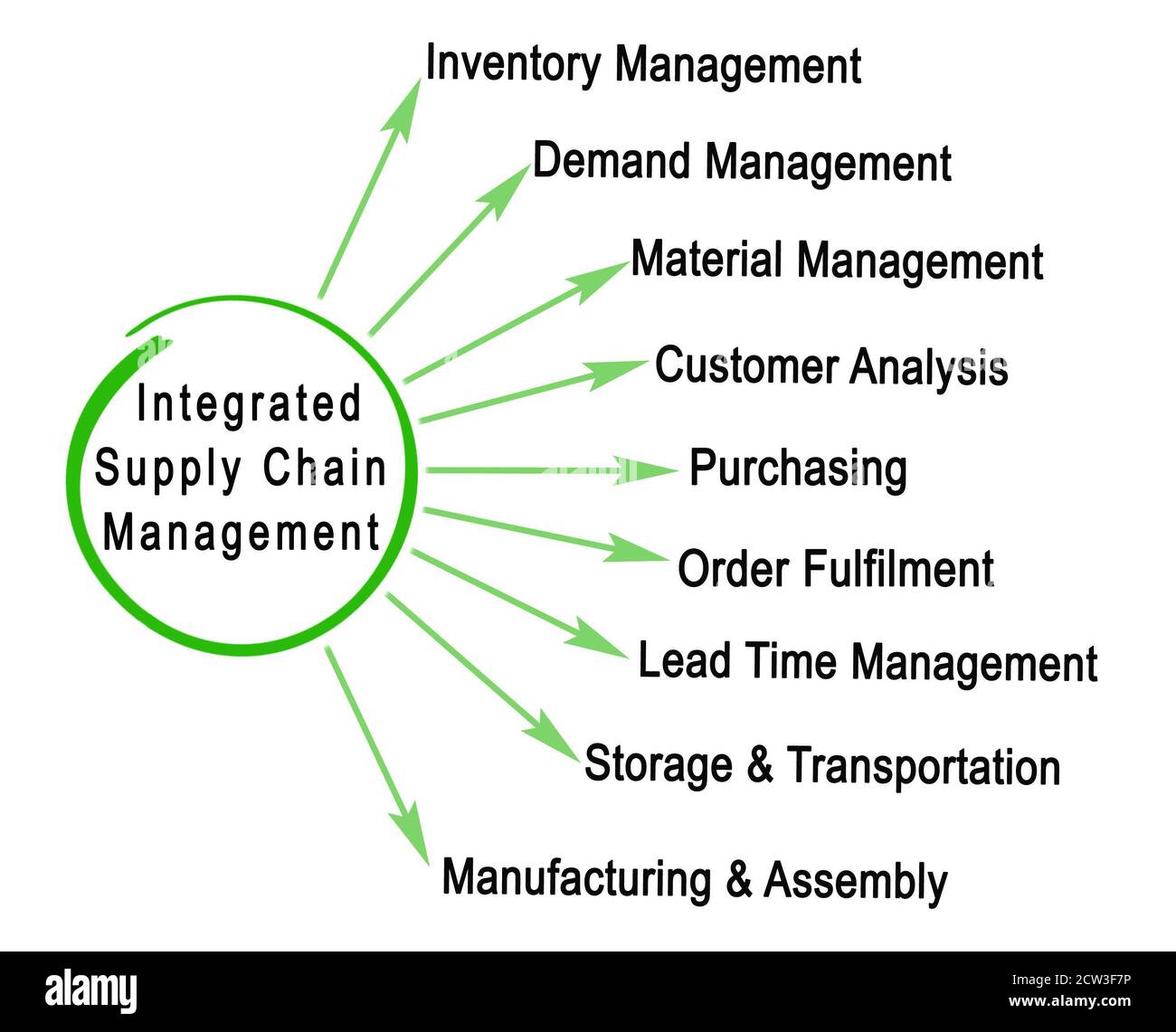
Business Process Reengineering is a method that allows cross-functional teams of people to collaborate to optimize business processes. It allows companies to gather and disseminate greater data, which is essential for sound improvements in customer services. Additionally, BPR helps organizations to implement optimized business processes faster and eliminate unproductive activities.
Taco Bell's reengineering of its business process is a lesson learned
Taco Bell's business processes re-engineering program was instrumental in driving a dramatic increase of sales. In just 10 years, the company saw a dramatic increase in sales from less than 500m in 1982 to over $3 billion. They improved customer service and eliminated unnecessary paperwork. Additionally, the company was able to eliminate a lot of time that was spent on administration. This resulted in a decrease in costs and a rise of employee morale.
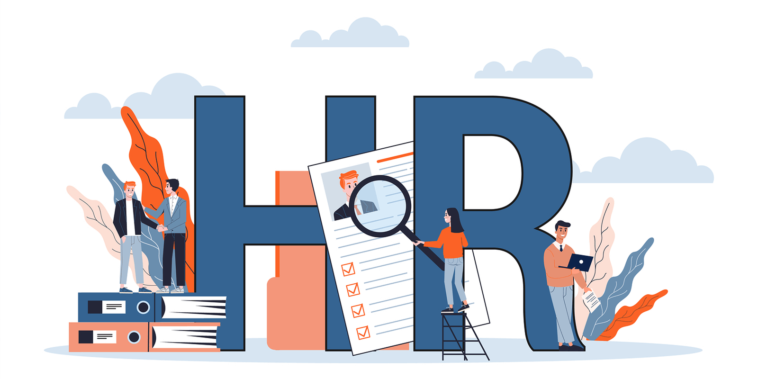
The new Defy drive through concept by Taco Bell, featuring a digital first experience, is one example of how Taco Bell has adapted for the digital revolution in food. The new concept is intended to be both memorable and efficient in order to attract customers. The company has great branding opportunities thanks to the new concept. Brands don't always have the funds to invest in such a transformative project. However, they can reimagine their offerings and create better customer experiences.
Taco Bell's innovative mobile ordering approach is another example. Taco Bell and Roadtrip Nation have teamed up to create an online community, where employees can share their stories with one another. This community allows employees to learn from one another, inspiring future team members.
Benefits of business process reengineering
Companies can improve efficiency and cut costs by performing business process redesign. Inefficient processes can cause delays in operations, which can lead to increased expenses and slow down the business. Reengineering business processes can improve the quality and quantity of services and products. This will improve customer satisfaction which in turn will boost the return on investment for BPR projects.
During the reengineering process, companies must empower workers and improve their overall satisfaction. This will improve employee satisfaction and customer satisfaction. Moreover, companies have to consider additional factors when hiring new workers. For example, workers must be able to handle multiple tasks and be "All-rounders".
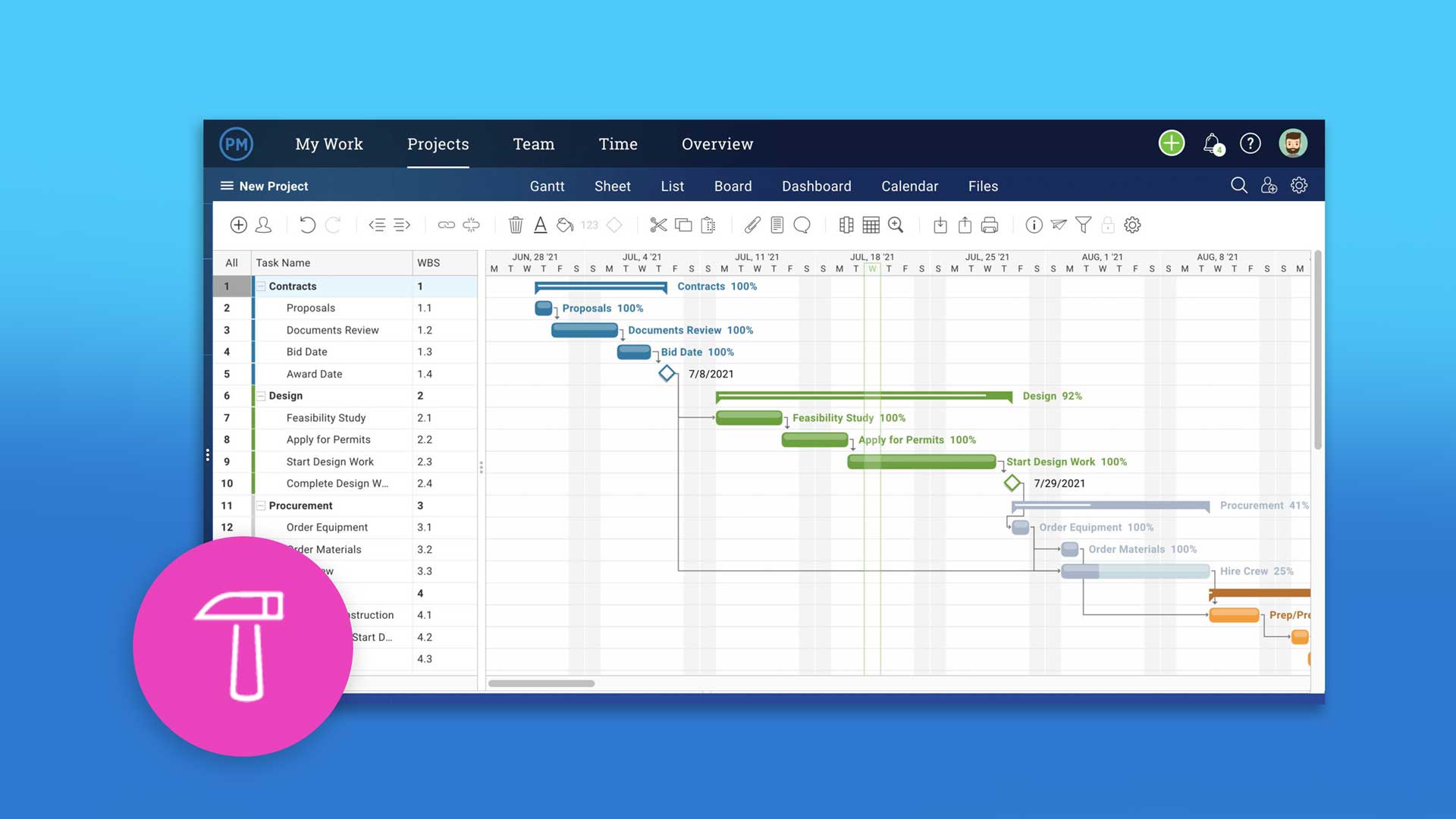
It is important to have a compelling business case and strong staff buy in before starting a BPR campaign. For a successful implementation, executive sponsorship is crucial. You must also have the right team of experts in the field. It is possible that you will need a team that is familiar with the business and the methods. Additionally, it is important to have a good IT infrastructure, which will facilitate the transformation of processes.
FAQ
What are the key management skills?
Management skills are essential for any business owner, whether they're running a small local store or an international corporation. They include the ability to manage people, finances, resources, time, and space, as well as other factors.
These skills are necessary for setting goals and objectives as well as planning strategies, leading groups, motivating employees and solving problems.
You can see that there are many managerial duties.
How do you manage your employees effectively?
Effectively managing employees requires that you ensure their happiness and productivity.
This includes setting clear expectations for their behavior and tracking their performance.
To do this successfully, managers need to set clear goals for themselves and for their teams.
They should communicate clearly to staff members. They also need to make sure that they discipline and reward the best performers.
They must also keep records of team activities. These include:
-
What was accomplished?
-
What was the work involved?
-
Who did it all?
-
What was the moment it was completed?
-
Why it was done?
This information is useful for monitoring performance and evaluating the results.
What is the difference between Six Sigma Six Sigma and TQM?
The major difference between the two tools for quality management is that six Sigma focuses on eliminating defect while total quality control (TQM), on improving processes and decreasing costs.
Six Sigma can be described as a strategy for continuous improvement. This approach emphasizes eliminating defects through statistical methods like control charts, Pareto analysis, and p-charts.
The goal of this method is to reduce variation in product output. This is done by identifying and correcting the root causes of problems.
Total quality management includes monitoring and measuring all aspects of an organization's performance. It also involves training employees to improve performance.
It is often used to increase productivity.
What are the steps to take in order to make a management decision?
The decision-making process of managers is complicated and multifaceted. It involves many factors, including but not limited to analysis, strategy, planning, implementation, measurement, evaluation, feedback, etc.
The key thing to remember when managing people is that they are human beings just as you are and therefore make mistakes. You can always improve your performance, provided you are willing to make the effort.
This video explains the process of decision-making in Management. We will explain the importance of different types decisions and how every manager can make them. These topics are covered in this course:
What are the main four functions of management
Management is responsible for planning, organizing, directing, and controlling people and resources. It also includes developing policies and procedures and setting goals.
Organizations can achieve their goals through management. This includes leadership, coordination, control and motivation.
Management's four main functions are:
Planning - Planning involves determining what needs to be done.
Organizing – Organizing means deciding how to organize things.
Direction - This is the art of getting people to follow your instructions.
Controlling – Controlling is the process of ensuring that tasks are completed according to plan.
What are the five management steps?
The five stages of any business are planning, execution, monitoring, review, and evaluation.
Setting goals for the future requires planning. Planning involves defining your goals and how to get there.
Execution is the actual execution of the plans. These plans must be adhered to by everyone.
Monitoring is the act of monitoring your progress towards achieving your targets. Regular reviews of performance against budgets and targets should be part of this process.
Reviews take place at the end of each year. They give you an opportunity to review the year and assess how it went. If not, then it may be possible to make adjustments in order to improve performance next time.
After the annual review is complete, evaluations are conducted. It helps identify what worked well and what didn't. It also provides feedback on the performance of people.
What are management theories?
Management Concepts are the management principles and practices that managers use in managing people and resources. These include topics such as human resource policies and job descriptions, performance assessments, training programs and employee motivation.
Statistics
- As of 2020, personal bankers or tellers make an average of $32,620 per year, according to the BLS. (wgu.edu)
- The profession is expected to grow 7% by 2028, a bit faster than the national average. (wgu.edu)
- Your choice in Step 5 may very likely be the same or similar to the alternative you placed at the top of your list at the end of Step 4. (umassd.edu)
- Our program is 100% engineered for your success. (online.uc.edu)
- The BLS says that financial services jobs like banking are expected to grow 4% by 2030, about as fast as the national average. (wgu.edu)
External Links
How To
How do I do the Kaizen Method?
Kaizen means continuous improvement. The Japanese philosophy emphasizes small, incremental improvements to achieve continuous improvement. This term was created by Toyota Motor Corporation in 1950. It's where people work together in order to improve their processes constantly.
Kaizen is one of the most effective methods used in Lean Manufacturing. In this concept, employees who are responsible for the production line must identify problems that exist during the manufacturing process and try to solve them before they become big issues. This will increase the quality and decrease the cost of the products.
Kaizen is the idea that every worker should be aware of what is going on around them. To prevent problems from happening, any problem should be addressed immediately. So, if someone notices a problem while working, he/she should report it to his/her manager.
Kaizen has a set of basic principles that we all follow. When working with kaizen, we always start with the end result and move towards the beginning. We can improve the factory by first fixing the machines that make it. Next, we repair the machines that make components. Then, the machines that make raw materials. We then fix the workers that work with those machines.
This is why it's called "kaizen" because it works step-by-step to improve everything. We finish fixing the factory and then go back to the beginning. This continues until we achieve perfection.
It is important to understand how to measure the effectiveness and implementation of kaizen in your company. There are many ways to tell if kaizen is effective. One method is to inspect the finished products for defects. Another method is to determine how much productivity has improved since the implementation of kaizen.
To determine if kaizen is effective, you should ask yourself why you chose to implement kaizen. Did you do it because it was legal or to save money? You really believed it would make you successful?
Congratulations! Now you're ready for kaizen.